Chromium-based coke removal and ash removal coal saving agent composition for boiler and preparation method for composition
A technology of coal-saving agent and composition, which is applied in the direction of fuel additives, petroleum industry, solid fuel, etc., can solve the problems of high strength of coke slag, inability to remove coking, and ineffective effect, etc. The effect of reducing the amount of coal and saving coal is remarkable
- Summary
- Abstract
- Description
- Claims
- Application Information
AI Technical Summary
Problems solved by technology
Method used
Examples
Embodiment 1
[0053] Embodiment 1, take raw material by following component and weight: Chromium trioxide 75kg, copper sulfate 16kg, cerium oxide 8kg, barium molybdate 14kg, manganese dioxide 6kg, potassium permanganate 12kg, potassium chlorate 10kg zinc oxide 20kg, cobalt sulfate 13kg, potassium carbonate 30kg, activated attapulgite 34kg and penetrant JFC 0.1kg. The above-mentioned raw materials in parts by weight are prepared into boiler chromium-based coke-removing, ash-removing and coal-saving agent compositions according to the following preparation method:
[0054] 1. Mix the chromium trioxide, copper sulfate, cerium oxide and barium molybdate in the above weight parts evenly, then crush them with a grinder and pass through an 80-mesh sieve to obtain the first powder;
[0055] 2. After the above-mentioned active attapulgite clay is crushed through a 20-mesh sieve, it is added to the first powder, and then mixed and stirred for 30 minutes until uniform, and the second powder is obtaine...
Embodiment 2
[0058] Embodiment 2, take raw material by following component and weight: Dichromium trioxide 62kg, copper sulfate 10kg, cerium oxide 12kg, barium molybdate 13kg, manganese dioxide 10kg, potassium permanganate 15kg, potassium chlorate 11kg, zinc oxide 22kg, cobalt sulfate 9kg, potassium carbonate 25kg, activated attapulgite 30kg and penetrant JFC 0.2kg. The preparation method of this embodiment is the same as that of Example 1.
Embodiment 3
[0059] Embodiment 3, take raw material by following component and weight: Dichromium trioxide 60kg, copper sulfate 15kg, cerium oxide 10kg, barium molybdate 10kg, manganese dioxide 12kg, potassium permanganate 14kg, potassium chlorate 6kg, zinc oxide 15kg, cobalt sulfate 10kg, potassium carbonate 28kg, activated attapulgite 40kg and penetrant JFC 0.3kg. The preparation method of this embodiment is the same as that of Example 1.
PUM
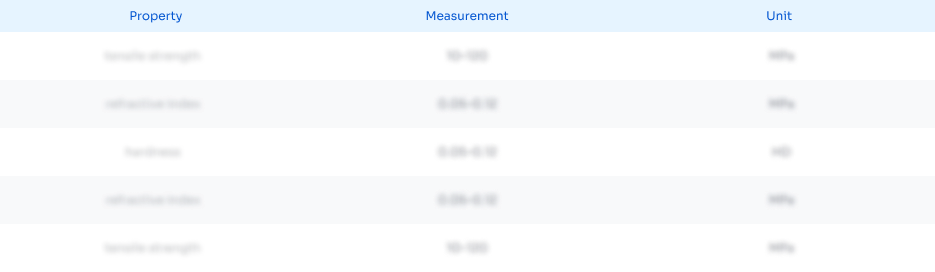
Abstract
Description
Claims
Application Information

- R&D
- Intellectual Property
- Life Sciences
- Materials
- Tech Scout
- Unparalleled Data Quality
- Higher Quality Content
- 60% Fewer Hallucinations
Browse by: Latest US Patents, China's latest patents, Technical Efficacy Thesaurus, Application Domain, Technology Topic, Popular Technical Reports.
© 2025 PatSnap. All rights reserved.Legal|Privacy policy|Modern Slavery Act Transparency Statement|Sitemap|About US| Contact US: help@patsnap.com