Preparation method of special low-density grinding column for cement grinding mill
A low-density, cement grinding technology, applied in the field of functional ceramics preparation, can solve the problems of high price, high evaporation heat, and consumption, and achieve the advantages of simple operation, reduced power consumption and grinding body loss, and promoted densification and sintering Effect
- Summary
- Abstract
- Description
- Claims
- Application Information
AI Technical Summary
Problems solved by technology
Method used
Examples
Embodiment 1
[0030] 1.1 Weigh 250 kg of bauxite, 80 kg of alumina powder, 3 kg of chromium oxide, 1 kg each of zirconia, calcium oxide, magnesium oxide, and iron oxide to make raw materials;
[0031] 1.2 Add 3 kg of aluminum sol and 3 kg of silica sol to the slurry raw material configured in Example 1.1 after grinding for 5 hours, and then add aluminum chloride, magnesium chloride, zirconium chloride, calcium chloride, and barium chloride after grinding for 5 hours 0.2 kg each, add 1 kg of sodium hydroxide after grinding for 3 hours, add 1 kg of one or more precipitants after grinding for 3 hours, and finally grind for 3 hours;
[0032] 1.3 The slurry obtained in Example 1.2 is spray-dried, then machine-pressed, and the machine-pressed abrasive is 35MPa / m 2 The pressure was kept for 2 minutes;
[0033] 1.4 Dry the sample obtained in Example 1.3 and put it into a programmable temperature-controlled furnace for segmental calcination. In the first stage, the temperature is raised from room t...
Embodiment 2
[0035] 1.1 Weigh 115 kg of bauxite, 115 kg of alumina powder, 2 kg of chromium oxide, 1 kg each of zirconia, calcium oxide, magnesium oxide, and iron oxide;
[0036] 1.2 Add 2 kg of aluminum sol and 2 kg of silica sol to the raw materials configured in Example 1.1 after grinding for 5 hours, and add aluminum chloride, magnesium chloride, zirconium chloride, calcium chloride, barium chloride each 0.13 after grinding for 5 hours kg, add 1.5 kg of calcium hydroxide after grinding for 3 hours, and finally grind for 3 hours;
[0037] 1.3 The slurry obtained in Example 1.2 is spray-dried, and then machine-pressed, and the machine-pressed abrasive is 70MPa / m 2 Keep the pressure for 2.5 minutes;
[0038] 1.4 After drying the sample obtained in Example 1.3, put it into a programmable temperature-controlled furnace for segmental calcination. In the first stage, the temperature is raised from room temperature to 900°C at a heating rate of 8°C / min. In the second stage, the heating rate i...
Embodiment 3
[0040] 1.1 Weigh 115 kg of bauxite, 115 kg of alumina powder, 1.5 kg of chromium oxide, 1 kg each of zirconia, calcium oxide, magnesium oxide, and iron oxide to make raw materials;
[0041] 1.2 After grinding the slurry prepared in Example 1.1 for 5 hours, add 4 kg of aluminum sol and 4 kg of silica sol, and then add aluminum chloride, magnesium chloride, zirconium chloride, calcium chloride, and barium chloride after grinding for 5 hours. 0.1 kg, add 1 catties of strong calcium oxide after grinding for 3 hours, and finally grind for 3 hours;
[0042] 1.3 The slurry obtained in Example 1.2 is spray-dried, and then machine-pressed, and the machine-pressed abrasive is 70MPa / m 2 Keep the pressure for 2.5 minutes;
[0043] 1.4 After drying the sample obtained in Example 1.3, put it into a programmable temperature-controlled furnace for segmental calcination. In the first stage, the temperature is raised from room temperature to 900°C at a heating rate of 8°C / min. In the second sta...
PUM
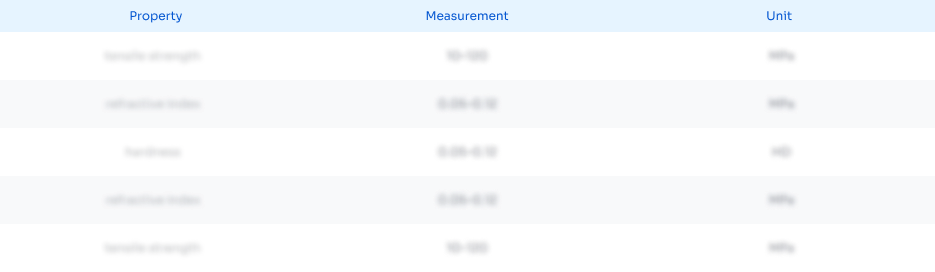
Abstract
Description
Claims
Application Information

- R&D
- Intellectual Property
- Life Sciences
- Materials
- Tech Scout
- Unparalleled Data Quality
- Higher Quality Content
- 60% Fewer Hallucinations
Browse by: Latest US Patents, China's latest patents, Technical Efficacy Thesaurus, Application Domain, Technology Topic, Popular Technical Reports.
© 2025 PatSnap. All rights reserved.Legal|Privacy policy|Modern Slavery Act Transparency Statement|Sitemap|About US| Contact US: help@patsnap.com