Preparation method of high-purity titanium powder
A titanium powder, high-purity technology, applied in the new preparation of ultra-fine high-purity titanium powder, high-pressure torsion processing and hydrogenation dehydrogenation method to prepare titanium powder composite field, can solve the problems of oxygen content reduction, particle size refinement, etc., and achieve distribution Uniform concentration, improved raw material purity, and good process performance
- Summary
- Abstract
- Description
- Claims
- Application Information
AI Technical Summary
Problems solved by technology
Method used
Examples
Embodiment 1
[0021] Preparation average particle size is 20μm, oxygen content <0.30% ultra-fine high-purity titanium powder, using molten salt electrolytic high-purity titanium as raw material, placed in a WC-Co mold, heated to 300°C and applied a pressure of 5 GPa, twisted 5 times to obtain a titanium material with ultra-fine crystal structure . During the hydrogenation process, the preheating temperature is 180°C, 280°C and 850°C, and each stage is kept for 3 hours respectively, and then the furnace temperature is lowered to 450°C before hydrogenation is performed. Keep the hydrogen gas for about 1 hour, and the hydrogenation is complete. Put the titanium hydride in a ball mill tank filled with argon gas with a ball-to-material ratio of 10:1, and use a planetary ball mill for ball milling. The speed is set to 250 r / min. When the titanium hydride powder is sent to the vacuum furnace for dehydrogenation, the vacuum degree is kept below 1kPa, and the dehydrogenation is carried out at 650°C ...
Embodiment 2
[0023] Preparation average particle size is 35μm, oxygen content <0.25% ultra-fine high-purity titanium powder, using molten salt electrolytic high-purity titanium as raw material, placed in a WC-Co mold, heated to 250 ℃ and applied 5 GPa pressure, twisted 5 times to obtain ultra-fine crystal structure of titanium . During the hydrogenation process, the preheating temperature is 160°C, 250°C and 830°C, and each stage is kept for 3 hours, and then the furnace temperature is lowered to 430°C before hydrogenation is performed. Keep the hydrogen gas for about 1 hour. After the hydrogenation is complete, the titanium hydride is placed in a ball mill tank filled with argon gas with a ball-to-material ratio of 8:1, and it is crushed by a planetary ball mill. The speed is set to 230 r / min. When the titanium hydride powder is sent to the vacuum furnace for dehydrogenation, the vacuum degree is kept below 1kPa, and the dehydrogenation is carried out at 650°C for 2 hours. The obtained p...
Embodiment 3
[0025] Preparation average particle size is 50μm, oxygen content <0.20% ultra-fine high-purity titanium powder, using molten salt electrolytic high-purity titanium as raw material, placed in a WC-Co mold, heated to 210°C and applied a pressure of 3 GPa, twisted 3 times to obtain a titanium material with ultra-fine crystal structure . During the hydrogenation process, the preheating temperature is 150°C, 250°C and 800°C, and each stage is held for 3 hours, and then the furnace temperature is lowered to 430°C before hydrogenation is performed. Keep the hydrogen gas for about 1 hour. After the hydrogenation is complete, the titanium hydride is placed in a ball mill tank filled with argon gas with a ball-to-material ratio of 8:1, and it is crushed by a planetary ball mill. The speed is set to 200 r / min. When the titanium hydride powder is sent to the vacuum furnace for dehydrogenation, the vacuum degree is kept below 1kPa, and the dehydrogenation is carried out at 680°C for 2 hour...
PUM
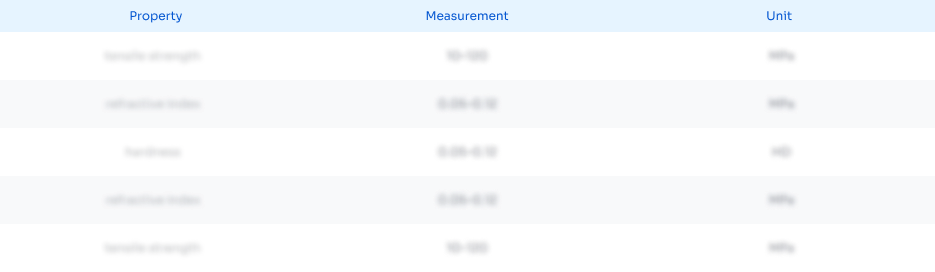
Abstract
Description
Claims
Application Information

- R&D
- Intellectual Property
- Life Sciences
- Materials
- Tech Scout
- Unparalleled Data Quality
- Higher Quality Content
- 60% Fewer Hallucinations
Browse by: Latest US Patents, China's latest patents, Technical Efficacy Thesaurus, Application Domain, Technology Topic, Popular Technical Reports.
© 2025 PatSnap. All rights reserved.Legal|Privacy policy|Modern Slavery Act Transparency Statement|Sitemap|About US| Contact US: help@patsnap.com