Heat-insulation reaction system and process for preparing glycolate through oxalate hydrogenation
An adiabatic reaction, glycolic acid ester technology, applied in the preparation of carboxylate, the preparation of organic compounds, organic chemistry and other directions, can solve the problems of inappropriate proportion of hot materials, insufficient utilization of catalysts, uneven mixing and air flow, etc. Achieve the effect of improving conversion rate, inhibiting side reactions and reducing energy consumption
- Summary
- Abstract
- Description
- Claims
- Application Information
AI Technical Summary
Problems solved by technology
Method used
Image
Examples
Embodiment 1
[0028] The process of using a single-layer axial adiabatic fixed-bed reactor figure 1 Shown. The hydrogenation reactor is a cylindrical body with an inner diameter of 160 mm and a height of 600 mm. Load 4LAg / SiO in the middle of the hydrogenation reactor 2 The catalyst is filled with stainless steel magnetic rings with the same particle size at the top and bottom, diethyl oxalate is used as the raw material, the reaction pressure is set to 3.0Mpa, and the molar ratio of hydrogen to oxalate in the hydrogenation reactor inlet is 120.
[0029] Hydrogen mixed gas 1 (hydrogen: 95v%, ethanol: 4v%, the rest is inert gas), flow rate 30Nm3 / h, temperature 84°C, pressure 3.12MPa(A), preheated to 152°C by circulating gas preheater E1 The hot stream 2 enters the vaporization tower T1, and is mixed with the raw material oxalate liquid 8 at a temperature of 160°C, and the liquid raw material feed rate is 1.55 kg / h to vaporize the liquid oxalate. The vaporized oxalate ester steam and hydrogen m...
Embodiment 2
[0031] The process of using a single-layer axial adiabatic fixed-bed reactor figure 1 Shown. The reactor is a cylindrical body with an inner diameter of 160 mm and a height of 600 mm. The 4LAg / SiO2 catalyst is filled in the middle of the hydrogenation reactor, and the upper and lower parts are filled with stainless steel magnetic rings with the same particle size. Diethyl oxalate is used as the raw material. The reaction pressure is set to 3.0MPa. The hydrogen and oxalate are in the inlet of the reactor. The molar ratio is 80.
[0032] Hydrogen mixed gas 1 (hydrogen: 95v%, ethanol: 4v%, the rest is inert gas), flow rate 20Nm3 / h, temperature 84°C, pressure 3.12MPa(A), preheated to 168°C by circulating gas preheater E1 The hot stream 2 enters the vaporization tower T1, and is mixed with the raw material oxalate liquid 8 at a temperature of 160°C. The liquid raw material feed rate is 1.55 kg / h to vaporize the liquid oxalate. The vaporized steam and hydrogen mixed gas 1 form a mixt...
Embodiment 3
[0034] The process of using a single-layer radial adiabatic fixed-bed reactor is as follows: figure 1 As shown, see the reactor type image 3 . The reactor is a cylindrical body with an inner diameter of 200mm and a height of 600mm. The catalyst is packed in an annulus formed by concentric circles. The gas is blown out by the distributor and passes through the catalyst bed in the radial direction. The 4LAg / SiO2 catalyst is loaded in the middle of the hydrogenation reactor, and the upper and lower parts are filled with stainless steel magnetic rings of equivalent particle size. Diethyl oxalate is used as the raw material. The reaction pressure is set to 3.0Mpa. The molar ratio of the acid ester is 100. The specific reaction process is the same as in Example 1.
[0035] The composition and mass fraction of the product are: ethanol 32.3%, ethyl acetate 1.00%, water 0.55%, ethylene glycol monoethyl ether 0.18%, ethyl glycolate 65.3%, ethylene glycol 0.54%, and others 0.13%. The co...
PUM
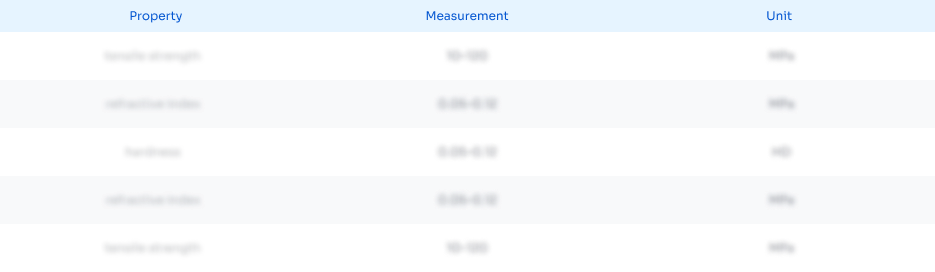
Abstract
Description
Claims
Application Information

- Generate Ideas
- Intellectual Property
- Life Sciences
- Materials
- Tech Scout
- Unparalleled Data Quality
- Higher Quality Content
- 60% Fewer Hallucinations
Browse by: Latest US Patents, China's latest patents, Technical Efficacy Thesaurus, Application Domain, Technology Topic, Popular Technical Reports.
© 2025 PatSnap. All rights reserved.Legal|Privacy policy|Modern Slavery Act Transparency Statement|Sitemap|About US| Contact US: help@patsnap.com