Dephosphorizing agent and application thereof
A dephosphorization agent and a form of technology, applied in the field of dephosphorization agents, can solve the problems of affecting the hardenability of steel and containing fluorite, and achieve the effects of increasing activity, reducing the amount of slag, and being environmentally friendly
- Summary
- Abstract
- Description
- Claims
- Application Information
AI Technical Summary
Problems solved by technology
Method used
Image
Examples
Embodiment 1
[0054] Dephosphorizer components (percentage is mass percentage):
[0055] Fe 2 O 3 :33, CaO: 38, SiO 2 :20, Na 2 O:3, Al 2 O 3 :6
[0056] The dephosphorization experiment was carried out in a high-temperature resistance furnace. The weight of the carbon-saturated molten iron sample was 300g, the composition of the molten iron [P] = 0.518%, [Si] ≤ 0.10wt% 0.1wt%; the controlled dephosphorization temperature was 1350℃, at this temperature Next, 30 g of the prepared dephosphorization agent was added to the molten iron in the upper part, and stirred with a molybdenum rod. After 30 minutes of dephosphorization, the molten iron [P] dropped to 0.076%, and the dephosphorization rate was 85.34%.
[0057] The dephosphorization final slag of Example 1 was subjected to water quenching treatment. After drying and grinding, XRD powder diffraction analysis was performed. The analysis results showed that there were only two phases in the dephosphorization final slag, one of which contained sodium...
Embodiment 2
[0061] Dephosphorizer components (percentage is mass percentage):
[0062] Fe 2 O 3 : 25, CaO: 45, SiO 2 :17, Na 2 O:10, Al 2 O 3 :3
[0063] The dephosphorization experiment was carried out in a high-temperature resistance furnace. The weight of the carbon-saturated molten iron sample was 300g, the molten iron content [P]=0.765%, [Si]≤0.10wt%; the dephosphorization temperature was controlled to 1350℃, and the above method of input would be 30 g of the dephosphorization agent prepared above was added to the molten iron and stirred with a molybdenum rod. After 30 minutes of dephosphorization, the molten iron [P] dropped to 0.113%, and the dephosphorization rate was 85.25%.
Embodiment 3
[0065] Dephosphorizer components (percentage is mass percentage):
[0066] Fe 2 O 3 :28, CaO: 32, SiO 2 :30, Na 2 O:3, Al 2 O 3 :7
[0067] The dephosphorization experiment was carried out in a high-temperature resistance furnace. The weight of the carbon-saturated molten iron sample was 300g, the molten iron content [P] = 0.518%, [Si] ≤ 0.10wt%; the dephosphorization temperature was controlled at 1400 ℃, and the above method of input would be 30 g of the dephosphorization agent prepared above was added to the molten iron and stirred with a molybdenum rod. After 30 minutes of dephosphorization, the molten iron [P] dropped to 0.084%, and the dephosphorization rate was 83.72%.
PUM
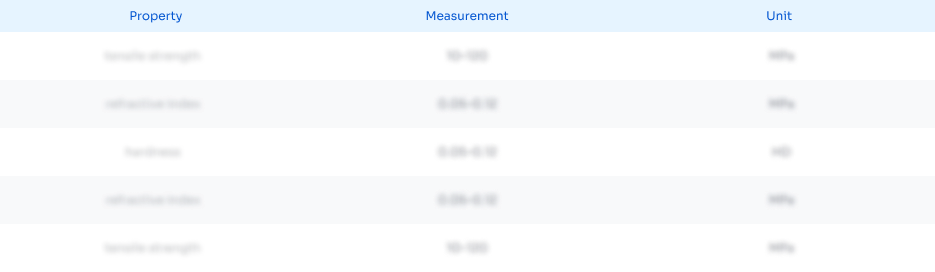
Abstract
Description
Claims
Application Information

- R&D
- Intellectual Property
- Life Sciences
- Materials
- Tech Scout
- Unparalleled Data Quality
- Higher Quality Content
- 60% Fewer Hallucinations
Browse by: Latest US Patents, China's latest patents, Technical Efficacy Thesaurus, Application Domain, Technology Topic, Popular Technical Reports.
© 2025 PatSnap. All rights reserved.Legal|Privacy policy|Modern Slavery Act Transparency Statement|Sitemap|About US| Contact US: help@patsnap.com