Making method of artificial red coral bead string
A coral and artificial technology, applied in the field of preparation of red coral beads, can solve the problems of complicated preparation process, high cost, and slag drop, and achieve the effects of simple preparation process, long service life and short production cycle
- Summary
- Abstract
- Description
- Claims
- Application Information
AI Technical Summary
Problems solved by technology
Method used
Image
Examples
Embodiment 1
[0028] 10mM CaCl 2 1000L and 1M MgCl 2 40L was poured into the reactor, then 208g of polyacrylic acid with a molecular weight of 20k was added, the reactor was covered and reacted at room temperature for 3 days, then centrifugally dried to obtain pure high-magnesium calcite powder. Weigh again 15g of strontium carbonate powder and 1260g of the high-magnesium calcite powder prepared above are added to 40L of industrial water together, 60g of FeCl 2 Dissolve in 20L of industrial water, mechanically stir for 1 hour respectively, then mix and stir the above two solutions for 2 hours, add 100ml of ammonia water, mix and sonicate for 20 minutes, pour into a 100L autoclave and react at 200°C for 12 hours, then centrifuge and dry. Get Red Coral Powder (eg figure 1 shown); Stir 150g of unsaturated polyester crystal resin, 1350g of the above-mentioned red coral powder, 12g of cyclohexanone peroxide and 12g of cobalt naphthenate at a stirring speed of 500r / min for 4h; pour the mixed ...
Embodiment 2
[0030] 10mM CaCl 2 1000L and 1M MgCl 2 50L was poured into the reactor, then 144g of polyaspartic acid with a molecular weight of 13.7k was added, the reactor was covered and reacted at room temperature for 3 days, and then centrifuged and dried to obtain pure high-magnesium calcite powder. Then weigh 22.5g of strontium carbonate powder and 555g of the above-mentioned high-magnesium calcite powder and add them to 40L of industrial water, 60g of FeCl 2 Dissolve in 20L of industrial water, mechanically stir for 1 hour, then mix and stir the two solutions for 3 hours, add 100ml of ammonia water, mix and sonicate for 20 minutes, pour into a 100L autoclave and react at 180°C for 18 hours, then centrifuge and dry. Get Red Coral Powder (eg figure 2 shown); Stir 97.5g of unsaturated polyester crystal resin, 652.5g of the above-mentioned red coral powder, 4.5g of cyclohexanone peroxide and 4.5g of cobalt naphthenate at a stirring speed of 800r / min for 5h; The slurry is poured int...
Embodiment 3
[0032] 10mM CaCl 2 1000L and 1M MgCl 2 50L was poured into the reactor, then 210g of polyacrylic acid with a molecular weight of 20k was added, the reactor was covered and reacted at room temperature for 4 days, then centrifugally dried to obtain pure high-magnesium calcite powder. Weigh again 18.75g of strontium carbonate powder and 225g of the above-prepared high-magnesium calcite powder are added to 40L of industrial water, 60g of FeCl 2 Dissolve in 20L of industrial water, mechanically stir for 2 hours respectively, then mix and stir the two solutions for 4 hours, add 100ml of ammonia water, mix and sonicate for 20 minutes, pour into a 100L autoclave and react at 200°C for 24 hours, and then centrifuge and dry to obtain red Coral powder; Stir 56.25g of unsaturated polyester crystal resin, 318.75g of red coral powder, 2.6g of cyclohexanone peroxide and 2.6g of cobalt naphthenate at a stirring speed of 1000r / min for 6h; put the mixed slurry Pour into bead-shaped fibergla...
PUM
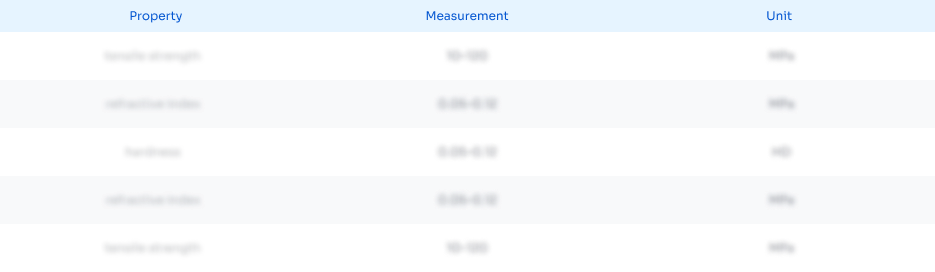
Abstract
Description
Claims
Application Information

- R&D Engineer
- R&D Manager
- IP Professional
- Industry Leading Data Capabilities
- Powerful AI technology
- Patent DNA Extraction
Browse by: Latest US Patents, China's latest patents, Technical Efficacy Thesaurus, Application Domain, Technology Topic, Popular Technical Reports.
© 2024 PatSnap. All rights reserved.Legal|Privacy policy|Modern Slavery Act Transparency Statement|Sitemap|About US| Contact US: help@patsnap.com