Preparation method of slow-release solid polycarboxylic acid water reducing agent
A polycarboxylic acid, slow-release technology, applied in the field of polycarboxylic acid-based water-reducing agents, can solve the problems of difficulty in meeting the requirements of long-distance transportation of ready-mixed concrete, slump loss, and the lack of slow-release properties of water-reducing agents. , to achieve the effect of excellent water reduction and dispersion effect, stable state and excellent performance indicators
- Summary
- Abstract
- Description
- Claims
- Application Information
AI Technical Summary
Problems solved by technology
Method used
Image
Examples
Embodiment 1
[0022] Step (1) Pretreatment of acrylic small monomers with unsaturated double bonds: Stir 1 mol of acrylic acid and 0.3 mol of ethylenediamine for 1 hour without heat source;
[0023] (2) Preparation of slow-release solid polycarboxylate water reducer: 0.31 mol of acrylic acid pretreated in the above step (1) and 1 mol of allyl polyoxyethylene ether with a molecular weight of 1400 are heated to 65 ° C in a kettle, and the Allyl polyoxyethylene ether is in a liquid state. Add 0.01mol of azobisisoheptanonitrile and 0.5mol of mercaptoacetic acid to the kettle, then dropwise add 3mol of hydroxypropyl acrylate to react for 2 hours and keep it warm for 3 hours. The copolymerization product is obtained through bulk polymerization in a certain environment, and becomes a solid polycarboxylate water reducer after cooling.
Embodiment 2
[0025] Step (1) Pretreatment of acrylic small monomers with unsaturated double bonds: Stir 1 mol of methacrylic acid and 0.8 mol of triethylamine for 2 hours without heat source;
[0026] (2) Preparation of slow-release solid polycarboxylate water reducer: 1 mol of methacrylic acid pretreated in the above step (1) and 1 mol of isopentenyl polyoxyethylene ether with a molecular weight of 2400 are heated to 70°C in a kettle , when the isopentenyl polyoxyethylene ether is liquid, add 0.05mol of azobisisobutyronitrile and 0.8mol of 2-mercaptopropionic acid to the kettle, then dropwise add 4mol of hydroxyethyl acrylate to react for 3h and keep warm for 2h. The reaction process is The copolymerization product is obtained through bulk polymerization in an environment without water and organic solvents, and becomes a solid polycarboxylate water reducer after cooling.
Embodiment 3
[0028] Step (1) pretreatment of acrylic small monomers with unsaturated double bonds: stirring 1 mol of maleic acid and 0.6 mol of cyclohexylamine for 3 hours without heat source;
[0029] (2) Preparation of slow-release solid polycarboxylate water reducer: 2.3 mol of maleic acid pretreated in the above step (1) and 1 mol of isopentenyl polyoxyethylene ether with a molecular weight of 2900 are heated to 75 ℃, when the isopentenyl polyoxyethylene ether is in liquid state, add 0.1 mol of azobisisoheptanonitrile and 1 mol of sodium methacrylsulfonate to the kettle, then add 5 mol of butyl acrylate dropwise to react for 3 hours and keep it warm for 2 hours. The copolymerization product is obtained through bulk polymerization in an environment without water and organic solvents, and becomes a solid polycarboxylate water reducer after cooling.
PUM
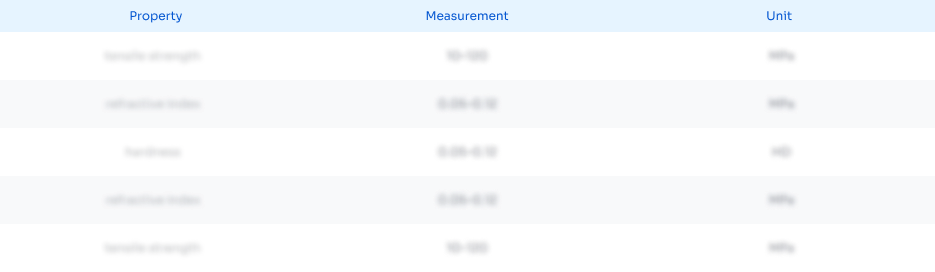
Abstract
Description
Claims
Application Information

- R&D
- Intellectual Property
- Life Sciences
- Materials
- Tech Scout
- Unparalleled Data Quality
- Higher Quality Content
- 60% Fewer Hallucinations
Browse by: Latest US Patents, China's latest patents, Technical Efficacy Thesaurus, Application Domain, Technology Topic, Popular Technical Reports.
© 2025 PatSnap. All rights reserved.Legal|Privacy policy|Modern Slavery Act Transparency Statement|Sitemap|About US| Contact US: help@patsnap.com