Technology of welding and repair for defects of E grade steel coupler and coupler yoke
A coupler frame and welding repair technology, which is applied in the field of welding and repairing defects of E-grade steel couplers and coupler frames, can solve problems such as cracks and inability to guarantee welding quality, and achieve simple process, good welding quality and no cracks The effect of defects
- Summary
- Abstract
- Description
- Claims
- Application Information
AI Technical Summary
Problems solved by technology
Method used
Examples
Embodiment Construction
[0011] Taking the welding repair of 17 E-grade steel hook bodies, 20 E-grade steel knuckles, and 10 E-grade steel tail frames as an example, the above-mentioned parts are heated in an electric furnace as a whole before welding and repairing. ℃, and keep the above temperature for 0.5-1.5 hours, then hang out the electric furnace for welding repair treatment, the welding rods used, the specifications of the welding rods and the treatment of the welding rods can be the same as the existing technology. Slowly cool the furnace to ≤150°C and then take it out of the furnace.
[0012] Using this process, 17 E-grade steel hook bodies, 20 E-grade steel knuckles, and 10 E-grade steel tail frames are welded and repaired, and the welding repair points are photographed and recorded, so as to accurately define the heat treatment after welding. point of impact. At the same time, the welded repair point was ground, and the wet magnetic particle inspection was carried out. After the flaw detec...
PUM
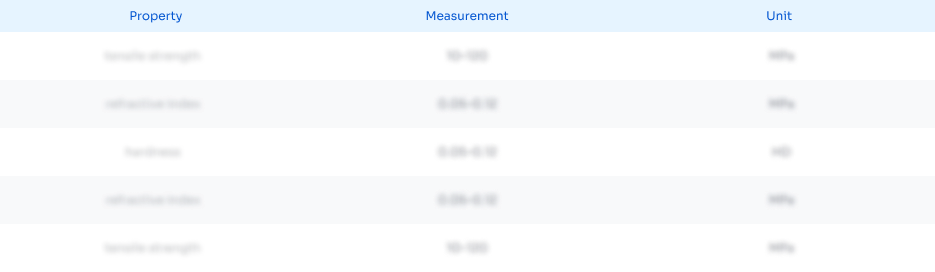
Abstract
Description
Claims
Application Information

- R&D
- Intellectual Property
- Life Sciences
- Materials
- Tech Scout
- Unparalleled Data Quality
- Higher Quality Content
- 60% Fewer Hallucinations
Browse by: Latest US Patents, China's latest patents, Technical Efficacy Thesaurus, Application Domain, Technology Topic, Popular Technical Reports.
© 2025 PatSnap. All rights reserved.Legal|Privacy policy|Modern Slavery Act Transparency Statement|Sitemap|About US| Contact US: help@patsnap.com