Surface anti-corrosion treatment technology for aluminum fuel tanks
An anti-corrosion and fuel tank technology, which is applied to special surfaces, pretreated surfaces, surface reaction electrolytic coatings, etc., can solve the problems of unreliable surface treatment technology, few surface treatment technologies, and unsatisfactory anti-corrosion effect. To achieve the effect of good decoration, low cost and tight bonding
- Summary
- Abstract
- Description
- Claims
- Application Information
AI Technical Summary
Problems solved by technology
Method used
Examples
Embodiment 1
[0014] Embodiment 1: a kind of aluminum fuel tank surface anti-corrosion treatment technology, comprises the steps:
[0015] A1 Degreasing: Put the oil tank to be degreased into the mixture prepared by 2 parts by weight of sodium carbonate, 1 part of sodium bicarbonate, 1 part of sodium silicate, 2 parts of sodium phosphate, 1 part of surfactant and 90 parts of deionized water. Soak in the weak alkaline degreasing solution for 10 minutes. After the degreasing is completed, rinse the surface of the fuel tank with clean water, drain the water stains, and dry at 50°C for 25 minutes until the fuel tank is completely dry;
[0016] A2 Chemical polishing: Cover the aluminum fuel tank with the end cap, immerse in the polishing solution for 3 minutes, then take out the fuel tank, drain the water stains after cleaning, and dry at 50°C for 25 minutes until the fuel tank is completely dry; the polishing solution is composed of 80 parts of phosphoric acid, sulfuric acid 32 parts, 12 parts ...
Embodiment 2
[0020] Embodiment 2: a kind of aluminum fuel tank surface anti-corrosion treatment technology, comprises the steps:
[0021] B1 Degreasing: put the oil tank to be degreased into the preparation by weight parts of 3 parts of sodium carbonate, 1.5 parts of sodium bicarbonate, 1.5 parts of sodium silicate, 2.5 parts of sodium phosphate, 1.5 parts of surfactant and 95 parts of deionized water Soak in the weak alkaline degreasing solution for 15 minutes. After degreasing is completed, rinse the surface of the fuel tank with clean water, drain the water stains, and dry at 55°C for 25 minutes until the fuel tank is completely dry;
[0022] B2 chemical polishing: cover the aluminum fuel tank with the end cap, immerse in the polishing solution for 4 minutes, then take out the fuel tank, drain the water stains after cleaning, and dry at 55°C for 20 minutes until the fuel tank is completely dry; the polishing solution is composed of 89 parts of phosphoric acid, sulfuric acid 45 parts, 13...
Embodiment 3
[0026] Embodiment 3: a kind of aluminum fuel tank surface anti-corrosion treatment technology, comprises the steps:
[0027] C1 degreasing: put the oil tank to be degreased into the mixture prepared by weight parts of 4 parts of sodium carbonate, 2 parts of sodium bicarbonate, 2 parts of sodium silicate, 3 parts of sodium phosphate, 2 parts of surfactant and 100 parts of deionized water. Soak in the weak alkaline degreasing solution for 20 minutes. After degreasing is completed, rinse the surface of the fuel tank with clean water, drain the water stains, and dry at 60°C for 20 minutes until the fuel tank is completely dry;
[0028] C2 chemical polishing: cover the aluminum fuel tank with the end cap, immerse in the polishing solution for 5 minutes, then take out the fuel tank, drain the water stains after cleaning, and dry at 60°C for 20 minutes until the fuel tank is completely dry; the polishing solution is composed of 96 parts of phosphoric acid, sulfuric acid 56 parts, 15 ...
PUM
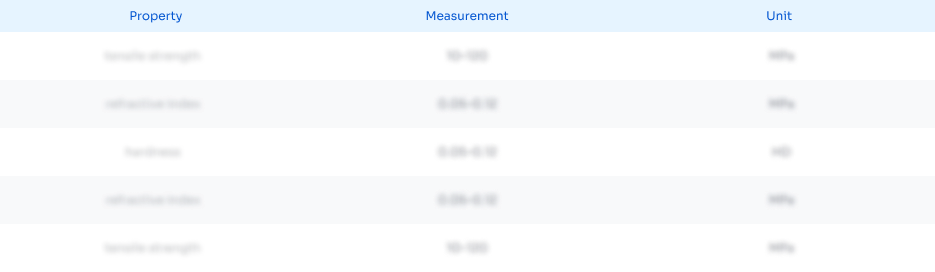
Abstract
Description
Claims
Application Information

- R&D Engineer
- R&D Manager
- IP Professional
- Industry Leading Data Capabilities
- Powerful AI technology
- Patent DNA Extraction
Browse by: Latest US Patents, China's latest patents, Technical Efficacy Thesaurus, Application Domain, Technology Topic, Popular Technical Reports.
© 2024 PatSnap. All rights reserved.Legal|Privacy policy|Modern Slavery Act Transparency Statement|Sitemap|About US| Contact US: help@patsnap.com