Preparation method of molybdenum-sulfur complex lubricating oil additive with high molybdenum content
A technology of lubricating oil additives and complexes, applied in additives, lubricating compositions, petroleum industry and other directions, can solve the problems of tribological properties that are inferior to sulfur-containing molybdenum compounds, poor oil solubility of organic molybdenum compounds, poisoning of exhaust catalysts, etc. Market competitiveness, good oil solubility, and the effect of reducing by-products
- Summary
- Abstract
- Description
- Claims
- Application Information
AI Technical Summary
Problems solved by technology
Method used
Image
Examples
Embodiment 1
[0031] The preparation method of the high molybdenum content molybdenum-sulfur complex lubricating oil additive in this embodiment includes the following steps:
[0032] Step 1. The hexavalent molybdenum compound, sulfur-containing compound and distilled water are prepared into mixed solution A at a molar ratio of 1:1.2:1.5, and then the pH of the mixed solution A is adjusted to 4; the hexavalent molybdenum compound is ammonium molybdate ; The sulfur-containing compound is sodium sulfide;
[0033] Step 2: Add dialkylamine to the mixed solution A after adjusting the pH value in step 1, stir for 75min at a temperature of 60°C, and then add a phase transfer catalyst to obtain mixed solution B; the dialkylamine The molar ratio with the hexavalent molybdenum compound in step one is 1:1.2, the mass ratio of the phase transfer catalyst to the hexavalent molybdenum compound is 1:55; the dialkylamine is didodecanamine; The phase transfer catalyst is benzyltriethylammonium chloride;
[0034]...
Embodiment 2
[0038] The preparation method of this embodiment is the same as that of embodiment 1, but the difference is that the hexavalent molybdenum compound is sodium molybdate, potassium molybdate or molybdenum trioxide, or is ammonium molybdate, sodium molybdate, or potassium molybdate. And at least two of molybdenum trioxide; the sulfur-containing compound is sodium hydrosulfide or ammonium sulfide, or at least two of sodium sulfide, sodium hydrosulfide and ammonium sulfide; the phase transfer catalyst is tetrabutyl bromide Ammonium chloride, tetrabutylammonium chloride, tetrabutylammonium hydrogen sulfate, trioctylmethylammonium chloride, dodecyltrimethylammonium chloride or tetradecyltrimethylammonium chloride, or Benzyl triethyl ammonium chloride, tetrabutyl ammonium bromide, tetrabutyl ammonium chloride, tetrabutyl ammonium hydrogen sulfate, trioctyl methyl ammonium chloride, dodecyl trimethyl ammonium chloride and At least two of tetradecyl trimethyl ammonium chloride; the alkal...
Embodiment 3
[0041] The preparation method of the high molybdenum content molybdenum-sulfur complex lubricating oil additive in this embodiment includes the following steps:
[0042] Step 1. The hexavalent molybdenum compound, sulfur-containing compound and distilled water are prepared into mixed solution A at a molar ratio of 1:0.5:1, and then the pH of the mixed solution A is adjusted to 1; the hexavalent molybdenum compound is sodium molybdate ; The sulfur-containing compound is sodium hydrosulfide;
[0043] Step 2. Add dialkylamine to the mixed solution A after adjusting the pH value in step 1, and stir for 30 minutes at a temperature of 80°C, and then add a phase transfer catalyst to obtain mixed solution B; the dialkylamine The molar ratio to the hexavalent molybdenum compound in step one is 1:0.8, the mass ratio of the phase transfer catalyst to the hexavalent molybdenum compound is 1:10; the dialkylamine is diethylamine; The phase transfer catalyst is tetrabutylammonium bromide;
[0044...
PUM
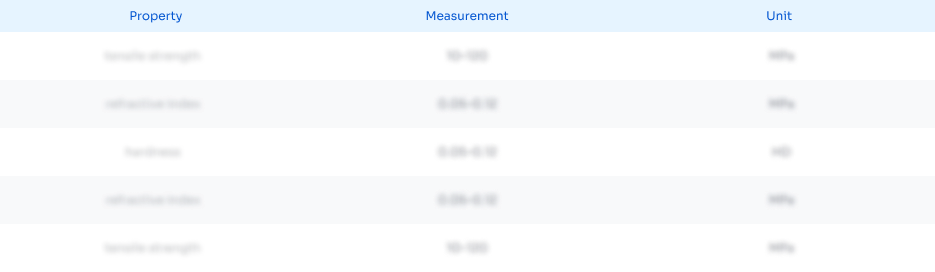
Abstract
Description
Claims
Application Information

- R&D
- Intellectual Property
- Life Sciences
- Materials
- Tech Scout
- Unparalleled Data Quality
- Higher Quality Content
- 60% Fewer Hallucinations
Browse by: Latest US Patents, China's latest patents, Technical Efficacy Thesaurus, Application Domain, Technology Topic, Popular Technical Reports.
© 2025 PatSnap. All rights reserved.Legal|Privacy policy|Modern Slavery Act Transparency Statement|Sitemap|About US| Contact US: help@patsnap.com