Manganese carbonate ore leaching method based on two-stage leaching
A technology of manganese carbonate ore and two-stage leaching, which is applied in the direction of improving process efficiency, etc., to achieve the effects of large production flexibility, improved leaching rate, and reduced times of entering and leaving the tank.
- Summary
- Abstract
- Description
- Claims
- Application Information
AI Technical Summary
Problems solved by technology
Method used
Image
Examples
Embodiment 1
[0047] a kind of like figure 1 Shown is based on the manganese carbonate ore leaching method of two-stage leaching, comprises the following steps:
[0048] (1) After grinding 28t of high-grade manganese carbonate ore (imported ore, see Table 1 below for its grade), put it into the reaction tank, add 0.7t of concentrated sulfuric acid and 300m of anolyte 3 (The composition of the anolyte is shown in Table 2 below), the leaching reaction time is 2h, the ore leaching rate is 50.2%, and the manganese content in the leaching slag is 19.5%;
[0049] (2) After the leaching is finished, the remaining acid in the detection reaction is 1g / L, and the neutralizing agent ammonia water is added according to the concentration of the remaining acid in the reaction to neutralize, and air is introduced to remove impurities;
[0050] (3) Use a thickener to carry out liquid-solid separation of the pulp after impurity removal in step (2), wherein the solution obtained is an electrolytic qualified...
Embodiment 2
[0062] a kind of like figure 1 Shown is based on the manganese carbonate ore leaching method of two-stage leaching, comprises the following steps:
[0063] (1) Grind 50t of high-grade manganese carbonate ore (imported ore, see the above table 1 for its grade), put it into the reaction tank, add 11.5t of concentrated sulfuric acid and 300m of anolyte 3 (The composition of the anolyte is shown in Table 2), the leaching reaction time is 4h, the ore leaching rate is 61.3%, and the manganese content in the leaching slag is 16.8%;
[0064] (2) After the leaching ends, the detection of residual acid in reaction is 2g / L, and according to the concentration of residual acid in reaction, artificially synthesized manganese carbonate slurry and ammonia are added for neutralization, and air is introduced to remove impurities;
[0065] (3) The ore pulp after impurity removal in step (2) is carried out liquid-solid separation using a thickener, wherein the solution obtained is an electrolyti...
Embodiment 3
[0071] a kind of like figure 1 Shown is based on the manganese carbonate ore leaching method of two-stage leaching, comprises the following steps:
[0072] (1) Grind 40t of high-grade manganese carbonate ore (imported ore, see the above table 1 for its grade) into the reaction tank, add 12.8t of concentrated sulfuric acid and 300m of anolyte 3 (The composition of the anolyte is shown in Table 2), the leaching reaction time is 6h, the ore leaching rate is 84.75%, and the manganese content of the leaching slag is 8.6%;
[0073] (2) After the leaching is finished, it is detected that the residual acid in the reaction is 4g / L. According to the concentration of the residual acid in the reaction, artificially synthesized manganese carbonate slurry, double fly powder and ammonia water are added for neutralization, and air is introduced to remove impurities;
[0074] (3) The ore pulp after removing impurities in step (2) is separated from liquid and solid by pressure filtration, wher...
PUM
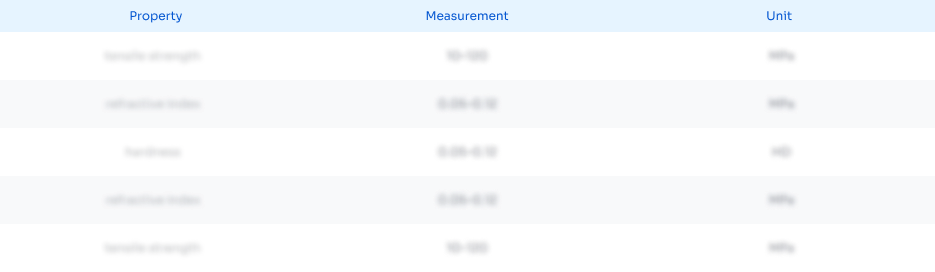
Abstract
Description
Claims
Application Information

- R&D
- Intellectual Property
- Life Sciences
- Materials
- Tech Scout
- Unparalleled Data Quality
- Higher Quality Content
- 60% Fewer Hallucinations
Browse by: Latest US Patents, China's latest patents, Technical Efficacy Thesaurus, Application Domain, Technology Topic, Popular Technical Reports.
© 2025 PatSnap. All rights reserved.Legal|Privacy policy|Modern Slavery Act Transparency Statement|Sitemap|About US| Contact US: help@patsnap.com