Method for processing high-copper-silver smelting slag
A smelting slag and high-copper technology, applied in the direction of improving process efficiency, can solve the problems of long production cycle, low equipment utilization rate, poor operating environment, etc., and achieve the effects of low cost, pollution avoidance and loss reduction
- Summary
- Abstract
- Description
- Claims
- Application Information
AI Technical Summary
Problems solved by technology
Method used
Image
Examples
Embodiment 1
[0016] The main components and weight percentages of high-copper-silver smelting slag are: silver: 0.9826%, copper: 54.35%, arsenic: 6.95%, lead: 10.14%, antimony: 13.87%, iron: 3.07%.
[0017] refer to figure 1 As shown, it is a process flow chart of the embodiment of the present invention for treating high-copper-silver smelting slag.
[0018] Step 1: Take the above-mentioned high-copper-silver smelting slag and pulverize it to 300 mesh through high-pressure water in a molten state.
[0019] Step 2: Add 100 g of pulverized high copper and silver smelting slag, 150 g / L of sulfuric acid, and 20 g / L of ferric sulfate into a 2L high-pressure reactor, with a liquid-solid ratio of 8:1. Oxygen was introduced into the high-pressure reactor, the pressure was controlled at 1.5 MPa, and the reaction time was 3 hours under the conditions of 150°C. High-efficiency leaching of copper in high-copper silver smelting slag under the condition of high pressure oxygen. After the reaction is ...
Embodiment 2
[0031] The main components and contents of high copper and silver smelting slag: silver: 1.1024%, copper: 53.03%, arsenic: 7.01%, lead: 11.09%, antimony: 13.01%, iron: 4.12%.
[0032] refer to figure 1 As shown, it is a process flow chart of the embodiment of the present invention for treating high-copper-silver smelting slag.
[0033] Step 1: Take the above-mentioned high-copper-silver smelting slag and pulverize it to 400 mesh through high-pressure nitrogen in a molten state.
[0034] Step 2: Add 100 g of pulverized high copper and silver smelting slag, 180 g / L of sulfuric acid, and 30 g / L of ferric sulfate into a 2L high-pressure reactor, with a liquid-solid ratio of 10:1. Oxygen was introduced into the high-pressure reactor, the pressure was controlled at 2.3 MPa, and the reaction time was 5 hours under the conditions of 180°C. High-efficiency leaching of copper in high-copper silver smelting slag under the condition of high pressure oxygen. After the reaction is comple...
Embodiment 3
[0046] The main components and contents of high copper and silver smelting slag: silver: 1.3715%, copper: 51.03%, arsenic: 7.14%, lead: 12.49%, antimony: 12.36%, iron: 4.78%.
[0047] refer to figure 1 As shown, it is a process flow chart of the embodiment of the present invention for treating high-copper-silver smelting slag.
[0048] Step 1: Take the above-mentioned high-copper-silver smelting slag and pulverize it to 400 mesh through high-pressure nitrogen in a molten state.
[0049] Step 2: Add 100 g of pulverized high copper and silver smelting slag, 180 g / L of sulfuric acid, and 30 g / L of ferric sulfate into a 2L high-pressure reactor, with a liquid-solid ratio of 10:1. Oxygen was introduced into the high-pressure reactor, the pressure was controlled at 3.0 MPa, and the reaction time was 4 hours under the conditions of 160°C. High-efficiency leaching of copper in high-copper silver smelting slag under the condition of high pressure oxygen. After the reaction is comple...
PUM
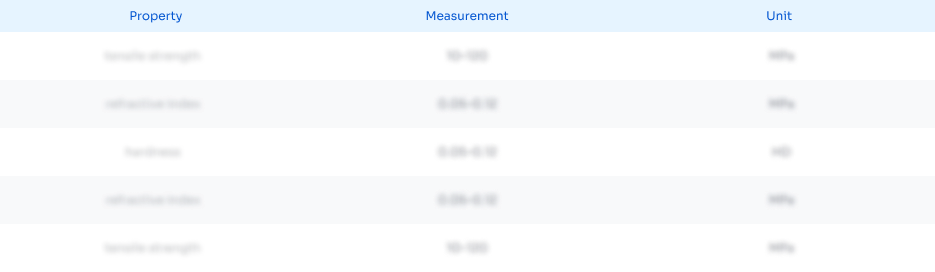
Abstract
Description
Claims
Application Information

- R&D
- Intellectual Property
- Life Sciences
- Materials
- Tech Scout
- Unparalleled Data Quality
- Higher Quality Content
- 60% Fewer Hallucinations
Browse by: Latest US Patents, China's latest patents, Technical Efficacy Thesaurus, Application Domain, Technology Topic, Popular Technical Reports.
© 2025 PatSnap. All rights reserved.Legal|Privacy policy|Modern Slavery Act Transparency Statement|Sitemap|About US| Contact US: help@patsnap.com