Organic silicone modified acrylate emulsion and preparation method thereof
A technology of acrylate and silicone, which is applied in the field of silicone-modified acrylate emulsion and its preparation, and can solve problems such as poor environmental protection, weather resistance, emulsion stability, coating film mechanical strength, solvent resistance and unsatisfactory functionality. , to achieve the effect of improving stability and water resistance and reducing VOC emissions
- Summary
- Abstract
- Description
- Claims
- Application Information
AI Technical Summary
Problems solved by technology
Method used
Examples
Embodiment 1
[0026] Example 1 is composed of the following substances in parts by weight: 5 methyl acrylate, 8 butyl acrylate, 0.5 glycidyl acrylate, 10 octamethylcyclotetrasiloxane (D4), 5.0 sodium alkyl vinyl sulfonate , potassium persulfate 0.5, deionized water 71
[0027] Firstly, potassium persulfate is added to the catalyst tank equipped with deionized water, and stirred evenly to obtain the initiator solution A with a concentration of 2.5%; methyl acrylate, butyl acrylate, glycidyl acrylate, octamethylcyclotetrasiloxane Mix alkanes (D4) in the premixing tank evenly to obtain the mixed phase B of polymerized monomers; add sodium alkyl vinyl sulfonate and deionized water into the four-necked flask, maintain the rotation speed at 200r / min, and heat to 80°C , slowly drop the homogeneously mixed monomer mixed phase B and 90% initiator solution A for 2 hours, and keep the polymerization temperature at 80°C during the reaction process; Add the remaining 10% initiator solution A dropwise; ...
Embodiment 2
[0028] Example 2 is composed of the following substances in parts by weight: methyl methacrylate 15, octyl acrylate 12, glycidyl methacrylate 0.5, hexamethylcyclotrisiloxane (D3) 5.0, dodecyl Sodium allyl succinate 2.0, ammonium persulfate 0.5, deionized water 65
[0029] First, ammonium persulfate is added to the catalyst tank equipped with deionized water, and stirred evenly to obtain a solution A with a concentration of 2.5%; methyl methacrylate, octyl acrylate, glycidyl methacrylate, hexamethyl Mix cyclotrisiloxane (D3) evenly in the premixing tank to obtain the mixed phase B of polymerized monomers; add sodium dodecyl allyl succinate and deionized water into the four-necked flask, and maintain the rotation speed at 250r / min, after heating to 70°C, slowly add the uniformly mixed monomer mixed phase B and 90% initiator solution A for 3 hours, and keep the polymerization temperature at 70°C during the reaction process; after the dropwise addition, the temperature rises to 9...
Embodiment 3
[0030] Example 3 is composed of the following substances in parts by weight: methacrylic acid 11, ethyl acrylate 15, glycidyl methacrylate 0.5, decamethylcyclopentasiloxane (D5) 6, sodium vinyl sulfonate 3 , ammonium persulfate 0.5, deionized water 64
[0031] Firstly, ammonium persulfate is added to the catalyst tank equipped with deionized water, and stirred evenly to obtain the initiator solution A with a concentration of 2.5%; methacrylic acid, ethyl acrylate, glycidyl methacrylate, decamethylcyclopentadiene Mix the siloxane (D5) evenly in the pre-mixing tank to obtain the mixed phase B of polymerized monomers; add sodium vinyl sulfonate and deionized water into the four-necked flask, maintain the rotation speed at 300r / min, and heat it to 90°C , slowly drop the uniformly mixed monomer mixed phase B and 90% initiator solution A for 1 hour, and keep the polymerization temperature at 90°C during the reaction process; Add the remaining 10% initiator solution A dropwise; when...
PUM
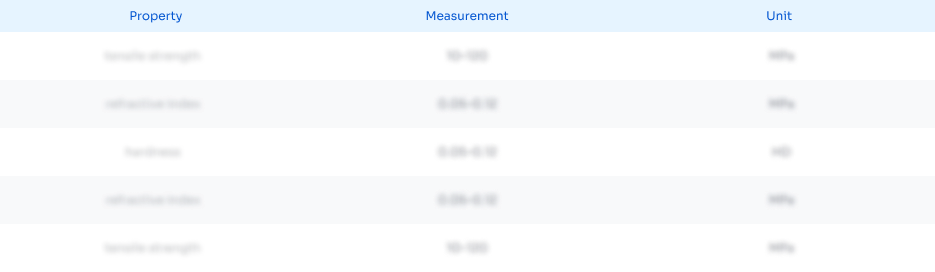
Abstract
Description
Claims
Application Information

- Generate Ideas
- Intellectual Property
- Life Sciences
- Materials
- Tech Scout
- Unparalleled Data Quality
- Higher Quality Content
- 60% Fewer Hallucinations
Browse by: Latest US Patents, China's latest patents, Technical Efficacy Thesaurus, Application Domain, Technology Topic, Popular Technical Reports.
© 2025 PatSnap. All rights reserved.Legal|Privacy policy|Modern Slavery Act Transparency Statement|Sitemap|About US| Contact US: help@patsnap.com