Tooth surface processing device and gear manufacturing method
A processing device and gear manufacturing technology, applied in the direction of gear tooth manufacturing tools, gear tooth manufacturing devices, abrasive surface adjustment devices, etc., can solve problems such as difficult to finely control processing pressure, avoid grinding burns, and improve surface roughness Effect
- Summary
- Abstract
- Description
- Claims
- Application Information
AI Technical Summary
Problems solved by technology
Method used
Image
Examples
Embodiment approach 1
[0063] Such as figure 1 As shown, the tooth surface processing device 10 according to Embodiment 1 includes a grindstone (helical-toothed grindstone) 2, a position adjustment mechanism 3, a grindstone rotation motor (grindstone rotation mechanism) 4, a rotation torque control mechanism 5, and a control mechanism 7.
[0064] As the grindstone 2, a helical grindstone in which the angle of the teeth of the helical grindstone becomes large is used. Furthermore, the grindstone 2 is made of an elastic material capable of deforming the grindstone tooth surface 21 along the shape of the processed tooth surface 11 of the gear W to be processed. The tooth thickness of the grindstone 2 is smaller than the tooth groove width of the gear W to be machined. The grindstone 2 is rotatably supported by an attachment base (not shown) with a rotation axis C as a rotation center.
[0065] The grindstone rotation motor 4 rotates the grindstone 2 around the rotation axis C via a speed reduction m...
Embodiment approach 2
[0090] The tooth surface machining device according to the second embodiment has basically the same configuration and effects as those of the tooth surface machining device 10 according to the first embodiment. Hereinafter, a description will be given centering on different configurations and effects.
[0091] The adjustment member 9 of the tooth surface machining device according to the second embodiment is different from the adjustment members 52 and 8 used in the tooth surface machining device 10 according to the first embodiment. The adjustment member 9 used in the tooth surface machining device of the second embodiment is as follows: Figure 8 As shown, one end is inserted into the gear W to be processed, and the other end 614 side of the shaft portion 61 is provided in a rotatable state with respect to a bearing portion not shown in the figure. The adjustment member 9 has a torque generating motor 91 that generates torque at the other end, and has a first measuring memb...
Embodiment 1
[0098] here, Figure 10 It is a figure which shows the system structure of the gear surface machining apparatus of this Example 1. also, Figure 10 The tooth surface machining apparatus of Example 1 exemplified in FIG. 1 is an apparatus in which the grinding stone 2 and the gear W to be machined rotate synchronously.
[0099] In the tooth surface processing apparatus of the first embodiment, the grindstone 2 is connected to the grindstone 2 with the grindstone rotation motor 4 as a spindle motor, and the helical grindstone 2 can be driven to rotate by the spindle motor 4 . In addition, the spindle motor 4 is provided with a built-in detector 4 a so that the amount of rotation of the grindstone 2 can be grasped. On the other hand, the gear W to be processed is connected to the drive servomotor 18 via the C-shaft 16 and the timing belt 17 , and the gear W to be processed can also be driven to rotate by the drive servomotor 18 . Furthermore, the grinding stone 2 connected to t...
PUM
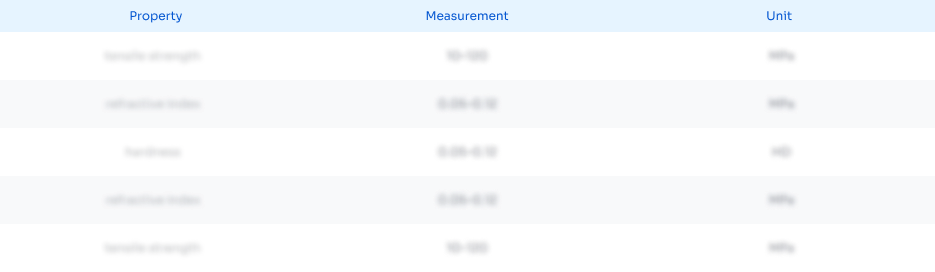
Abstract
Description
Claims
Application Information

- R&D
- Intellectual Property
- Life Sciences
- Materials
- Tech Scout
- Unparalleled Data Quality
- Higher Quality Content
- 60% Fewer Hallucinations
Browse by: Latest US Patents, China's latest patents, Technical Efficacy Thesaurus, Application Domain, Technology Topic, Popular Technical Reports.
© 2025 PatSnap. All rights reserved.Legal|Privacy policy|Modern Slavery Act Transparency Statement|Sitemap|About US| Contact US: help@patsnap.com