Heat treatment method
A heat treatment method and slab technology, applied in the field of heat treatment, to achieve the effect of excellent surface quality and elimination of internal stress
- Summary
- Abstract
- Description
- Claims
- Application Information
AI Technical Summary
Problems solved by technology
Method used
Examples
Embodiment 1
[0036] What the heat treatment of present embodiment is medium-high carbon steel slab, its chemical composition mass percent is:
[0037] C: 1.10%; Si: 0.30%; Mn: 0.40%; P: 0.025%; S: 0.021%;
[0038] The balance is Fe and unavoidable impurity elements.
[0039] The slab is 11000mm long, 1250mm wide and 230mm thick.
[0040] The heat treatment process of the present embodiment is:
[0041] The temperature before the slab enters the heat treatment furnace: 600°C;
[0042] Slab heat treatment holding temperature: 740°C;
[0043] Slab heat treatment holding time: 6 hours;
[0044] Slab heat treatment temperature before leaving the furnace: 250°C;
[0045] Slab heat treatment heating rate: 30°C / h;
[0046] Slab heat treatment cooling rate: 40°C / h.
Embodiment 2
[0048] What the heat treatment of present embodiment is medium-high carbon steel slab, its chemical composition mass percent is:
[0049] C: 0.85%; Si: 0.30%; Mn: 0.37%; P: 0.018%; S: 0.012%;
[0050] The balance is Fe and unavoidable impurity elements.
[0051] The slab is 11000mm long, 1250mm wide and 200mm thick.
[0052] The heat treatment process of the present embodiment is:
[0053] The temperature before the slab enters the heat treatment furnace: 550°C;
[0054] Slab heat treatment temperature: 720°C;
[0055] Slab heat treatment holding time: 8 hours;
[0056] Slab heat treatment temperature before leaving the furnace: 300°C;
[0057] Slab heat treatment heating rate: 40°C / h;
[0058] Slab heat treatment cooling rate: 60°C / h.
Embodiment 3
[0060] What the heat treatment of present embodiment is medium-high carbon steel slab, its chemical composition mass percent is:
[0061] C: 0.65%; Si: 0.22%; Mn: 0.35%; P: 0.017%; S: 0.013%;
[0062] The balance is Fe and unavoidable impurity elements.
[0063] The slab is 11000mm long, 1450mm wide and 230mm thick.
[0064] The heat treatment process of the present embodiment is:
[0065] The temperature before the slab enters the heat treatment furnace: 300°C;
[0066] Slab heat treatment temperature: 500°C;
[0067] Slab heat treatment holding time: 30 hours;
[0068] Slab heat treatment temperature before leaving the furnace: 200°C;
[0069] Slab heat treatment heating rate: 80°C / h;
[0070] Slab heat treatment cooling rate: 90°C / h.
[0071] Carbon steel embodiment four
[0072] What the heat treatment of present embodiment is medium-high carbon steel slab, its chemical composition mass percent is:
[0073] C: 0.50%; Si: 0.32%; Mn: 0.70%; P: 0.016%; S: 0.014%;
...
PUM
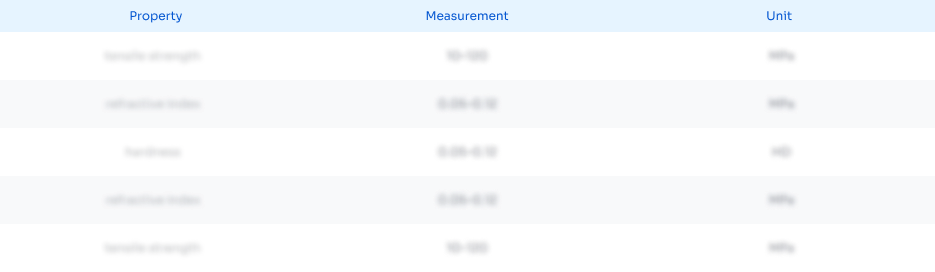
Abstract
Description
Claims
Application Information

- R&D Engineer
- R&D Manager
- IP Professional
- Industry Leading Data Capabilities
- Powerful AI technology
- Patent DNA Extraction
Browse by: Latest US Patents, China's latest patents, Technical Efficacy Thesaurus, Application Domain, Technology Topic, Popular Technical Reports.
© 2024 PatSnap. All rights reserved.Legal|Privacy policy|Modern Slavery Act Transparency Statement|Sitemap|About US| Contact US: help@patsnap.com