Preparation method of vanadium pentoxide adsorbent
A vanadium pentoxide and adsorbent technology, which is applied in the field of anion exchange resin preparation, can solve the problems of affecting the use effect of industrial devices, affecting the uniformity of polymerization, and reducing the strength of resin, so as to achieve enhanced binding force, prolong service life, and improve efficiency effect
- Summary
- Abstract
- Description
- Claims
- Application Information
AI Technical Summary
Problems solved by technology
Method used
Image
Examples
Embodiment 1
[0029] Step 1. Preparation of the water phase
[0030] In parts by weight, add 100 parts of pure water and 1.5 parts of gelatin into the pressure reaction vessel, and stir evenly.
[0031] Step 2. Preparation of the oil phase
[0032] Mix the oil phase components in the following proportions in a beaker and stir evenly;
[0033]
[0034] Step 3. Suspension polymerization
[0035] Add the oil phase solution prepared in the beaker in step 1.2 to the pressure reaction kettle with the prepared water phase in step 1.1, react at 90°C for 15 hours, discharge after the reaction, discharge after the reaction, and wash the microspheres to The water is clear and the product white ball is obtained.
[0036] Step 4. Chloromethylation reaction
[0037] In a 500L reactor, immerse 100Kg of white balls in 300Kg of chloromethyl ether, add 30Kg of zinc chloride as a catalyst, and carry out the chloromethylation reaction at 40℃ for 24h to obtain low chloromethylation. Crosslinked macroporous polystyrene-di...
Embodiment 2
[0041] Step 1. Preparation of the water phase
[0042] In parts by weight, add 100 parts of pure water and 2 parts of gelatin into the pressure reactor, and stir evenly.
[0043] Step 2. Preparation of the oil phase
[0044] Mix the oil phase components in the following proportions in a beaker and stir evenly;
[0045]
[0046] Step 3. Suspension polymerization
[0047] Add the oil phase solution prepared in the beaker in step 1.2 to the pressure reaction kettle with the prepared water phase in step 1.1, and react at 70°C for 24 hours. After the reaction, the material is discharged. After the reaction, the material is discharged and the microspheres are washed with water. The water is clear and the product white ball is obtained.
[0048] Step 4. Chloromethylation reaction
[0049] In a 500L reactor, immerse 100Kg of white balls in 500Kg of chloromethyl ether, add 20Kg of zinc chloride as a catalyst, and carry out the chloromethylation reaction at 45°C for 15h to obtain low chloromethyla...
Embodiment 3
[0053] Step 1. Preparation of the water phase
[0054] In parts by weight, add 100 parts of pure water and 0.5 parts of polyvinyl alcohol into the pressure reactor, and stir evenly. Step 2. Preparation of the oil phase
[0055] Mix the oil phase components in the following proportions in a beaker and stir evenly;
[0056]
[0057] Step 3. Suspension polymerization
[0058] Add the oil phase solution prepared in the beaker in step 1.2 to the pressure reaction kettle containing the prepared water phase in step 1.1, and react at 110°C for 10 hours. After the reaction, the material is discharged, and the material is discharged after the reaction. The water is clear and the product white ball is obtained.
[0059] Step 4. Chloromethylation reaction
[0060] In a 500L reactor, soak 100Kg of white balls in 200Kg of chloromethyl ether, add 50Kg of zinc chloride as a catalyst, and carry out the chloromethylation reaction at a temperature of 20°C for 40h to obtain chloromethylation Low-crosslin...
PUM
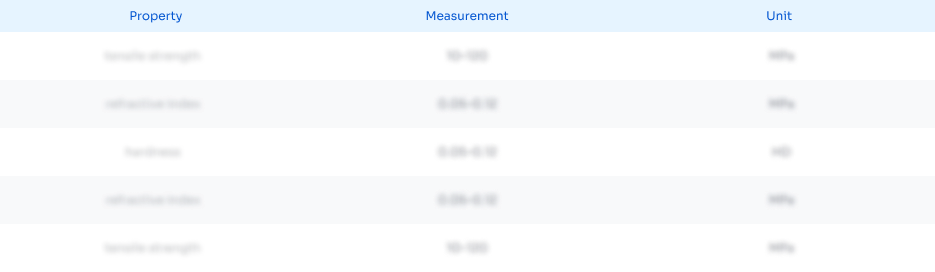
Abstract
Description
Claims
Application Information

- R&D
- Intellectual Property
- Life Sciences
- Materials
- Tech Scout
- Unparalleled Data Quality
- Higher Quality Content
- 60% Fewer Hallucinations
Browse by: Latest US Patents, China's latest patents, Technical Efficacy Thesaurus, Application Domain, Technology Topic, Popular Technical Reports.
© 2025 PatSnap. All rights reserved.Legal|Privacy policy|Modern Slavery Act Transparency Statement|Sitemap|About US| Contact US: help@patsnap.com