A kind of preparation method of membrane electrode of lithium ion battery
A lithium-ion battery, membrane electrode technology, applied in battery electrodes, electrode manufacturing, electrolyte storage battery manufacturing and other directions, can solve the problems of poor bonding force between electrode active materials and metal foils, restricted mechanical properties, shortened service life, etc. Effects of capacity and cycle performance, improved reliability and safety, and improved energy density
- Summary
- Abstract
- Description
- Claims
- Application Information
AI Technical Summary
Problems solved by technology
Method used
Examples
Embodiment 1
[0024] (1) Take 20ml of polymethyl methacrylate solution with a concentration of 20wt%, pour it into a polytetrafluoroethylene membrane maker with a diameter of 80°C, and obtain a lithium-ion membrane substrate with a thickness of 20um after drying at 80°C;
[0025] (2) Take the lithium ion negative electrode material lithium titanate and acetylene black and grind them evenly, place them in a vacuum drying oven at 80°C / 12h, and dry to obtain the negative electrode conductive drying material for use; take the lithium ion positive electrode material LiFePO 4 After being evenly ground with acetylene black, place it in a vacuum drying oven at 80°C / 12h, and dry to obtain the positive electrode conductive drying material for use;
[0026] (3) Take the polymethyl methacrylate solution and add it to N-methylpyrrolidone (NMP) as a dispersant, stir for 2 hours, then add the negative electrode conductive drying material obtained in step (2), stir for 3 hours, and coat it on the lithium O...
Embodiment 2
[0031] (1) Take 50ml of polyurethane solution with a concentration of 30wt%, pour it into a polytetrafluoroethylene membrane maker, and dry it at 150°C to obtain a lithium ion membrane substrate with a thickness of 50um;
[0032] (2) Take lithium ion negative electrode material graphite and XC72 carbon black and grind evenly, put it in a vacuum drying oven at 80°C / 12h, and dry to obtain negative electrode conductive drying material for use; take lithium ion positive electrode material LiFePO 4 After being evenly ground with XC72 carbon black, place it in a vacuum drying oven at 80°C / 12h, and dry to obtain a positive electrode conductive drying material for use;
[0033] (3) Take the polyurethane solution and add it to N-methylpyrrolidone (NMP) as a dispersant, stir for 4 hours, then add the negative electrode conductive drying material obtained in step (2), stir for 5 hours, and coat it on the lithium ion on the film substrate and dried;
[0034] (4) Take the polyurethane sol...
Embodiment 3
[0038] (1) Take 25ml of polyethylene naphthalate solution with a concentration of 25wt%, pour it into a polytetrafluoroethylene membrane maker, and dry it at 140°C to obtain a lithium ion membrane substrate with a thickness of 28um;
[0039] (2) Take the lithium ion negative electrode material lithium titanate and SP carbon black and grind them evenly, put them in a vacuum drying oven at 80°C / 12h, and dry to obtain the negative electrode conductive drying material for later use; take the lithium ion positive electrode material LiFeMnPO 4 After being evenly ground with SP carbon black, place it in a vacuum drying oven at 80°C / 12h, and dry to obtain a positive electrode conductive drying material for use;
[0040] (3) Add polyethylene naphthalate solution into N-methylpyrrolidone (NMP) as a dispersant, stir magnetically for 3 hours, then add the negative electrode conductive drying material obtained in step (2), stir for 4 hours, coat Cover one side of the lithium ion membrane s...
PUM
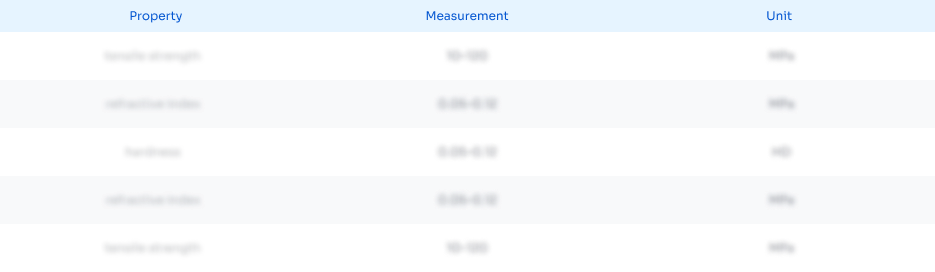
Abstract
Description
Claims
Application Information

- R&D
- Intellectual Property
- Life Sciences
- Materials
- Tech Scout
- Unparalleled Data Quality
- Higher Quality Content
- 60% Fewer Hallucinations
Browse by: Latest US Patents, China's latest patents, Technical Efficacy Thesaurus, Application Domain, Technology Topic, Popular Technical Reports.
© 2025 PatSnap. All rights reserved.Legal|Privacy policy|Modern Slavery Act Transparency Statement|Sitemap|About US| Contact US: help@patsnap.com