Buried and embedded copper block PCB manufacturing method
A technology of PCB board and production method, which is applied in the direction of multilayer circuit manufacturing, printed circuit manufacturing, and printed circuits connected with non-printed electrical components, can solve the problem that stamping equipment cannot apply pressure evenly, resin cannot be effectively removed, and copper Block can not be effectively positioned and other problems, to ensure product quality effect, realize standardized production, avoid the effect of copper block falling
- Summary
- Abstract
- Description
- Claims
- Application Information
AI Technical Summary
Problems solved by technology
Method used
Examples
Embodiment Construction
[0029] In order to enable those skilled in the art to better understand the technical solution of the present invention, the product of the present invention will be further described in detail below in conjunction with examples.
[0030] A kind of manufacture method of embedding copper block PCB board, processing on the PCB board is used for the slot hole that copper block is embedded and the metallized slot hole that is used for copper block embedding, comprises the following steps:
[0031] 1. Pretreatment of buried slot holes: According to the conventional process, the inner layer core board circuit production, AOI inspection, slot milling, browning and prepreg cutting, drilling, and slot milling are carried out, and the slot holes for buried copper blocks are processed.
[0032] 2. Lamination of buried copper blocks mainly includes the following processes:
[0033] 2.1. The pre-treatment process of the buried copper block pressing is to perform the pre-treatment process o...
PUM
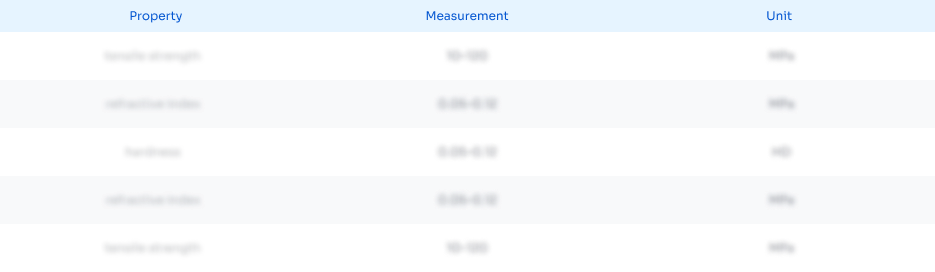
Abstract
Description
Claims
Application Information

- R&D
- Intellectual Property
- Life Sciences
- Materials
- Tech Scout
- Unparalleled Data Quality
- Higher Quality Content
- 60% Fewer Hallucinations
Browse by: Latest US Patents, China's latest patents, Technical Efficacy Thesaurus, Application Domain, Technology Topic, Popular Technical Reports.
© 2025 PatSnap. All rights reserved.Legal|Privacy policy|Modern Slavery Act Transparency Statement|Sitemap|About US| Contact US: help@patsnap.com