Processing method of arsenic-containing material
A processing method and material technology, applied in the field of copper smelting, can solve the problems affecting the quality of cathode copper in the electrolysis process, the adverse effect of electrolysis, and the increase of arsenic content, and achieve the effects of improving efficiency, improving reuse, and improving reaction speed.
- Summary
- Abstract
- Description
- Claims
- Application Information
AI Technical Summary
Problems solved by technology
Method used
Image
Examples
Embodiment 1
[0072] (1) Leaching process: the soot material containing about 8wt% of arsenic is fed through the feeding equipment, mixed with 2% NaOH aqueous solution according to the ratio of liquid to solid ratio of 2:1 to form a slurry, and sent into the leaching tank Carry out alkaline leaching, the leaching time is 30min, and then send it to the low-temperature heating oxidation leaching tank, add the oxidizing agent H 2 o 2 and catalyst magnetic MnO 2 , according to the arsenic-containing material and H 2 o 2 The mass ratio of 50: (1 ~ 2) ratio of adding H 2 o 2 Carry out oxidative leaching, leaching time is 50min, after leaching is finished, through magnetic separation operation, catalyst magnetic MnO 2 After separation, return to the low-temperature heating oxidation leaching tank, and the slurry after separation is sent to the solid-liquid separation process;
[0073] (2) Solid-liquid separation process: the slurry after the separation operation is concentrated by the 1# thi...
Embodiment 2
[0078] (1) Leaching process: the arsenic filter cake material containing about 4wt% arsenic is fed through the feeding equipment, mixed with 2% NaOH aqueous solution according to the ratio of liquid to solid ratio of 2:1 to form a slurry, and sent to the leaching Alkaline leaching is carried out in the tank, the leaching time is 30min, and then sent to the low-temperature heating oxidation leaching tank, and the oxidizing agent H is added 2 o 2 and catalyst magnetic MnO 2 , according to the arsenic-containing material and H 2 o 2 The mass ratio of 50:1.5 is added to H 2 o 2 Carry out oxidative leaching, leaching time is 50min, after leaching is finished, through magnetic separation operation, catalyst magnetic MnO 2 After separation, return to the low-temperature heating oxidation leaching tank, and the slurry after separation is sent to the solid-liquid separation process;
[0079] (2) Solid-liquid separation process: the slurry after the separation operation is concent...
PUM
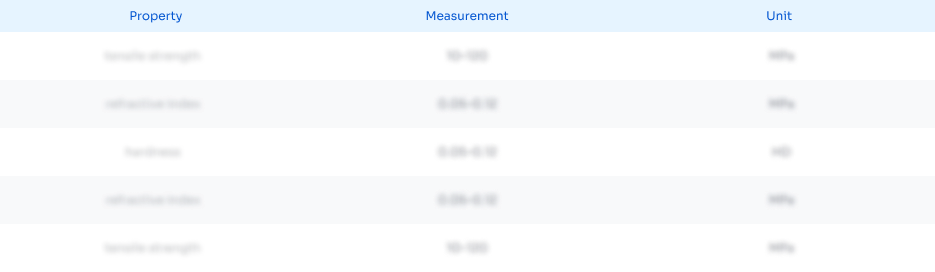
Abstract
Description
Claims
Application Information

- R&D
- Intellectual Property
- Life Sciences
- Materials
- Tech Scout
- Unparalleled Data Quality
- Higher Quality Content
- 60% Fewer Hallucinations
Browse by: Latest US Patents, China's latest patents, Technical Efficacy Thesaurus, Application Domain, Technology Topic, Popular Technical Reports.
© 2025 PatSnap. All rights reserved.Legal|Privacy policy|Modern Slavery Act Transparency Statement|Sitemap|About US| Contact US: help@patsnap.com