Die casting method for casting 80 t-grade large forged ingots through bottom casting method
A die-casting, large-scale technology, applied in the field of metallurgy, can solve the problems of difficult control of injection speed, easy cracks, poor surface quality, etc., and achieve the effects of easy operation, surface crack prevention, and good surface quality
- Summary
- Abstract
- Description
- Claims
- Application Information
AI Technical Summary
Problems solved by technology
Method used
Examples
Embodiment 1
[0017] In this embodiment, the 80t-grade 42CrMo steel ingot is mold-cast, and the pouring method is used, including the superheat of molten steel pouring, the pouring time of the steel ingot body, the pouring time of the cap mouth of the steel ingot, the demoulding after pouring, and the slow cooling control of the stacked red ladle. The process steps are as follows:
[0018] During the mold casting process, the pouring superheat of molten steel is 36°C, the pouring time for the ingot body is 20 minutes, the pouring time for the cap mouth of the ingot is 8 minutes, and the pouring nozzle aperture is 45mm;
[0019] After 24 hours of pouring, the surface temperature of the steel ingot dropped to 550°C and the demoulding took place. After the demoulding, the steel ladles were stacked and cooled slowly for 6 days until the surface temperature dropped to 170°C. 99.15%, no cracks on the surface, good surface quality.
Embodiment 2
[0021] In this embodiment, the 80t-grade Q235D steel ingot is die-cast, and poured by the down-casting method, including the superheat of molten steel pouring, the pouring time of the steel ingot body, the pouring time of the cap mouth of the steel ingot, the demoulding after pouring, and the slow cooling control of the stacked red ladle. The process steps are as follows:
[0022] During the mold casting process, the pouring superheat of molten steel is 34°C, the pouring time for the ingot body is 22 minutes, the pouring time for the cap mouth of the ingot is 9 minutes, and the pouring nozzle aperture is 45mm;
[0023] After 27 hours of pouring, the surface temperature of the steel ingot dropped to 600°C and the demoulding took place. After the demoulding, the buckle red steel ladles were stacked and cooled slowly for 6 days until the surface temperature dropped to 190°C. 99.35%, no cracks on the surface, good surface quality.
Embodiment 3
[0025] In this embodiment, the 35# steel ingot of 80t level is mold-cast, which is poured by the pouring method, including the superheat of molten steel pouring, the pouring time of the ingot body, the pouring time of the cap mouth of the steel ingot, the demoulding after pouring, and the slow cooling control of the red ladle stacking. Concrete process steps are as follows:
[0026] During the mold casting process, the pouring superheat of molten steel is 32°C, the pouring time for the ingot body is 24 minutes, the pouring time for the cap mouth of the ingot is 8 minutes, and the pouring nozzle aperture is 45mm;
[0027] After 26 hours of pouring, the surface temperature of the steel ingot dropped to 580°C and the mold was removed. After the demoulding, the buckle red steel ladle was stacked and cooled slowly for 7 days until the surface temperature dropped to 160°C. 99.42%, no cracks on the surface, good surface quality.
PUM
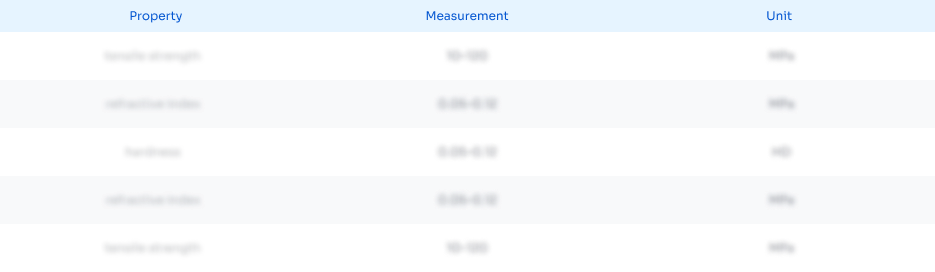
Abstract
Description
Claims
Application Information

- R&D
- Intellectual Property
- Life Sciences
- Materials
- Tech Scout
- Unparalleled Data Quality
- Higher Quality Content
- 60% Fewer Hallucinations
Browse by: Latest US Patents, China's latest patents, Technical Efficacy Thesaurus, Application Domain, Technology Topic, Popular Technical Reports.
© 2025 PatSnap. All rights reserved.Legal|Privacy policy|Modern Slavery Act Transparency Statement|Sitemap|About US| Contact US: help@patsnap.com