Method for preparing porous silicon nanowire NO2 gas sensor
A gas sensor and nanowire technology, applied in the direction of material resistance, can solve the problems of high working temperature, sensitive to humid environment, affecting the stability and sensitivity of gas sensor, and achieve large porosity, high sensitivity, and improved gas sensing performance Effect
- Summary
- Abstract
- Description
- Claims
- Application Information
AI Technical Summary
Problems solved by technology
Method used
Image
Examples
Embodiment 1
[0025] (1) Cut the silicon wafer into a suitable shape, and carry out ultrasonic cleaning with acetone, alcohol, and deionized water in sequence, and the cleaned silicon wafer is stored in H 2 o 2 and concentrated H 2 SO 4 In a solution with a volume ratio of 1:4.
[0026] (2) Save in H 2 o 2 and concentrated H 2 SO 4 An oxide layer will be formed on the surface of the silicon wafer in the mixed solution, and 5% HF is configured to remove the oxide layer.
[0027] (3) Preparation of HF and AgNO 3 A mixed solution in which the concentration of HF is 4.8M, AgNO 3 Concentration of 5mM, after magnetic stirring for a certain period of time, immerse the silicon chip in it for 60s to deposit a uniform layer of Ag particles on the surface; the silicon chip after silver plating is as attached figure 2 (a) shown.
[0028] (4) Preparation of HF and H 2 o 2 The mixed solution, in which the concentration of HF is 4.8M, H 2 o 2 The concentration is 0.1M, keep warm in a consta...
Embodiment 2
[0035] (1) Cut the silicon wafer into a suitable shape, and carry out ultrasonic cleaning with acetone, alcohol, and deionized water in sequence, and the cleaned silicon wafer is stored in H 2 o 2 and concentrated H 2 SO 4 In a solution with a volume ratio of 1:4.
[0036] (2) Save in H 2 o 2 and concentrated H 2 SO 4 An oxide layer will be formed on the surface of the silicon wafer in the mixed solution, and 5% HF is configured to remove the oxide layer.
[0037] (3) Preparation of HF and AgNO 3 A mixed solution in which the concentration of HF is 3M, AgNO 3 Concentration of 8mM, after magnetic stirring for a certain period of time, immerse the silicon chip in it for 80s to deposit a uniform layer of Ag particles on the surface; the silicon chip after silver plating is as attached figure 2 (a) shown.
[0038] (4) Preparation of HF and H 2 o 2 A mixed solution in which the concentration of HF is 3M, H 2 o 2 The concentration is 1M, keep warm in a constant temper...
Embodiment 3
[0045] (1) Cut the silicon wafer into a suitable shape, and carry out ultrasonic cleaning with acetone, alcohol, and deionized water in sequence, and the cleaned silicon wafer is stored in H 2 o 2 and concentrated H 2 SO 4 In a solution with a volume ratio of 1:4.
[0046] (2) Save in H 2 o 2 and concentrated H 2 SO 4 An oxide layer will be formed on the surface of the silicon wafer in the mixed solution, and 5% HF is configured to remove the oxide layer.
[0047] (3) Preparation of HF and AgNO 3 A mixed solution in which the concentration of HF is 6M, AgNO 3 The concentration is 8mM, after a certain period of magnetic stirring, the silicon wafer is immersed in it for 50s, so that a uniform layer of Ag particles is deposited on the surface; the silicon wafer after silver plating is as attached figure 2 (a) shown.
[0048] (4) Preparation of HF and H 2 o 2 The mixed solution, in which the concentration of HF is 4.8M, H 2 o 2 The concentration is 0.5M, keep warm i...
PUM
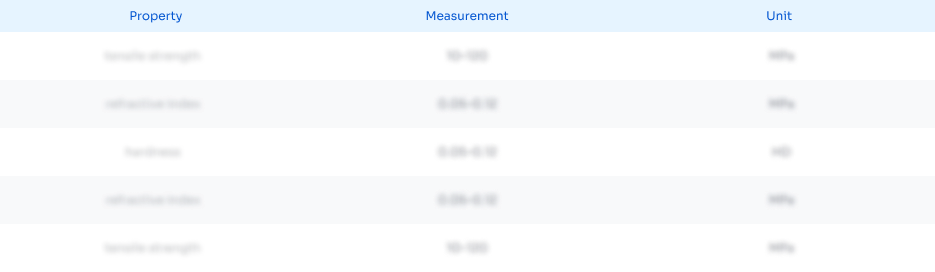
Abstract
Description
Claims
Application Information

- R&D
- Intellectual Property
- Life Sciences
- Materials
- Tech Scout
- Unparalleled Data Quality
- Higher Quality Content
- 60% Fewer Hallucinations
Browse by: Latest US Patents, China's latest patents, Technical Efficacy Thesaurus, Application Domain, Technology Topic, Popular Technical Reports.
© 2025 PatSnap. All rights reserved.Legal|Privacy policy|Modern Slavery Act Transparency Statement|Sitemap|About US| Contact US: help@patsnap.com