Organic-inorganic hybrid 3D printing material and preparation method thereof
A 3D printing, inorganic technology, applied in the field of organic-inorganic hybrid 3D printing materials and their preparation, can solve problems such as low flexibility and mechanical properties, inability to use organ transplantation, lack of versatility, etc., and achieve excellent mechanical properties. and flexibility, low production cost, excellent mechanical properties
- Summary
- Abstract
- Description
- Claims
- Application Information
AI Technical Summary
Problems solved by technology
Method used
Examples
Embodiment 1
[0033] An organic-inorganic hybrid 3D printing material is prepared according to the following steps:
[0034] 1. Mix sodium montmorillonite and hexadecyltrimethylammonium bromide (the amount of quaternary ammonium salt accounts for 5% of the mass of montmorillonite) in water and stir for 1 hour at 60°C, then filter, wash and fully dry Obtain quaternary ammonium salt intercalation modified montmorillonite powder;
[0035] 2. Prepare montmorillonite / polyacrylate by solution radical polymerization of the following components:
[0036] 40 parts of methyl methacrylate,
[0037] 10 parts of butyl acrylate,
[0038] 5 parts of methacrylic acid,
[0039] 10 parts of quaternary ammonium salt intercalation modified montmorillonite powder,
[0040] 0.2 parts of azobisisobutyronitrile;
[0041] First, 4 / 5 of butyl acetate (the amount of which makes the total mass fraction of mixed monomers is 15%), methyl methacrylate, butyl acrylate, methacrylic acid and quaternary ammonium salt in...
Embodiment 2
[0043] An organic-inorganic hybrid 3D printing material is prepared according to the following steps:
[0044] 1. Stir and react calcium-based montmorillonite and cetyltrimethylammonium chloride (quaternary ammonium salt accounts for 15% of the mass of montmorillonite) in water for 3 hours at 90°C, then filter, wash and fully dry Obtain quaternary ammonium salt intercalation modified montmorillonite powder;
[0045] 2. The following components are prepared in parts by weight by solution radical polymerization to obtain montmorillonite / polyacrylate:
[0046] 40 parts of methyl methacrylate,
[0047] 40 parts of styrene,
[0048] 10 parts of butyl acrylate,
[0049] 15 parts of ethyl acrylate,
[0050] 5 parts of methacrylic acid,
[0051] Acrylic acid 5 parts,
[0052] 20 parts of quaternary ammonium salt intercalation modified montmorillonite powder,
[0053] 1.5 parts of azobisisoheptanonitrile;
[0054] First, 7 / 8 mixed solvent (butyl acetate and methyl ethyl ketone ar...
Embodiment 3
[0056] An organic-inorganic hybrid 3D printing material is prepared according to the following steps:
[0057] 1. Stir and react sodium montmorillonite and octadecyltrimethylammonium bromide (the amount of quaternary ammonium salt accounts for 10% of the mass of montmorillonite) in water for 2 hours at 80°C, then filter, wash and fully dry Obtain quaternary ammonium salt intercalation modified montmorillonite powder;
[0058] 2. Prepare montmorillonite / polyacrylate by solution radical polymerization with the following components in parts by weight:
[0059] 20 parts of methyl methacrylate,
[0060] 20 parts of styrene,
[0061] 20 parts of methyl acrylate,
[0062] 5 parts of butyl acrylate,
[0063] 5 parts of butyl methacrylate,
[0064] 10 parts of ethyl acrylate,
[0065] 4 parts methacrylic acid,
[0066] 4 parts acrylic,
[0067] 15 parts of quaternary ammonium salt intercalation modified montmorillonite powder,
[0068] 0.5 parts of dimethyl azobisisobutyrate; ...
PUM
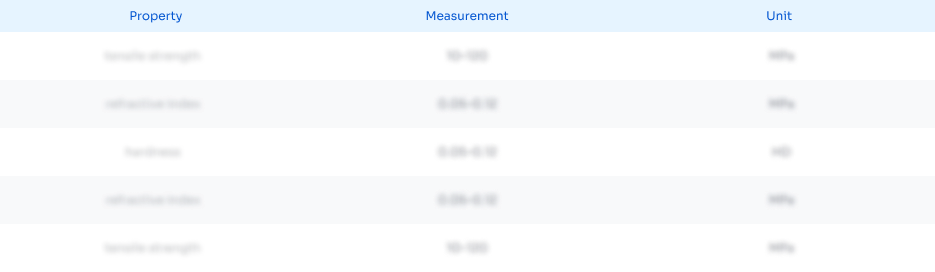
Abstract
Description
Claims
Application Information

- R&D
- Intellectual Property
- Life Sciences
- Materials
- Tech Scout
- Unparalleled Data Quality
- Higher Quality Content
- 60% Fewer Hallucinations
Browse by: Latest US Patents, China's latest patents, Technical Efficacy Thesaurus, Application Domain, Technology Topic, Popular Technical Reports.
© 2025 PatSnap. All rights reserved.Legal|Privacy policy|Modern Slavery Act Transparency Statement|Sitemap|About US| Contact US: help@patsnap.com