Circulating heat exchange agent for reactor
A technology of cyclic heat exchange and reactor, which is applied in heat exchange materials, chemical instruments and methods, hydrogen halide addition preparation, etc. It can solve the problems of loss of active components in catalysts, increase of system risk, and reduction of production efficiency. , to achieve the effect of stable control of the reaction process, ensuring effective working time, and solving safety problems
- Summary
- Abstract
- Description
- Claims
- Application Information
AI Technical Summary
Problems solved by technology
Method used
Examples
Embodiment 1
[0012] The final system achieves the following control indicators:
[0013] The content of trichloroethane is 100 parts
[0014] 0.2 part of stabilizer (hydroquinone), cresol or stearyl triethanolamine salt
[0015] Circulating agent temperature 80-140℃
[0016] The heat exchange agent does not cause any corrosion to the reactor, and the temperature of the circulating agent is controlled between 80 and 140°C. It is suitable for operation in the reactor for the synthesis of vinyl chloride by the traditional calcium carbide method with mercuric chloride catalyst. The reaction temperature of the converter is easy to control, and the reaction The process is quite stable, prolonging the service life of the reactor and the catalyst, improving the production efficiency of the reactor and the catalyst, and reducing the production cost.
Embodiment 2
[0018] The final system achieves the following control indicators:
[0019] The content of tetrachlorethylene is 100 parts
[0020] 0.4 part of stabilizer (hydroquinone), cresol or stearyl triethanolamine salt
[0021] Circulating agent temperature 80-140℃
[0022] The heat exchange agent does not cause any corrosion to the reactor, and the temperature of the circulating agent is controlled between 80 and 140°C. It is suitable for operation in the reactor for the synthesis of vinyl chloride by the traditional calcium carbide method with mercuric chloride catalyst. The reaction temperature of the converter is easy to control, and the reaction The process is quite stable, prolonging the service life of the reactor and the catalyst, improving the production efficiency of the reactor and the catalyst, and reducing the production cost.
Embodiment 3
[0024] The final system achieves the following control indicators:
[0025] Tetrachloroethane content is 100 parts
[0026] 0.2 part of stabilizer (hydroquinone), cresol or stearyl triethanolamine salt
[0027] Circulating agent temperature 80-160℃
[0028] The heat exchange agent has no corrosion to the reactor, and the temperature of the circulating agent is controlled between 80 and 160° C., which is suitable for operation in a reactor for the novel synthesis of vinyl chloride using a novel non-mercury catalyst. The reaction temperature of the converter is easy to control, the reaction process is quite stable, the service life of the reactor and the catalyst is prolonged, the production efficiency of the reactor and the catalyst is improved, and the production cost is reduced.
PUM
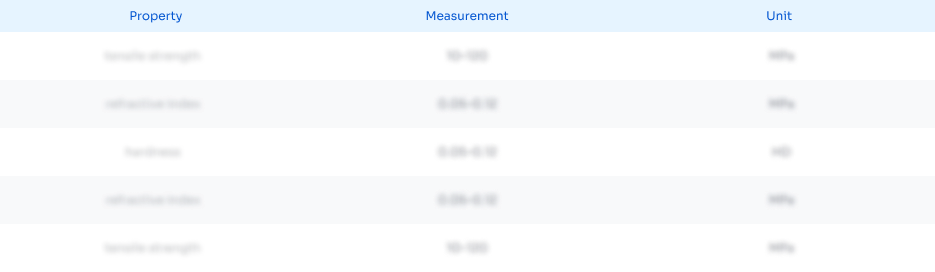
Abstract
Description
Claims
Application Information

- R&D Engineer
- R&D Manager
- IP Professional
- Industry Leading Data Capabilities
- Powerful AI technology
- Patent DNA Extraction
Browse by: Latest US Patents, China's latest patents, Technical Efficacy Thesaurus, Application Domain, Technology Topic, Popular Technical Reports.
© 2024 PatSnap. All rights reserved.Legal|Privacy policy|Modern Slavery Act Transparency Statement|Sitemap|About US| Contact US: help@patsnap.com