Puncture-resistance nylon composite film
A composite film, puncture-resistant technology, applied in the field of materials, can solve the problems of nylon layer damage, affecting the packaging barrier performance, etc., and achieve the effect of good packaging material, high oxygen resistance, and high puncture resistance.
- Summary
- Abstract
- Description
- Claims
- Application Information
AI Technical Summary
Problems solved by technology
Method used
Examples
Embodiment 1
[0012] A puncture-resistant nylon composite film, comprising the following raw material components in parts by weight: 60 parts of nylon, 15 parts of nitrocellulose resin, 14 parts of corundum fine powder, 9 parts of melamine cyanurate, 6 parts of silicon carbide, 12 parts of boron carbide, 23 parts of glass fiber, 3 parts of aluminum oxide, 1 part of titanium dioxide, 0.5 part of antimony trioxide, 1 part of benzoin ether, 7 parts of nano-montmorillonite, 1.2 parts of tetrabutyl titanate, ramie 12 parts of bone marrow, 2 parts of gelatin, 1 part of magnesium stearate, 13 parts of acetyl tributyl citrate, 1 part of 2,6-di-tert-butyl-4-methylphenol, 4 parts of 3-hydroxybenzoic acid , 1 part of lauryl alcohol sulfate, 4 parts of plant saponins.
[0013] The preparation method of the present invention is the same as the prior art.
Embodiment 2
[0015] A puncture-resistant nylon composite film, comprising the following raw material components in parts by weight: 70 parts of nylon, 20 parts of nitrocellulose resin, 20 parts of corundum fine powder, 13 parts of melamine cyanurate, 12 parts of silicon carbide, 25 parts of boron carbide, 29 parts of glass fiber, 7 parts of aluminum oxide, 3 parts of titanium dioxide, 2 parts of antimony trioxide, 2 parts of benzoin ether, 9 parts of nano-montmorillonite, 1.4 parts of tetrabutyl titanate, ramie 14 parts of bone marrow, 3 parts of gelatin, 2 parts of magnesium stearate, 15 parts of acetyl tributyl citrate, 1.5 parts of 2,6-di-tert-butyl-4-methylphenol, 6 parts of 3-hydroxybenzoic acid , 2 parts of lauryl alcohol sulfate, 6 parts of plant saponins.
[0016] The preparation method of the present invention is the same as the prior art.
Embodiment 3
[0018] A puncture-resistant nylon composite film, comprising the following raw material components in parts by weight: 65 parts of nylon, 18 parts of nitrocellulose resin, 16 parts of corundum fine powder, 10 parts of melamine cyanurate, 10 parts of silicon carbide, 18 parts of boron carbide, 25 parts of glass fiber, 5 parts of aluminum oxide, 2 parts of titanium dioxide, 1 part of antimony trioxide, 1 part of benzoin ether, 8 parts of nano-montmorillonite, 1.3 parts of tetrabutyl titanate, ramie 13 parts of bone marrow, 2 parts of gelatin, 1 part of magnesium stearate, 14 parts of acetyl tributyl citrate, 1 part of 2,6-di-tert-butyl-4-methylphenol, 5 parts of 3-hydroxybenzoic acid , 1 part of lauryl alcohol sulfate, 5 parts of plant saponins.
PUM
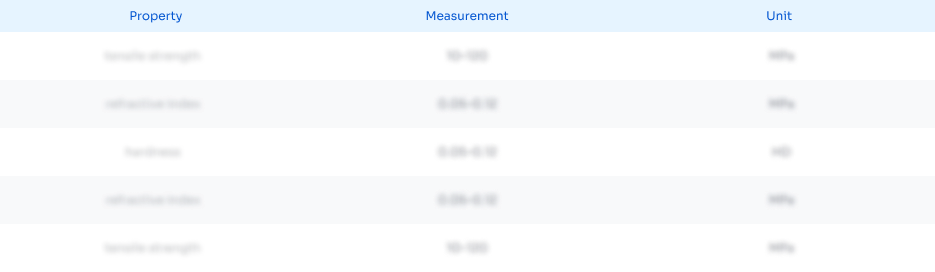
Abstract
Description
Claims
Application Information

- R&D Engineer
- R&D Manager
- IP Professional
- Industry Leading Data Capabilities
- Powerful AI technology
- Patent DNA Extraction
Browse by: Latest US Patents, China's latest patents, Technical Efficacy Thesaurus, Application Domain, Technology Topic, Popular Technical Reports.
© 2024 PatSnap. All rights reserved.Legal|Privacy policy|Modern Slavery Act Transparency Statement|Sitemap|About US| Contact US: help@patsnap.com