Device for moving small insulating plate at bottom of polycrystalline silicon ingot furnace and polycrystalline silicon ingot furnace
A polysilicon ingot casting furnace and movable device technology, which is applied in post-processing devices, polycrystalline material growth, crystal growth, etc., can solve the problems of reduced solidification speed of ingots, increased cost of silicon wafers, diffusion pollution, etc., and achieves improved cooling and crystallization Speed, shorten production cycle, reduce the effect of production cost
- Summary
- Abstract
- Description
- Claims
- Application Information
AI Technical Summary
Problems solved by technology
Method used
Image
Examples
Embodiment 1
[0037]The present embodiment comprises bottom small insulation board 2, support rod 3, telescopic tube 6, lifting device 7; The bottom small insulation board 2 is fixed on the top of support rod 3 with upper nut 4 and lower nut 16; Stretch to telescopic tube 6 bottoms; Telescopic tube 6 upper ends link to each other with body of heater, telescopic tube 6 lower ends are connected with elevating device 7; (Such as figure 1 shown);
[0038] Elevating device 7 is made up of elevating rod 8 and servo motor 9, and elevating rod 8 can move up and down along servo motor 9, thereby drives the bottom small insulation board 2 of support rod 3 tops to move up and down.
[0039] The telescopic tube 6 is sealed and welded by the bellows 13 and the quick-change joint 14; the upper end of the telescopic tube 6 is connected to the furnace body with a sealing ring 10, which can be sealed and fixed with a clamp 11; the lower end of the telescopic tube 6 is connected to the blind plate 12 A sea...
Embodiment 2
[0049] The difference between this embodiment and Embodiment 1 is only that: the support rod 3 is a tungsten rod; Figure 8 As shown), the cross-section of the bottom large insulation board 1 corresponding to the matching hole is circular; when the melting is completed and enters the crystal growth stage, start the lifting device 7 to separate the bottom small insulation board 2 from the bottom large insulation board 1, and the separation distance is 15 is 60mm. The rest are the same as embodiment 1.
[0050] Taking GT polysilicon ingot furnace G5 transformed into G6 as an example, the weight of the ingot is increased from 500 kg to 800 kg. If the crystal growth plan of lifting the heat insulation cage is simply adopted, the crystal growth time will take about 40 hours, and the total The process time is 75 hours; and after adopting the movable device of the small insulating plate at the bottom of the polysilicon ingot furnace of the present invention, the crystal growth time ...
Embodiment 3
[0052] The difference between this embodiment and Embodiment 1 is that: the support rod 3 is an iridium rod; the upper nut 4, the lower nut 16 and the backing plate 5 are made of carbon-carbon composite material; the lifting device 7 is replaced by a C-shaped card 20, when When melting completes and enters the crystal growth stage, use the C-shaped card 20 to separate the small insulation board 2 at the bottom from the large insulation board 1 at the bottom, and the separation distance 15 is 100mm (such as Figure 5 , Figure 6 shown). The rest are the same as embodiment 1.
[0053] Taking JYT polysilicon ingot furnace G5 transformed into G7 as an example, the weight of the ingot is increased from 500 kg to 1200 kg. If the crystal growth plan is simply adopted by the heat insulation cage, the crystal growth time will take about 52 hours, and the total The process time is 90 hours; and after adopting the movable device of the small insulating plate at the bottom of the polysi...
PUM
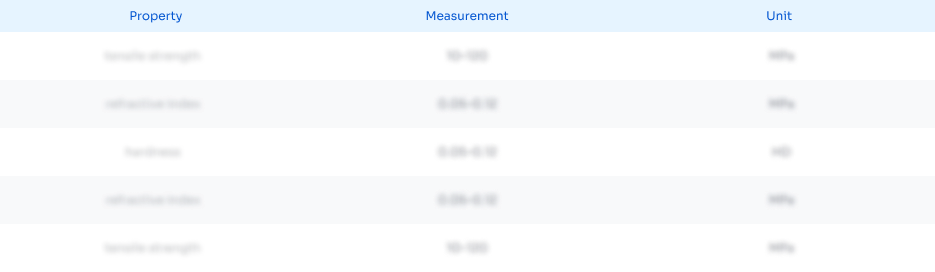
Abstract
Description
Claims
Application Information

- R&D
- Intellectual Property
- Life Sciences
- Materials
- Tech Scout
- Unparalleled Data Quality
- Higher Quality Content
- 60% Fewer Hallucinations
Browse by: Latest US Patents, China's latest patents, Technical Efficacy Thesaurus, Application Domain, Technology Topic, Popular Technical Reports.
© 2025 PatSnap. All rights reserved.Legal|Privacy policy|Modern Slavery Act Transparency Statement|Sitemap|About US| Contact US: help@patsnap.com