Inductor warm-pressing forming method and inductor prepared by using same
A technology of warm pressing and compression molding, which is applied in the manufacture of inductors/transformers/magnets, components of transformers/inductors, circuits, etc. It can solve problems such as low production efficiency, high energy consumption per unit of production, and affect applications, and achieve heating The effect of short time, few appearance defects and uniform heating
- Summary
- Abstract
- Description
- Claims
- Application Information
AI Technical Summary
Problems solved by technology
Method used
Image
Examples
Embodiment 1
[0040] Embodiment 1, the granules obtained by granulation need to be molded to become an inductor core and an inductor. as attached figure 1 As shown, the mold consists of four parts:
[0041] (1) Forming mechanism
[0042]This part is composed of cavity, upper punch 1 and lower punch 2. The shape of the cavity 3 and the punch depends on the product, and can be in any shape in theory, and the usual shapes include circular ring, cylinder, cube, cuboid and the like. The cavity is the space where the metal soft magnetic powder is finally formed, and the density of the powder increases gradually under the pressure of the punch until it is finally formed.
[0043] During the powder molding process, the powder needs to overcome the friction between the powder and the mold wall, the internal friction between the powders and the pressure required for the deformation of the powder, etc. Usually it can be achieved by applying sufficient molding pressure, but because too much pressur...
Embodiment 2
[0051] In the second embodiment, the powder obtained by granulation needs to be molded into a molded inductor. Such as figure 1 As shown, the mold consists of three parts:
[0052] (1) Forming mechanism
[0053] There are two structures of the forming mechanism, the first form will be introduced first:
[0054] This part includes an upper die 11 , a lower die 12 and a middle die 13 ; the upper die 11 includes an upper punch 1 ; the lower die 12 includes a lower punch 2 . The shape of the cavity 3 and the punch depends on the product, and can be in any shape in theory, and the usual shapes include cylinder, cube, cuboid and the like. The cavity is the space where the metal soft magnetic powder is finally formed, and the density of the powder increases gradually under the pressure of the punch until it is finally formed.
[0055] Before filling the powder, the inductance coil is first placed in the middle mold 13, and the two outgoing legs of the coil 4 are placed in the gro...
PUM
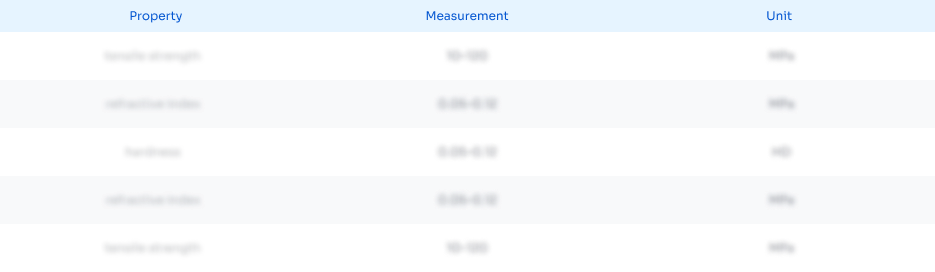
Abstract
Description
Claims
Application Information

- R&D Engineer
- R&D Manager
- IP Professional
- Industry Leading Data Capabilities
- Powerful AI technology
- Patent DNA Extraction
Browse by: Latest US Patents, China's latest patents, Technical Efficacy Thesaurus, Application Domain, Technology Topic, Popular Technical Reports.
© 2024 PatSnap. All rights reserved.Legal|Privacy policy|Modern Slavery Act Transparency Statement|Sitemap|About US| Contact US: help@patsnap.com