Method for preparing high-purity MnBi alloy
A high-purity, alloy technology, applied in the field of manganese-bismuth (MnBi) alloy preparation, can solve the problems of difficult synthesis of MnBi alloy materials, restrictions on the application of MnBi alloy materials, low magnetic properties of alloy materials, etc., to achieve improved purity, high melting point, The effect of high thermal conductivity
- Summary
- Abstract
- Description
- Claims
- Application Information
AI Technical Summary
Problems solved by technology
Method used
Image
Examples
preparation example Construction
[0019] The preparation method of high-purity MnBi alloy comprises the following steps:
[0020] ①. Select Bi and Mn powders as raw materials, and the Bi and Mn are 99%-99.999% nano- or micron-sized powders.
[0021] ②. Proportion the Bi and Mn powders selected in the above ① according to the molar ratio 1:x (x=1.0-2.0), mix them uniformly and package them in molybdenum cups, and carry out low-pressure pretreatment on the molybdenum cup samples through a powder molding press. Treatment or ultra-high pressure pretreatment of molybdenum cup samples by domestic six-sided top hydraulic press, the pressure range of low pressure pretreatment is 2-40MPa, and the pressure range of high pressure pretreatment is 1-6GPa.
[0022] ③. Put the molybdenum cup cavity pre-pressed in ② into the crucible, complete the preparation of MnBi alloy through closed low-temperature sintering and quenching procedures, and prepare high-purity MnBi alloy (95at.%). Closed low-temperature sintering is to syn...
Embodiment 1
[0024] as attached figure 1 Shown: Select 3.0g of Bi and Mn mixed powder (average particle size 3-5μm, molar ratio 1:1) as raw material, such as figure 1 Shown in number 1. Put the mixed powder into the molybdenum cup cavity of outer cup Φ13.65×5mm and inner cup Φ13.38×5mm, such as figure 1 Shown in number 2. The low-pressure pre-compression sealing treatment was carried out on the powder molding press, and the pressure condition was 2 MPa to obtain a dense Bi-Mn sample block sealed by a Φ14×3.2 mm molybdenum cup.
[0025] as attached image 3 Shown: Put the sealed molybdenum cup sample block into a ceramic crucible with a volume of about 40ml, such as image 3 Shown in number 7. Place the molybdenum cup closed cavity (after pre-pressing) 8 and the large-aperture metal mesh 9 from top to bottom, and perform low-temperature heat treatment in the muffle furnace. The sintering temperature is 270°C, the holding time is 50h, and quenching Finally, a Φ13.5×3mm high-purity MnBi...
Embodiment 2
[0027] as attached figure 1 Shown: Select 3.0g of Bi and Mn mixed powder (average particle size 3-5μm, molar ratio 1:1.3) as raw material, such as figure 1 Shown in number 1. Put the mixed powder into the molybdenum cup cavity of outer cup Φ13.65×5mm and inner cup Φ13.38×5mm, such as figure 1 Shown in number 2. The low-pressure pre-compression sealing treatment was carried out on the powder molding press, and the pressure condition was 15MPa to obtain a dense Bi-Mn sample block sealed by a Φ14×3.2mm molybdenum cup.
[0028] as attached image 3 Shown: Put the sealed molybdenum cup sample block into a ceramic crucible with a volume of about 40ml, such as image 3 Shown in number 7. Place the molybdenum cup closed cavity (after pre-pressing) 8 and the large-aperture metal mesh 9 from top to bottom, and perform low-temperature heat treatment in the muffle furnace. The sintering temperature is 280°C, the holding time is 20h, and quenching Finally, a Φ13.5×3mm high-purity MnB...
PUM
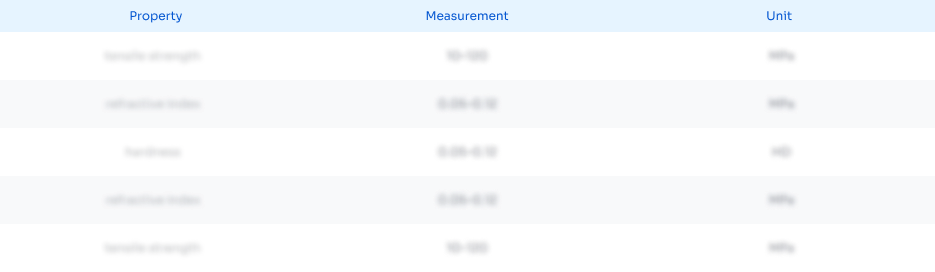
Abstract
Description
Claims
Application Information

- R&D Engineer
- R&D Manager
- IP Professional
- Industry Leading Data Capabilities
- Powerful AI technology
- Patent DNA Extraction
Browse by: Latest US Patents, China's latest patents, Technical Efficacy Thesaurus, Application Domain, Technology Topic, Popular Technical Reports.
© 2024 PatSnap. All rights reserved.Legal|Privacy policy|Modern Slavery Act Transparency Statement|Sitemap|About US| Contact US: help@patsnap.com