A kind of preparation method of liquid organosilicon polymer for high temperature resistant adhesive
A binder and silicone technology, applied in the direction of adhesives, etc., can solve the problems of lowering the use temperature, molecular structure change, low bonding strength, etc., and achieve the effect of reliable source, low surface energy, and good bonding performance
- Summary
- Abstract
- Description
- Claims
- Application Information
AI Technical Summary
Problems solved by technology
Method used
Image
Examples
Embodiment 1
[0025] Add 46g (2mol) of sodium metal and toluene solvent into a three-necked flask equipped with condensing reflux device and mechanical stirring device, heating to 100℃ under the protection of inert atmosphere, and then adding 115g (1mol) methyldichlorosilane (CH 3 SiHCl 2 ), after the dripping is completed, keep it at 100°C for 6 hours, filter and distill off the organic solvent to obtain liquid polysilane;
[0026] Mix liquid polysilane with 2,4,6,8-tetramethyl-2,4,6,8-tetravinylcyclotetrasiloxane at a mass ratio of 1:1, and under the protection of nitrogen, The temperature of the reaction system was raised to 180°C at a temperature rising rate of 3°C / min, mechanically stirred, and kept for 1 hour to obtain a liquid silicone polymer.
[0027] Reference figure 1 , figure 2 : By IR, 1 H-NMR analysis shows that the silicone polymer contains Si-H and Si-CH 3 , Si-O-Si, CH=CH 2 And other chemical bonds, the polymer has excellent high temperature resistance, N 2 At 1200℃, the weight ...
Embodiment 2
[0029] Add 69g (3mol) of sodium metal and toluene solvent into a three-necked flask equipped with condensing reflux device and mechanical stirring device, heat to 90°C under the protection of an inert atmosphere, and then add 115g (1mol) methyldichlorosilane (CH 3 SiHCl 2 ) And 70.5g (0.5mol) CH 3 (CH 2 =CH)SiCl 2 After the dripping is completed, keep it at 90°C for 8h, filter and distill off the organic solvent to obtain liquid polysilane;
[0030] Mix liquid polysilane with 2,4,6,8-tetramethyl-2,4,6,8-tetravinylcyclotetrasiloxane at a mass ratio of 2:1, and under the protection of nitrogen, The temperature of the reaction system was raised to 120°C at a heating rate of 2°C / min, mechanically stirred, and kept for 4 hours to obtain a liquid silicone polymer.
[0031] Polymer N obtained in this example 2 The weight loss at 1200°C under the atmosphere is 17.4%, and the weight loss at 1200°C under the air atmosphere is 14.5%.
Embodiment 3
[0033] Add 69g (3mol) of sodium metal and toluene solvent to a three-necked flask equipped with condensing reflux device and mechanical stirring device, and heat to 90°C under the protection of an inert atmosphere, and then add 57.5g (0.5mol) methyldichlorosilane ( CH 3 SiHCl 2 ) And 70.5g (0.5mol) CH 3 (CH 2 =CH)SiCl 2 After the dropping, keep it at 90°C for 6h, filter and distill off the organic solvent to obtain liquid polysilane;
[0034] Mix liquid polysilane and tetramethyldivinyldisilazane in a mass ratio of 1:2. Under the protection of nitrogen, the temperature of the reaction system is raised to 180°C at a heating rate of 1°C / min, and mechanically stirred , After being kept for 4h, a liquid silicone polymer is obtained.
[0035] Polymer N obtained in this example 2 The weight loss at 1200℃ under the atmosphere is 22.4%, and the weight loss at 1200℃ under the air atmosphere is 25.5%.
[0036] Use the product obtained in Example 1 to bond the normal pressure sintered silicon ...
PUM
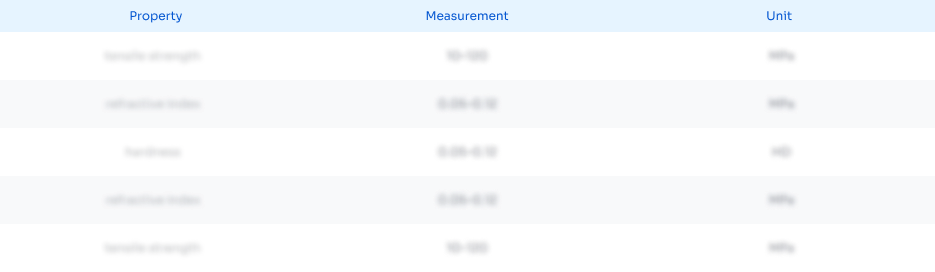
Abstract
Description
Claims
Application Information

- R&D Engineer
- R&D Manager
- IP Professional
- Industry Leading Data Capabilities
- Powerful AI technology
- Patent DNA Extraction
Browse by: Latest US Patents, China's latest patents, Technical Efficacy Thesaurus, Application Domain, Technology Topic, Popular Technical Reports.
© 2024 PatSnap. All rights reserved.Legal|Privacy policy|Modern Slavery Act Transparency Statement|Sitemap|About US| Contact US: help@patsnap.com