Machining method for hard alloy saw web
A technology of hard alloys and processing methods, which is applied in the direction of metal processing equipment, metal sawing equipment, and sawing machine tool manufacturing. Good quality, less welding times and less friction coefficient
- Summary
- Abstract
- Description
- Claims
- Application Information
AI Technical Summary
Problems solved by technology
Method used
Image
Examples
Embodiment 1
[0023] A method for processing cemented carbide saw blades, which includes the following steps: leveling the substrate of the cemented carbide saw blade → rolling teeth → welding the cutter head → sandblasting → grinding teeth → polishing → anti-rust treatment → storage of finished products; The step of welding the cutter head is interdental welding; the abrasive belt in the polishing step is 180 mesh, and the relative speed between the cemented carbide saw blade substrate and the abrasive belt is 4000r / min. The corundum in the blasting step is 40 mesh, and the blasting time is 10s. The antirust treatment steps include cleaning, oil immersion and drying of the carbide saw blade. The immersion oil used in the oil immersion step includes a varnish and a diluent in a mass ratio of 2:3. The varnish agent includes alkyd resin and butanol, and the mass ratio is 2:1. The diluent is xylene. The drying temperature is 80° C., and the drying time is 30 minutes.
Embodiment 2
[0025] A processing method of a cemented carbide saw blade, comprising the following steps: leveling of a cemented carbide saw blade substrate → tooth rolling → welding of a cutter head → sandblasting → secondary leveling of a cemented carbide saw blade substrate → tooth grinding → Polishing → antirust treatment → finished product storage; the step of welding the cutter head is interdental welding; the abrasive belt in the polishing step is 180 mesh, and the relative speed between the cemented carbide saw blade substrate and the abrasive belt is 4000r / min. The corundum in the blasting step is 40 mesh, and the blasting time is 10s. The antirust treatment steps include cleaning, oil immersion and drying of the carbide saw blade. The immersion oil used in the oil immersion step includes a varnish and a diluent in a mass ratio of 2:3. The varnish agent includes alkyd resin and butanol, and the mass ratio is 2:1. Described diluent is butyl acetate. The drying temperature is 80° ...
Embodiment 3
[0027] A processing method of a cemented carbide saw blade, comprising the following steps: leveling of a cemented carbide saw blade substrate → tooth rolling → welding of a cutter head → sandblasting → secondary leveling of a cemented carbide saw blade substrate → tooth grinding → Polishing → antirust treatment → finished product storage; the step of welding the cutter head is interdental welding; the abrasive belt in the polishing step is 240 mesh, and the relative speed between the cemented carbide saw blade substrate and the abrasive belt is 4500r / min. The corundum in the blasting step is 60 mesh, and the blasting time is 45s. The antirust treatment steps include cleaning, oil immersion and drying of the carbide saw blade. The immersion oil used in the oil immersion step includes a varnish and a diluent in a mass ratio of 2:3. The varnish agent includes alkyd resin and butanol, and the mass ratio is 2:1. The diluent is butyl acetate and butyl ether with a mass ratio of 1...
PUM
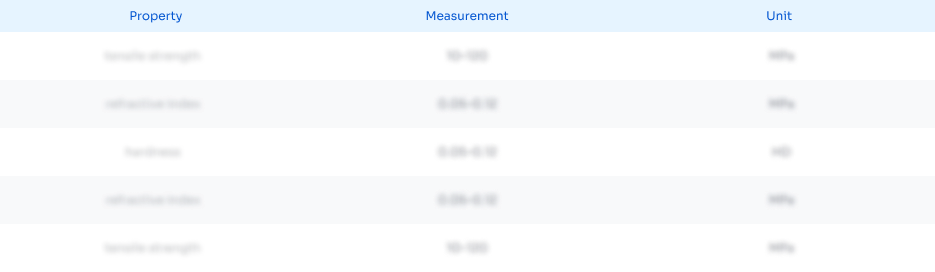
Abstract
Description
Claims
Application Information

- Generate Ideas
- Intellectual Property
- Life Sciences
- Materials
- Tech Scout
- Unparalleled Data Quality
- Higher Quality Content
- 60% Fewer Hallucinations
Browse by: Latest US Patents, China's latest patents, Technical Efficacy Thesaurus, Application Domain, Technology Topic, Popular Technical Reports.
© 2025 PatSnap. All rights reserved.Legal|Privacy policy|Modern Slavery Act Transparency Statement|Sitemap|About US| Contact US: help@patsnap.com