Method for preparing chloroethylene by reaction of chloroform and acetylene, and catalyst used in method
A technology of catalysts and vinyl chloride, applied in chemical instruments and methods, physical/chemical process catalysts, chemical/physical processes, etc., can solve pollution, poisonous and other problems, and achieve the effect of simple process
- Summary
- Abstract
- Description
- Claims
- Application Information
AI Technical Summary
Problems solved by technology
Method used
Examples
Embodiment 1
[0023] 1 kg FeCl 3 ·6H 2 O and 0.6 kg AlCl 3 ·6H 2O was added to 12 kg of water, stirred and dissolved to obtain a solution with a metal salt concentration of 0.52 mol / L, added with 10 kg of activated carbon, soaked at room temperature for 10 hours, filtered, dried at 110°C for 10 hours, and calcined at 400°C for 8 hours to obtain a metal-containing An acetylene hydrochlorination catalyst with 8% (mass content) of salt. Mix acetylene and tetrachloroethane gas and feed it into a fixed-bed catalyst reactor under the conditions of 200 °C and 0.1 MPa. The molar ratio of acetylene and tetrachloroethane gas is 1:1, and the space velocity of the reaction gas is 200 h. -1 , The conversion rate of acetylene is 54%, the selectivity of vinyl chloride is 97%, and the selectivity of trichlorethylene is 98%.
Embodiment 2
[0025] 1.5 kg FeCl 3 ·6H 2 O, 0.8 kg AlCl 3 ·6H 2 O and 0.5 kg TiCl 4 Add 12 kg of water, stir and dissolve to obtain a solution with a metal salt concentration of 0.82 mol / L, add 10 kg of activated carbon, soak at room temperature for 10 hours, filter, dry at 110°C for 10 hours, and roast at 450°C for 8 hours to obtain a metal salt 14% (mass content) of the acetylene hydrochlorination catalyst. Mix acetylene and tetrachloroethane gas and feed it into a fixed-bed catalyst reactor under the conditions of 220°C and 0.1MPa. The molar ratio of acetylene and tetrachloroethane gas is 1:1.05, and the space velocity of the reaction gas is 500 h -1 , The conversion rate of acetylene is 85%, the selectivity of vinyl chloride is 96%, and the selectivity of trichlorethylene is 99%.
Embodiment 3
[0027] 1.5 kg FeCl 3 ·6H 2 O, 0.8 kg AlCl 3 ·6H 2 O, 0.8 kg CaCl 2 2H 2 O, 0.5 kg SnCl 2 2H 2 O and 0.3 kg TiCl 4 Add 10 kg of water, stir and dissolve to obtain a solution with a metal salt concentration of 1.8 mol / L, add 10 kg of activated carbon, soak at room temperature for 10 hours, filter, dry at 110°C for 10 hours, and roast at 400°C for 8 hours to obtain a metal salt 21% (mass content) of the acetylene hydrochlorination catalyst. Mix acetylene and tetrachloroethane gas, 250 0 C. Under the condition of 0.5MPa, pass it into a fixed-bed catalyst reactor for reaction, the molar ratio of acetylene and tetrachloroethane gas mixture is 1:1.02, and the reaction gas space velocity is 100 h -1 , The conversion rate of acetylene is 81%, the selectivity of vinyl chloride is 97%, and the selectivity of trichlorethylene is 98%.
PUM
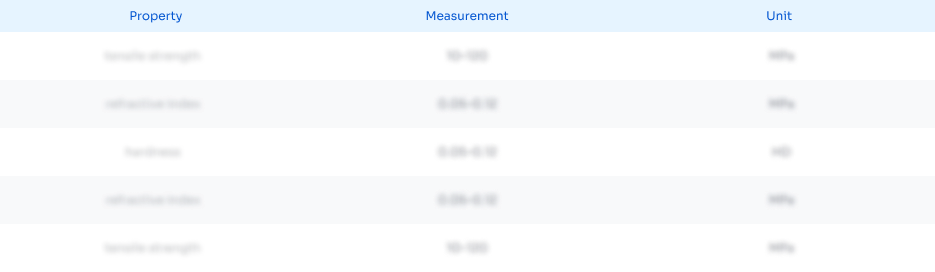
Abstract
Description
Claims
Application Information

- R&D
- Intellectual Property
- Life Sciences
- Materials
- Tech Scout
- Unparalleled Data Quality
- Higher Quality Content
- 60% Fewer Hallucinations
Browse by: Latest US Patents, China's latest patents, Technical Efficacy Thesaurus, Application Domain, Technology Topic, Popular Technical Reports.
© 2025 PatSnap. All rights reserved.Legal|Privacy policy|Modern Slavery Act Transparency Statement|Sitemap|About US| Contact US: help@patsnap.com