Oil-resistant, high-temperature-resistant and flame-retardant thermoplastic elastomer cable material and preparation method thereof
A thermoplastic elastomer, high-temperature-resistant technology, applied in the direction of insulating cables, plastic/resin/wax insulators, cables, etc., can solve the problems of unfavorable energy saving, high processing temperature, high hardness, etc., and achieve reasonable material selection and ratio , The process is short and the extrusion temperature is reduced
- Summary
- Abstract
- Description
- Claims
- Application Information
AI Technical Summary
Problems solved by technology
Method used
Image
Examples
Embodiment 1
[0022]First, 20 parts of a mixture of 10% SEBS by mass percentage and 90% TPV by mass percentage and 2 parts of naphthenic oil as an extender oil that were weighed in parts by weight were put into a high-speed mixer and heated at room temperature Stir at low speed for 10 minutes, then add 15 parts of ethylene-vinyl acetate copolymer (EVA), 8 parts of single block copolymerized polypropylene, and compatibilizer to the high-speed mixer. That is, 1 part of EVA grafted by maleic anhydride, a mixture of 9 parts of decabromodiphenylethane and antimony trioxide as a flame retardant, 0.2 parts of liquid paraffin as a lubricant, and 10100.4 parts of an antioxidant , and continue to stir evenly to obtain a mixture, then introduce the mixture into a conical feeding hopper, melt and extrude it through a twin-screw extruder, cool and pelletize, and obtain an oil-resistant, high-temperature, flame-retardant thermoplastic elastomer cable material, wherein: The temperature of zone 1 to zone 9...
Embodiment 2
[0024] First, 35 parts of a mixture of 60% SEBS and 40% TPV and 6 parts of paraffin oil as filler oil are put into a high-speed mixer and weighed in parts by weight. Stir at low speed for 5 minutes at room temperature, then add 10 parts of chlorinated polyethylene (CPE), 5 parts of homopolypropylene, and compatibilizer by weight to the high-speed mixer. 3 parts of SEBS grafted with anhydride, 25 parts of a mixture of magnesium hydroxide and zinc borate in any weight ratio as a flame retardant, 0.6 parts of high-viscosity silicone oil as a lubricant and 1680.8 parts of an antioxidant as an antioxidant, and Continue to stir evenly to obtain a mixture, then introduce the mixture into a conical feeding hopper, melt and extrude through a twin-screw extruder, cool and pelletize, and obtain an oil-resistant, high-temperature, flame-retardant thermoplastic elastomer cable material, wherein: the aforementioned double The temperature of zone 1 to zone 9 and the head of the screw extrude...
Embodiment 3
[0026] First, 27 parts of a mixture of 35% SEBS and 65% TPV and 4 parts of DOTP as filler oil weighed in parts by weight were put into a high-speed mixer and cooled at room temperature at a low speed. Stir for 8 minutes, and then add 5 parts of oil-resistant modifiers weighed in parts by weight, that is, acrylate terpolymers (Sunigum P95, ie, acrylate elastic modifiers), and a single block copolymerization type to the high-speed mixer. Mixture of 5 parts of polypropylene and 5 parts of homopolymerized polypropylene, 5 parts of ethylene-methyl acrylate-glycidyl methacrylate (EMA-GMA) as a compatibilizer, and 5 parts of flame retardant as aluminum phenyl hypophosphite 15 parts, lubricant is polyethylene wax or 0.4 part of polyethylene glycol ester and antioxidant is 10240.6 parts of antioxidant, and continue to stir evenly to obtain a mixture, then introduce the mixture into a conical feeding hopper, and pass through a twin-screw The extruder is melted and extruded, cooled and p...
PUM
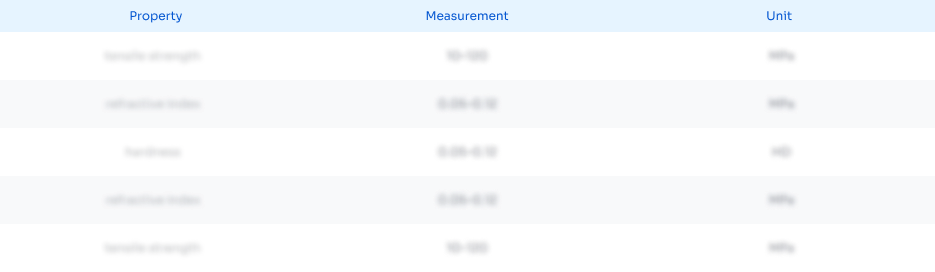
Abstract
Description
Claims
Application Information

- R&D Engineer
- R&D Manager
- IP Professional
- Industry Leading Data Capabilities
- Powerful AI technology
- Patent DNA Extraction
Browse by: Latest US Patents, China's latest patents, Technical Efficacy Thesaurus, Application Domain, Technology Topic, Popular Technical Reports.
© 2024 PatSnap. All rights reserved.Legal|Privacy policy|Modern Slavery Act Transparency Statement|Sitemap|About US| Contact US: help@patsnap.com