Waterborne Static Conductive Coating and Its Preparation
A technology for conducting static electricity and coatings, which is applied in the direction of conductive coatings, anti-fouling/underwater coatings, anti-corrosion coatings, etc. It can solve the problem that the anti-corrosion performance and static conductivity performance of coatings cannot be balanced, and the anti-corrosion performance and static conductivity cannot be obtained. Performance, high cost of solvent-based coatings and other issues, to achieve significant social and economic benefits, cost-effective, wide range of effects
- Summary
- Abstract
- Description
- Claims
- Application Information
AI Technical Summary
Problems solved by technology
Method used
Image
Examples
Embodiment 1
[0042] It is 0% to prepare carbon nanotube solid content, and conductive barium sulfate solid content is the water-based acrylate grafted epoxy resin anticorrosion antistatic coating of 20%, and each component is all in parts by mass:
[0043] 1) Weigh 271 parts of water and 1 part of fungicide (Hua Ke-981) to mix, and stir evenly at a speed of 600r / min;
[0044] 2) Add 6 parts of dispersant (BYK-154), 2 parts of wetting agent (PE-100), 2 parts of compatible stabilizer for latex paint (Hydropalat 306), hydroxyethyl cellulose to the mixture in step 1). (HBR-250) 0.5 parts, silicone defoamer (Defoamer 5845) 1.5 parts, alcohol ester twelve parts 14 parts, ethylene glycol 25 parts, stir at 600r / min for 15 minutes to form a uniform dispersion system;
[0045] 3) Add 96 parts of iron oxide red, 20 parts of mica powder, 32 parts of talcum powder, 29 parts of aluminum tripolyphosphate, 87 parts of zinc phosphate, 4.5 parts of ordinary barium sulfate, and 111.5 parts of conductive bari...
Embodiment 2
[0053] Prepare the carbon nanotube solid content as 0.1%, the water-based acrylate grafted epoxy resin anticorrosion and antistatic coating that the conductive barium sulfate solid content is 19.9%, and each component is all in parts by mass:
[0054] 1) Purification of carbon nanotubes: 0.557 parts of carbon nanotubes were purified with 5wt% HF and 5wt% HNO 3 Purification treatment to remove impurities in carbon nanotubes, followed by washing with deionized water to remove residual acid;
[0055] 2) Modification of carbon nanotubes: Add the carbon nanotubes obtained in step 1) to 271 parts of water containing 6 parts of dispersant (SN-5040) and perform high-speed shearing (2500 rpm) for 0.5 hours to form a uniform dispersion system;
[0056] 3) Mix the carbon nanotube dispersion obtained in step 2) with 1 part of fungicide (Huake-981), and stir evenly at a speed of 500 r / min;
[0057] 4) Add 2 parts of wetting agent (BYK-181), 2 parts of compatible stabilizer for latex pain...
Embodiment 3
[0065] It is 0.2% to prepare carbon nanotube solid content, and conductive barium sulfate solid content is 19.8% water-based acrylate grafted epoxy resin anticorrosion and antistatic coating, and each component is all in parts by mass:
[0066] 1) Purification of carbon nanotubes: 1.114 parts of carbon nanotubes were purified with 5wt% HF and 5wt% HNO 3 Purification treatment to remove impurities in carbon nanotubes, followed by washing with deionized water to remove residual acid;
[0067] 2) Modification of carbon nanotubes: Add the carbon nanotubes obtained in step 1) to 271 parts of water containing 6 parts of dispersant (740W) and perform high-speed shear (2500 rpm) for 0.5h to form a uniformly dispersed system ;
[0068] 3) Mix the carbon nanotube dispersion obtained in step 2) with 1 part of bactericide, and stir evenly at a speed of 600 r / min;
[0069] 4) Add 2 parts of wetting agent (CF-10), 2 parts of compatible stabilizer for latex paint (Hydropalat 306), 0.5 part...
PUM
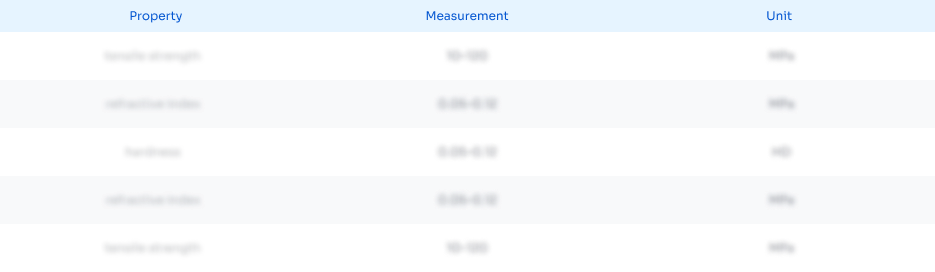
Abstract
Description
Claims
Application Information

- Generate Ideas
- Intellectual Property
- Life Sciences
- Materials
- Tech Scout
- Unparalleled Data Quality
- Higher Quality Content
- 60% Fewer Hallucinations
Browse by: Latest US Patents, China's latest patents, Technical Efficacy Thesaurus, Application Domain, Technology Topic, Popular Technical Reports.
© 2025 PatSnap. All rights reserved.Legal|Privacy policy|Modern Slavery Act Transparency Statement|Sitemap|About US| Contact US: help@patsnap.com