Preparation method and application of silicon oxycarbide/carbon composite micronano material
A silicon oxycarbide, micro-nano technology, applied in nanotechnology, nanotechnology, nanotechnology for materials and surface science, etc., can solve the problems of optimization, unfavorable structural properties, microstructure and limited carbon content capacity, etc. The effect of good lithium battery performance, short time and easy operation
- Summary
- Abstract
- Description
- Claims
- Application Information
AI Technical Summary
Problems solved by technology
Method used
Image
Examples
Embodiment 1
[0022] Step (1). Add 2g photoinitiator phenyl bis(2,4,6-trimethylbenzoyl) phosphine oxide into 998g bisphenol A glycerol dimethacrylate solution and stir for 5 minutes at room temperature Obtain 1kg resin solution after;
[0023] Step (2). Take 200g of step (1) resin solution, add 12.5g of silane coupling agent hexadecyltrimethoxysilane and 12.5g of acrylic acid, and stir to obtain a mixed solution;
[0024] Step (3). Import the mixed solution obtained in step (2) into the silica gel template placed on the glass slide, and then cover a glass slide on top, cure for 2 minutes on the upper and lower sides, and then incubate at 30°C for 24 hours or more fully cured;
[0025] Step (4). The solid obtained in step (3) was placed in a corundum crucible, placed in a tube furnace, and calcined at 600° C. for 8 hours under an inert atmosphere to obtain a silicon oxycarbide / carbon composite powder.
[0026] In the silicon oxycarbide / carbon composite powder prepared in this example, the ...
Embodiment 2
[0028] Step (1). Add 20g of photoinitiator Yanjiagu 1173 into 980g of bisphenol A glycidyl methacrylate solution, and stir at room temperature for 5 minutes to obtain 1kg of resin solution;
[0029] Step (2). Take 200g of the resin solution in step (1), add 200g of silane coupling agent γ-(methacryloyloxy)propyltriethoxysilane, and 50g of methacrylic acid, and stir to obtain a mixed solution;
[0030] Step (3). Import the mixed solution obtained in step (2) into the silica gel template placed on the glass slide, and then cover a glass slide on the top, cure for 3 minutes on the upper and lower sides, and then incubate at 80°C for 6 hours or more fully cured;
[0031] Step (4). Put the solid obtained in step (3) in a corundum crucible, put it in a tube furnace, and calcinate at 1200° C. for 1 hour under an inert atmosphere to obtain a silicon oxycarbide / carbon composite powder.
Embodiment 3
[0033] Step (1). Add 5g of photoinitiator Yanjiagu 184 into 995g of urethane dimethacrylate solution, and stir at room temperature for 5 minutes to obtain 1kg of resin solution;
[0034] Step (2). Take 200g of step (1) resin solution, add 15g of silane coupling agent n-octyltrimethoxysilane and 2400g of acrylic acid, and stir to obtain a mixed solution;
[0035] Step (3). Import the mixed solution obtained in step (2) into the silica gel template placed on the glass slide, and then cover a glass slide on the top, cure for 2.5 minutes on the upper and lower sides, and then incubate at 40°C for 22 hours or more fully cured;
[0036] Step (4). The solid obtained in step (3) was placed in a corundum crucible, placed in a tube furnace, and calcined at 700° C. for 7.5 hours under an inert atmosphere to obtain a silicon oxycarbide / carbon composite powder. The XRD data prove that silicon oxycarbide particles are in an amorphous state and exist in a carbon matrix with a microcrystalli...
PUM
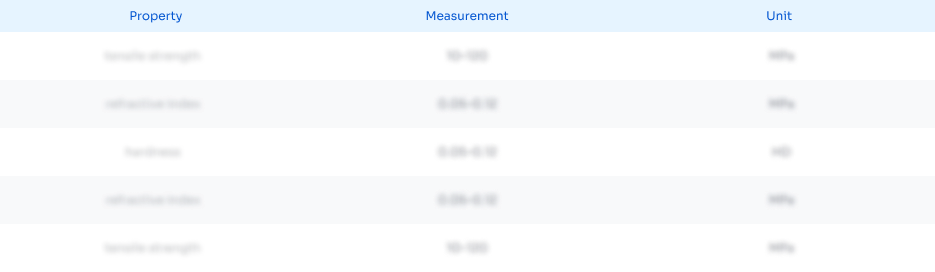
Abstract
Description
Claims
Application Information

- Generate Ideas
- Intellectual Property
- Life Sciences
- Materials
- Tech Scout
- Unparalleled Data Quality
- Higher Quality Content
- 60% Fewer Hallucinations
Browse by: Latest US Patents, China's latest patents, Technical Efficacy Thesaurus, Application Domain, Technology Topic, Popular Technical Reports.
© 2025 PatSnap. All rights reserved.Legal|Privacy policy|Modern Slavery Act Transparency Statement|Sitemap|About US| Contact US: help@patsnap.com