Smoke purification technology implemented based on adsorbent pretreatment
A flue gas purification process and absorbent technology, applied in chemical instruments and methods, dispersed particle separation, separation methods, etc., can solve the problems of unobvious industrial application, long process flow, poor technical economy, etc., and improve desulfurization and denitrification efficiency , Improve processing efficiency, high crushing efficiency
- Summary
- Abstract
- Description
- Claims
- Application Information
AI Technical Summary
Problems solved by technology
Method used
Image
Examples
Embodiment 1
[0037] In the traditional flue gas purification method, the rough purification process of the raw flue gas by the absorbent usually includes: metering the absorbent, and then sending it into the pulverizer system for pulverization, and then sending the pulverized absorbent particles through a dry powder injector. The main flue 1 mixes and reacts with the raw flue gas. During this process, the purification efficiency of the absorbent to the raw flue gas is usually about 50%, and the desulfurization efficiency is low. Therefore, in order to improve the working efficiency of the absorbent, this The invention proposes a flue gas purification process based on absorbent pretreatment. The flue gas purification process includes sending the original flue gas in the main flue into SO through the flue gas system. 2 Absorption system, in order to overcome the above defects, the present invention improves the flue gas system. In the present invention, the flue gas system is mainly composed ...
Embodiment 2
[0039] The difference between this embodiment and Embodiment 1 is that in this embodiment, after the original flue gas is split, the volume ratio of the auxiliary flue gas passing through the auxiliary flue 2 and the flue gas passing through the main flue 1 is 9: 1.
[0040] In the actual application process of this embodiment, the original flue gas is sent into the main flue 1 through the flue gas booster fan, and a part of the original flue gas enters the auxiliary flue 2 through the entrance of the auxiliary flue 2, which is called auxiliary flue gas. A part of the original flue gas remains in the main flue 1, which is called flue gas. The auxiliary flue gas drives the absorbent and enters the impact mill crushing classifier together. The absorbent is pretreated in the impact mill crushing classifier and combined with the auxiliary flue gas. reaction, the obtained gas-powder mixture is sent to the main flue 1 through the outlet of the flue, and then mixed with the flue gas ...
Embodiment 3
[0042] The difference between this embodiment and Embodiment 2 is that in this embodiment, the impact mill pulverizing classifier is mainly composed of a pulverizer, a classifier and a high-pressure induced draft fan, and the absorbent and auxiliary flue gas are sent into the mill with the high-pressure induced draft fan. The absorbent is pulverized and then sent to the classifier with the auxiliary flue gas for screening. In the actual operation process, the gas-powder mixture can be selected by adjusting the speed of the classifier. Usually, the particle size of the absorbent in the gas-powder mixture It is controlled at 10-40um, that is, the absorbent with a particle size of ≤40um is mixed with auxiliary flue gas to obtain a gas-powder mixture, and the absorbent with a particle size>40um is returned to the mill for further pulverization.
[0043] Since the amount of absorbent introduced is related to the pollutant content in the original flue gas, it is necessary to monitor ...
PUM
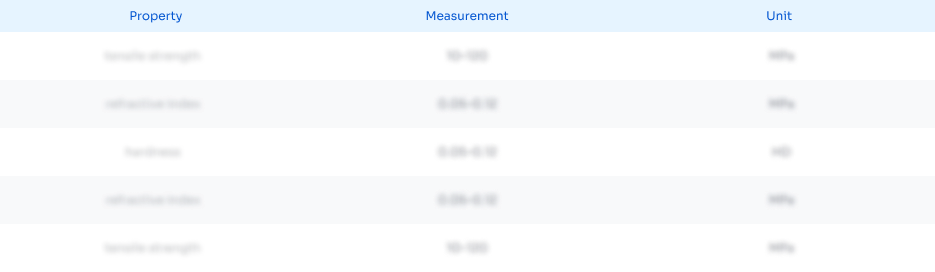
Abstract
Description
Claims
Application Information

- R&D
- Intellectual Property
- Life Sciences
- Materials
- Tech Scout
- Unparalleled Data Quality
- Higher Quality Content
- 60% Fewer Hallucinations
Browse by: Latest US Patents, China's latest patents, Technical Efficacy Thesaurus, Application Domain, Technology Topic, Popular Technical Reports.
© 2025 PatSnap. All rights reserved.Legal|Privacy policy|Modern Slavery Act Transparency Statement|Sitemap|About US| Contact US: help@patsnap.com