Heat-curable magnetic epoxy resin powder and inductor packaging method thereof
A technology of epoxy resin powder and epoxy resin, which is applied in epoxy resin coatings, transformer/inductor parts, powder coatings, etc., to achieve the effects of reducing electromagnetic interference, having electromagnetic shielding functions, and less material waste
- Summary
- Abstract
- Description
- Claims
- Application Information
AI Technical Summary
Problems solved by technology
Method used
Examples
example 1
[0028] A thermosetting epoxy resin powder coating, comprising the following substances: bisphenol A and bisphenol A modified epoxy resin 1kg, nickel zinc ferrite magnetic powder 1kg, composite curing agent 0.6KG, filler 0.21KG, auxiliary agent 0.2 KG, the weight percentage of each component is: 33.2%, 33.2%, 20%, 7%, 6.6%, after mixing the above materials in proportion, stir them evenly with a stirring device, and then extrude them into flakes The dry material is then pulverized, and then sieved and classified to obtain a heat-curing epoxy resin powder coating;
[0029] The preparation method of the nickel-zinc ferrite magnetic powder is to directly burn the nickel-zinc ferrite powder after pre-baking without processing and molding, and the fired nickel-zinc ferrite magnetic powder is in a loose form Powder, crushed or sieved according to the actual situation to obtain nickel-zinc ferrite magnetic powder; the filler is any one or a mixture of two of silicon dioxide and aluminu...
Embodiment 2
[0036] A heat-curing epoxy resin powder coating comprises the following substances: 1.2 kg of epoxy phenolic resin, 1 kg of manganese-zinc ferrite magnetic powder, 0.6 kg of composite curing agent, 0.1 kg of filler, and 0.1 kg of auxiliary agent. The weight percentage of each component is: 40%, 33.3%, 20%, 3.3%, 3.3%. After the above substances are mixed in proportion, they are stirred evenly with a stirring device, and then extruded to form a sheet-like dry material. , then through powder, and then through sieving and classification to obtain heat-curing epoxy resin powder coating;
[0037] The manganese-zinc ferrite magnetic powder is prepared by the following method: the magnetic powder containing water after grinding the magnetic core of the switching power supply transformer is dried in an oven, and the dried manganese-zinc ferrite magnetic powder is obtained by pulverizing with a fine pulverizer, According to actual needs, use metal screen machines with different meshes ...
PUM
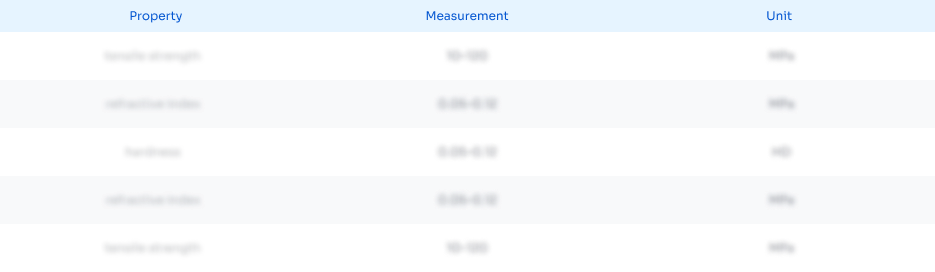
Abstract
Description
Claims
Application Information

- R&D
- Intellectual Property
- Life Sciences
- Materials
- Tech Scout
- Unparalleled Data Quality
- Higher Quality Content
- 60% Fewer Hallucinations
Browse by: Latest US Patents, China's latest patents, Technical Efficacy Thesaurus, Application Domain, Technology Topic, Popular Technical Reports.
© 2025 PatSnap. All rights reserved.Legal|Privacy policy|Modern Slavery Act Transparency Statement|Sitemap|About US| Contact US: help@patsnap.com