Composite ceramic coating, lithium ion battery composite ceramic diaphragm and lithium ion battery
A technology of lithium-ion batteries and composite ceramics, which is applied in the field of composite ceramic coatings and lithium-ion battery composite ceramic diaphragms, can solve the problems of reducing battery energy density, increasing battery manufacturing costs, overcharging and overdischarging, and improving battery overcharging , Improve the safety performance of abuse and prevent overcharging
- Summary
- Abstract
- Description
- Claims
- Application Information
AI Technical Summary
Problems solved by technology
Method used
Image
Examples
Embodiment 1
[0033] Preparation of positive electrode sheet: Mix nickel-cobalt lithium manganese oxide, conductive carbon, and binder (polyvinylidene fluoride) in N-methylpyrrolidone solvent at a mass ratio of 97:1.5:1.5 to make a positive electrode slurry, and then coat Clothed on aluminum foil and dried, then cold-pressed and slitting to make positive pole pieces.
[0034] Preparation of negative electrode sheet: Mix graphite, conductive carbon, dispersant (sodium carboxymethyl cellulose), and binder (styrene-butadiene rubber) in deionized water at a mass ratio of 95:1.5:2.0:1.5 to make negative electrode slurry Material, then coated on copper foil and dried, then cold pressed and slitting to make negative electrode sheet.
[0035] Preparation of ceramic diaphragm: Mix aluminum oxide, lithium carbonate, and sodium carboxymethyl cellulose in a mass ratio of 0.48:0.5:0.02, use deionized water as the dispersion medium, and prepare a slurry with a certain viscosity after high-speed stirring ...
Embodiment 2
[0039] The difference from Example 1 is that the preparation of the ceramic diaphragm: mix titanium dioxide, lithium bicarbonate, and sodium carboxyethyl cellulose in a mass ratio of 0.68:0.3:0.05, use deionized water as the dispersion medium, and stir at a high speed A slurry with a certain viscosity is prepared to obtain a composite ceramic coating, and the composite ceramic coating is coated on both sides of a PP base film with a thickness of 8um. The thickness of the composite ceramic coating is controlled at 4um, and then baked and cut into pieces. Ceramic separator for batteries.
[0040] The rest are the same as in Embodiment 1, and will not be repeated.
Embodiment 3
[0042]Different from Example 1, the preparation of the ceramic diaphragm: mix silicon dioxide, lithium carbonate, lithium bicarbonate, sodium carboxyethyl cellulose in a mass ratio of 0.28:0.35:0.35:0.1, and deionized water As a dispersion medium, a slurry with a certain viscosity is prepared by high-speed stirring to obtain a composite ceramic coating, and the composite ceramic coating is coated on one side of a PP / PP base film with a thickness of 10um, and the thickness of the composite ceramic coating is controlled at 8um. Then it is baked and cut into ceramic separators for batteries.
[0043] The rest are the same as in Embodiment 1, and will not be repeated.
PUM
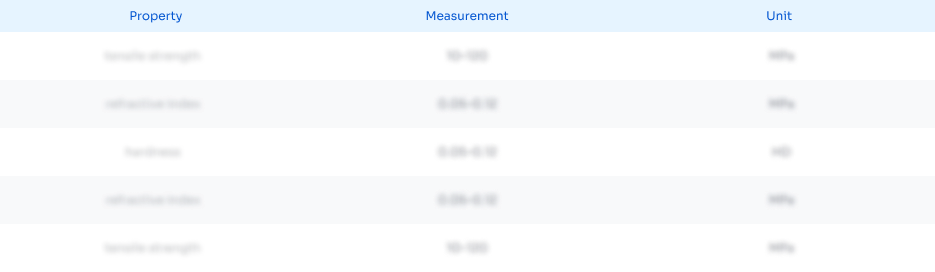
Abstract
Description
Claims
Application Information

- R&D Engineer
- R&D Manager
- IP Professional
- Industry Leading Data Capabilities
- Powerful AI technology
- Patent DNA Extraction
Browse by: Latest US Patents, China's latest patents, Technical Efficacy Thesaurus, Application Domain, Technology Topic, Popular Technical Reports.
© 2024 PatSnap. All rights reserved.Legal|Privacy policy|Modern Slavery Act Transparency Statement|Sitemap|About US| Contact US: help@patsnap.com