Protein plastic material
A plastic material and protein technology, applied in the field of plastics, can solve the problems of large consumption of agricultural products, low tensile strength, high brittleness, etc., to improve ductility, improve tensile performance and impact resistance, and improve wear resistance The effect of tear properties
- Summary
- Abstract
- Description
- Claims
- Application Information
AI Technical Summary
Problems solved by technology
Method used
Examples
Embodiment 1
[0012] A kind of protein plastic material that the present invention proposes, its raw material comprises by weight: polybutylene succinate PBS 50 parts, poly-β-hydroxybutyric acid PHB 30 parts, peanut protein powder 25 parts, potassium titanate 2.5 parts of fiber, 7 parts of silk fiber, 1.2 parts of silane coupling agent KH570, 3 parts of sodium sorbate, 1.1 parts of ethyl p-hydroxybenzoate, 1.9 parts of diisooctyl phthalate DIOP, 3 parts of epoxy soybean oil Parts, 5 parts of acetate starch, 15 parts of talcum powder, 11 parts of wollastonite powder, 5 parts of calcite powder, 1.4 parts of tert-butyl hydroquinone TBHQ;
[0013] During the preparation process, the silane coupling agent KH570 was added to the potassium titanate fiber and stirred at a stirring speed of 27rpm for 8min, then silk fiber was added and stirred at a stirring speed of 30rpm for 8min, then peanut protein powder was added and stirred at a stirring speed of 38rpm for 6min , then add polybutylene succinat...
Embodiment 2
[0015] A kind of protein plastic material that the present invention proposes, its raw material comprises by weight: polybutylene succinate PBS 45 parts, poly-β-hydroxybutyric acid PHB 35 parts, peanut protein powder 20 parts, potassium titanate fiber 3 parts, 5 parts of silk fiber, 1.7 parts of silane coupling agent KH570, 2 parts of sodium sorbate, 1.6 parts of ethyl p-hydroxybenzoate, 1.7 parts of diisooctyl phthalate DIOP, 6 parts of epoxy soybean oil , 3 parts of acetate starch, 18 parts of talcum powder, 7 parts of wollastonite powder, 9 parts of calcite powder, 1 part of tert-butyl hydroquinone TBHQ;
[0016] During the preparation process, the silane coupling agent KH570 was added to the potassium titanate fiber and stirred at a stirring speed of 24rpm for 9min, then silk fiber was added and stirred at a stirring speed of 25rpm for 11min, then peanut protein powder was added and stirred at a stirring speed of 37rpm for 7min , then add polybutylene succinate PBS, poly-β...
Embodiment 3
[0018] A kind of protein plastic material that the present invention proposes, its raw material comprises by weight: polybutylene succinate PBS part, poly-beta-hydroxybutyric acid PHB 31 parts, peanut protein powder 24 parts, potassium titanate fiber 2.7 parts 6.5 parts of silk fiber, 1.3 parts of silane coupling agent KH570, 2.7 parts of sodium sorbate, 1.2 parts of ethyl p-hydroxybenzoate, 1.82 parts of diisooctyl phthalate DIOP, 3.4 parts of epoxy soybean oil, 4.5 parts of acetate starch, 16 parts of talc powder, 10 parts of wollastonite powder, 6 parts of calcite powder, 1.3 parts of tert-butyl hydroquinone TBHQ.
[0019] During the preparation process, the silane coupling agent KH570 was added to the potassium titanate fiber and stirred at a stirring speed of 30rpm for 5min, then silk fiber was added and stirred at a stirring speed of 32rpm for 7min, then peanut protein powder was added and stirred at a stirring speed of 40rpm for 5min , then add polybutylene succinate PB...
PUM
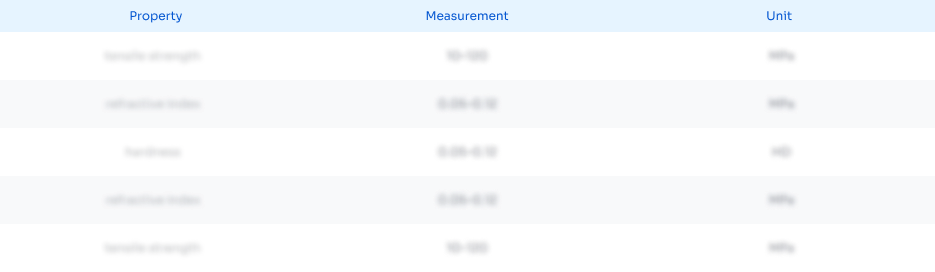
Abstract
Description
Claims
Application Information

- Generate Ideas
- Intellectual Property
- Life Sciences
- Materials
- Tech Scout
- Unparalleled Data Quality
- Higher Quality Content
- 60% Fewer Hallucinations
Browse by: Latest US Patents, China's latest patents, Technical Efficacy Thesaurus, Application Domain, Technology Topic, Popular Technical Reports.
© 2025 PatSnap. All rights reserved.Legal|Privacy policy|Modern Slavery Act Transparency Statement|Sitemap|About US| Contact US: help@patsnap.com