Cellulose-reinforcement disc-adhesion-prevention squeaking-prevention abrasion-resistant braking material and preparation method thereof
A brake material, cellulose technology, applied in the direction of chemical instruments and methods, other chemical processes, etc.
- Summary
- Abstract
- Description
- Claims
- Application Information
AI Technical Summary
Problems solved by technology
Method used
Image
Examples
Embodiment 1
[0036] The ratio of cotton linters is MgCl 2 :MgSO 4 = 5:3 solution of 3mol / L, soaked in ammonia water at 30°C for half an hour, then filtered and dried to obtain cellulose fluff with flame-retardant effect; place the fluff in a high-speed opener and spray After pouring the aluminum ester coupling agent alcohol solution, the fluffy short fleece was heated at 80°C for 30 minutes. Take 10 parts of the above-mentioned treated cotton linters, 18 parts of modified phenolic resin, 6 parts of powdered rubber with pre-crosslinked styrene-butadiene rubber as the core layer of floating beads, 6 parts of epoxy soybean oil, and 300 meshes of burnt gem mineral powder 5 parts, 15 parts of carbonaceous material, 40 parts of 200 mesh barite powder.
[0037] The above-mentioned materials are mixed in a Z-type mixer, and the positive and negative rotations are switched every 3 minutes. The total mixing time is controlled within 15 minutes, and then the molded powder is obtained by discharging...
Embodiment 2
[0047] Woodworking sawdust passed through a 40-mesh sieve, sprayed with a dilute solution of melamine-tri(butoxyethyl) phosphate (TBEP) flame retardant, the spraying amount was 10% of the woodworking sawdust, and then pre-baked at 80°C for 30 minutes, and then the same Embodiment 1 makes the anti-stick disc anti-whistling brake pad, and the physical and mechanical properties of the gained brake pad are as follows:
[0048]
[0049] The numerical comparison of the wear rate of the brake pads made in embodiment 2 and embodiment 1 is as follows Figure 4 Shown:
[0050] The anti-whistling and anti-sticking disk test procedure of the brake pad produced in embodiment 2 is the same as that of embodiment 1, and there is no sharp whistling sound and no sticking brake disc phenomenon.
PUM
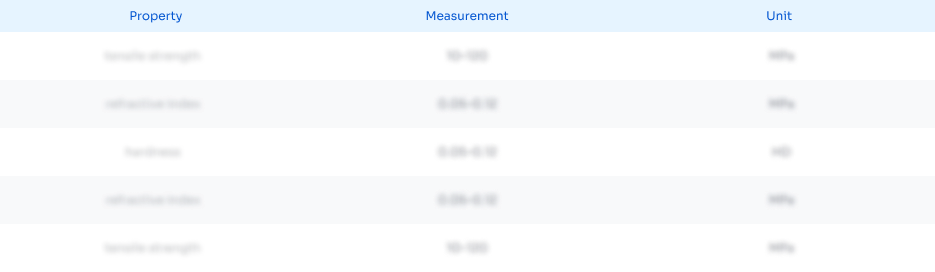
Abstract
Description
Claims
Application Information

- R&D Engineer
- R&D Manager
- IP Professional
- Industry Leading Data Capabilities
- Powerful AI technology
- Patent DNA Extraction
Browse by: Latest US Patents, China's latest patents, Technical Efficacy Thesaurus, Application Domain, Technology Topic, Popular Technical Reports.
© 2024 PatSnap. All rights reserved.Legal|Privacy policy|Modern Slavery Act Transparency Statement|Sitemap|About US| Contact US: help@patsnap.com