Titanium alloy skull repair prosthesis preparation method based on metal powder laser sintering 3D molding technology
A laser sintering and metal powder technology, applied in prostheses, bone implants, medical science, etc., can solve problems such as processing difficulties, and achieve the effects of overcoming processing difficulties, improving surface accuracy, and rapid prototyping
- Summary
- Abstract
- Description
- Claims
- Application Information
AI Technical Summary
Problems solved by technology
Method used
Image
Examples
Embodiment Construction
[0032] Such as figure 1 , figure 2 As shown, a method for preparing a titanium alloy skull repair prosthesis based on metal powder laser sintering 3D molding technology includes the following steps:
[0033] S1. Use imaging technology to scan patients with skull repair, and reconstruct the model of the missing part of the skull through reverse engineering; imaging technology includes CT, DR and other imaging technologies.
[0034] S2, utilize Pro / e software to carry out three-dimensional modeling to the model of above-mentioned reconstruction skull missing part;
[0035] S3. Preprocessing the skull repair prosthesis 1 model generated by the above-mentioned three-dimensional modeling:
[0036] Selection of molding angle: Skull repair prosthesis 1 is a thin-walled part. During processing, the molding effect of both flat and fully erect angles will have defects such as sagging and deformation, and even lead to molding failure. Since the concave surface 2 of the skull repair p...
PUM
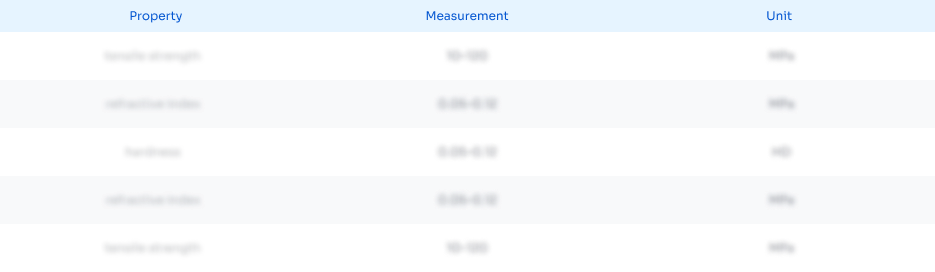
Abstract
Description
Claims
Application Information

- R&D Engineer
- R&D Manager
- IP Professional
- Industry Leading Data Capabilities
- Powerful AI technology
- Patent DNA Extraction
Browse by: Latest US Patents, China's latest patents, Technical Efficacy Thesaurus, Application Domain, Technology Topic, Popular Technical Reports.
© 2024 PatSnap. All rights reserved.Legal|Privacy policy|Modern Slavery Act Transparency Statement|Sitemap|About US| Contact US: help@patsnap.com