Preparation method of oiling agent for polyester spinning
A spinning and finishing technology is applied in the field of preparation of finishing finishing for polyester spinning, which can solve the problems of poor wetting and permeability, low production cost and the like, and achieves the advantages of environmental protection, low production cost and low surface tension. Effect
- Summary
- Abstract
- Description
- Claims
- Application Information
AI Technical Summary
Problems solved by technology
Method used
Image
Examples
Embodiment 1
[0025] A preparation method for polyester spinning oil, comprising the following steps:
[0026] (1) Make 5mol diamine hydrogen phosphate and 5mol calcium nitrate into an aqueous solution with a concentration of 0.2-0.5mol / L, then transfer to the reaction kettle, add ammonia water dropwise, adjust the pH of the solution to 11-12, and then add 1.65mol-2.5 mol cellulose nanocrystals, 1.65mol-2.5mol polylactic acid, stir until mixed evenly, add 2.5mol-7.5mol polyglycolic acid, heat up to 80°C, react for 1h, cool to room temperature, and obtain mixed emulsion A;
[0027] (2) 1.65mol-2.5mol polyoxyethylene coconut oleate, 1.65mol-2.5mol sorbitan stearate, 5mol-12molC 5-10 Saturated fatty alcohol oxyethylene ether and 5mol-10mol tung oil are added to the reaction kettle, the temperature is raised to 50°C, reacted for 2h, cooled to room temperature, and mixed emulsion B is obtained;
[0028] (3) The mixed emulsion A obtained in step (1) and the mixed emulsion B obtained in step (2) ...
Embodiment 2
[0030] A preparation method for polyester spinning oil, comprising the following steps:
[0031] (1) Make 5mol diamine hydrogen phosphate and 5mol calcium nitrate into an aqueous solution with a concentration of 0.2-0.5mol / L, then transfer to the reaction kettle, add ammonia water dropwise, adjust the pH of the solution to 11-12, and then add 1.65mol-2.5 mol cellulose nanocrystals, 1.65mol-2.5mol polylactic acid, stir until mixed evenly, add 2.5mol-7.5mol polyglycolic acid, heat up to 100°C, react for 3 hours, cool to room temperature, and obtain mixed emulsion A;
[0032] (2) 1.65mol-2.5mol polyoxyethylene coconut oleate, 1.65mol-2.5mol sorbitan stearate, 5mol-12molC 5-10 Saturated fatty alcohol oxyethylene ether and 5mol-10mol tung oil are added to the reaction kettle, the temperature is raised to 60°C, reacted for 4h, cooled to room temperature, and mixed emulsion B is obtained;
[0033] (3) Mix and stir the mixed emulsion A obtained in step (1) and the mixed emulsion B ob...
Embodiment 3
[0035] A preparation method for polyester spinning oil, comprising the following steps:
[0036] (1) Make 5mol diamine hydrogen phosphate and 5mol calcium nitrate into an aqueous solution with a concentration of 0.2-0.5mol / L, then transfer to the reaction kettle, add ammonia water dropwise, adjust the pH of the solution to 11-12, and then add 1.65mol-2.5 mol cellulose nanocrystals, 1.65mol-2.5mol polylactic acid, stir until mixed evenly, add 2.5mol-7.5mol polyglycolic acid, heat up to 85°C, react for 1.5h, cool to room temperature, and obtain mixed emulsion A;
[0037] (2) 1.65mol-2.5mol polyoxyethylene coconut oleate, 1.65mol-2.5mol sorbitan stearate, 5mol-12molC 5-10 Saturated fatty alcohol oxyethylene ether and 5mol-10mol tung oil were added to the reaction kettle, heated to 55°C, reacted for 2.5h, cooled to room temperature, and mixed emulsion B was obtained;
[0038] (3) The mixed emulsion A obtained in step (1) and the mixed emulsion B obtained in step (2) were mixed an...
PUM
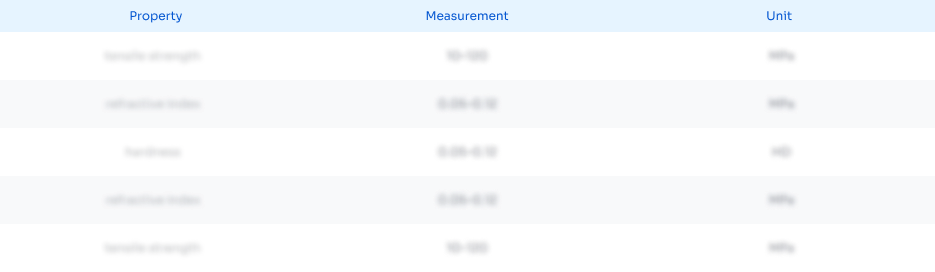
Abstract
Description
Claims
Application Information

- R&D Engineer
- R&D Manager
- IP Professional
- Industry Leading Data Capabilities
- Powerful AI technology
- Patent DNA Extraction
Browse by: Latest US Patents, China's latest patents, Technical Efficacy Thesaurus, Application Domain, Technology Topic, Popular Technical Reports.
© 2024 PatSnap. All rights reserved.Legal|Privacy policy|Modern Slavery Act Transparency Statement|Sitemap|About US| Contact US: help@patsnap.com