Preparation method of superfine boron carbide spray granulation powder
A technology of spray granulation and boron carbide powder, applied in the field of nanomaterial processing, can solve the problems of increasing waste water, high cost, low density of boron carbide, etc., and achieve the effects of improving sintering density, short production cycle and low production cost
- Summary
- Abstract
- Description
- Claims
- Application Information
AI Technical Summary
Problems solved by technology
Method used
Image
Examples
Embodiment
[0036] 1) Mix 55 kg of boron carbide powder with a particle size not greater than 500um and 45 kg of deionized water with compressed air, add 110 g of polycarboxylate sodium saline dispersant after 30 minutes, and continue to pass compressed air for 1 hour;
[0037] 2) Add the nearly spherical boron carbide particles with a particle size of 0.5-1mm into the grinding chamber of the grinding machine provided with the ball adding port, the addition of the nearly spherical boron carbide particles accounts for 70%-80% of the grinding chamber, start the main motor and Slurry pump, start grinding;
[0038] 3) Every 1 hour of grinding, add nearly spherical boron carbide particles and deionized water to the initial state; after grinding for 50 hours, use a Coulter laser particle size analyzer to detect the particle size of the slurry every 3 hours until the boron carbide particles are ground to a particle size of Stop after 0.4-0.5um, discharge the slurry and pass through a 500-mesh wa...
PUM
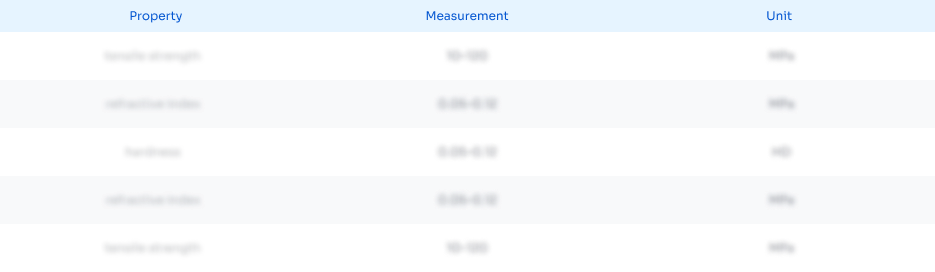
Abstract
Description
Claims
Application Information

- R&D Engineer
- R&D Manager
- IP Professional
- Industry Leading Data Capabilities
- Powerful AI technology
- Patent DNA Extraction
Browse by: Latest US Patents, China's latest patents, Technical Efficacy Thesaurus, Application Domain, Technology Topic, Popular Technical Reports.
© 2024 PatSnap. All rights reserved.Legal|Privacy policy|Modern Slavery Act Transparency Statement|Sitemap|About US| Contact US: help@patsnap.com