Coal-fired power generation system deeply integrated with calcium-based absorbent sequential desulfurization and decarbonization system
A calcium-based absorbent and power generation system technology, which is applied in steam generation, machines/engines, and energy industries, can solve the problems of high energy consumption for compression, high energy consumption for air separation, and high energy consumption for calcination, so as to reduce energy consumption, Effect of improving thermal efficiency and reducing oxygen consumption
- Summary
- Abstract
- Description
- Claims
- Application Information
AI Technical Summary
Problems solved by technology
Method used
Image
Examples
Embodiment Construction
[0028] The present invention will be further described below in conjunction with the accompanying drawings and specific embodiments. It should be emphasized that the following description is only exemplary and not intended to limit the scope of the invention and its application.
[0029] Such as figure 1 As shown in the flow chart of the benchmark system, the flue gas of the power plant passes through the water wall 2, the partition superheater 3, the rear panel superheater 4, the high temperature reheater 5, the final superheater 6, the low temperature reheater 7, and the economizer 8 1. The air preheater 9 enters the carbonization furnace 10 for desulfurization and decarbonization after heat exchange. The operating temperature of the carbonization furnace 10 is 650°C. The exported logistics is divided into two streams, and the CO-depleted stream after desulfurization and decarbonization 2 The flue gas is discharged into the atmosphere after being recovered by the waste hea...
PUM
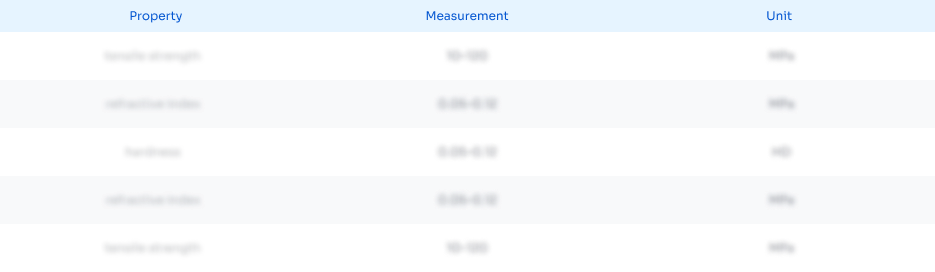
Abstract
Description
Claims
Application Information

- R&D
- Intellectual Property
- Life Sciences
- Materials
- Tech Scout
- Unparalleled Data Quality
- Higher Quality Content
- 60% Fewer Hallucinations
Browse by: Latest US Patents, China's latest patents, Technical Efficacy Thesaurus, Application Domain, Technology Topic, Popular Technical Reports.
© 2025 PatSnap. All rights reserved.Legal|Privacy policy|Modern Slavery Act Transparency Statement|Sitemap|About US| Contact US: help@patsnap.com