Double-component aluminum metal anti-corrosion repairing agent and preparation method thereof
A repair agent, two-component technology, applied in the direction of adhesives, adhesive types, adhesive additives, etc., can solve the problems of poor acid and alkali resistance, low cohesive strength, damaged bonding effect, etc., and achieve excellent high temperature resistance , good water resistance, and the effect of improving the bonding effect
- Summary
- Abstract
- Description
- Claims
- Application Information
AI Technical Summary
Problems solved by technology
Method used
Examples
Embodiment 1
[0020] Repairing agent preparation of the present invention and use process are as follows:
[0021] (1) Preparation of reinforcing filler (modified attapulgite / nano silica composite powder):
[0022] (a) Weigh 100g of attapulgite clay with a fineness of 200-400 mesh, put it into 800-1000ml of distilled water, and treat it with 50-100ml of hydrochloric acid with a concentration of 1mol / L at 80-100°C for 1-3 hours while stirring 2 to 4 hours to prepare the suspension;
[0023] (b) Add 5-10 mL of composite active agent to the suspension, add 15 g of nano-silicon oxide, add NaOH solution dropwise to adjust the pH of the suspension to 6-8, and then stir for 2-4 hours to prepare the suspension;
[0024] (c) Centrifuge the suspension at a speed of 3500r / min for 5-10 minutes, dry the recovered solids, and grind them finely to obtain the modified attapulgite powder.
[0025] (2) Take 30g of tetrahydrofuran and pour it into a stirrer, add 20g of E14 type bisphenol A epoxy resin to it...
Embodiment 2
[0032] Repairing agent preparation of the present invention and use process are as follows:
[0033] (1) Preparation of reinforcing filler (modified attapulgite / nano silica composite powder):
[0034] (a) Weigh 100g of attapulgite clay with a fineness of 200-400 mesh, put it into 800-1000ml of distilled water, and treat it with 50-100ml of hydrochloric acid with a concentration of 1mol / L at 80-100°C for 1-3 hours while stirring 2 to 4 hours to prepare the suspension;
[0035] (b) Add 5-10 mL of composite active agent to the suspension, add 15 g of nano-silicon oxide, add NaOH solution dropwise to adjust the pH of the suspension to 6-8, and then stir for 2-4 hours to prepare the suspension;
[0036] (c) Centrifuge the suspension at a speed of 3500r / min for 5-10 minutes, dry the recovered solids, and grind them finely to obtain the modified attapulgite powder.
[0037] (2) Take 30g of tetrahydrofuran and pour it into a stirrer, add 25g of E14 type bisphenol A epoxy resin to it...
Embodiment 3
[0044] Repairing agent preparation of the present invention and use process are as follows:
[0045] (1) Prepare the reinforcing filler according to the method of Example 1.
[0046] (2) Take 35g of tetrahydrofuran and pour it into a stirrer, add 20g of E44 type bisphenol A epoxy resin to it, stir fully with a cross blade stirrer, the stirring speed is 3000 rpm, and the stirring time is 60 minutes;
[0047] (3) Put 22g of modified attapulgite clay powder, 6g of nano-zirconia, 6g of Tween 20 active agent and 0.5g of defoamer for epoxy resin into the mixing system of step (1), and stir well, The stirring time is 2 hours, and the stirred slurry is vacuum defoamed to make component A for use;
[0048] (4) Put 15g of linear polyamine polyamide resin, 15g of methyltriethoxysilane and 3g of alkylethylenediamine into a cross-blade stirrer and stir fully at a stirring speed of 3000 rpm, stirring Time is 60 minutes, make component B, stand-by;
[0049] (5) Soak the aluminum metal par...
PUM
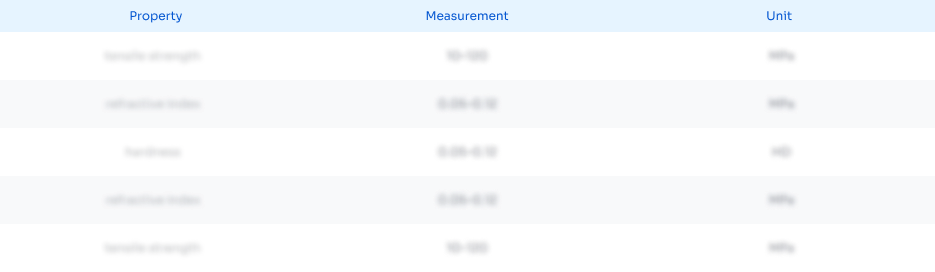
Abstract
Description
Claims
Application Information

- R&D Engineer
- R&D Manager
- IP Professional
- Industry Leading Data Capabilities
- Powerful AI technology
- Patent DNA Extraction
Browse by: Latest US Patents, China's latest patents, Technical Efficacy Thesaurus, Application Domain, Technology Topic, Popular Technical Reports.
© 2024 PatSnap. All rights reserved.Legal|Privacy policy|Modern Slavery Act Transparency Statement|Sitemap|About US| Contact US: help@patsnap.com