Method for obtaining liquid paraffin, gasoline and diesel oil via extraction of shale oil
A technology for liquid paraffin and shale oil, which is applied in the petroleum industry, hydrocarbon oil treatment, hydrotreating process, etc., can solve the problems of shale oil dewaxing, high energy consumption, deactivation, etc. that are not considered, and achieve good economic benefits and industrial application prospects, improve economic benefits, and increase the effect of added value
- Summary
- Abstract
- Description
- Claims
- Application Information
AI Technical Summary
Problems solved by technology
Method used
Image
Examples
Embodiment 1
[0021] Shale oil is cut into distillate oil and residual oil below 420°C by vacuum distillation. The residual oil is injected into the catalytic distillation tower, and the temperature of the kettle is controlled at 450°C. The distilled oil and gas are contacted with molecular sieve / alumina catalyst for reaction and rectification. Catalytic distillation slip-off oil is mixed with distillate oil lower than 420°C through the raw material pump, mixed with hydrogen, and then heated by a heat exchanger into the hydrodewaxing reactor. The feed temperature is controlled at 380°C; hydrogen partial pressure is 8MPa, and the volume is empty Speed 1.0h -1 The volume ratio to hydrogen oil is 800:1. The distillate after hydrofining is distilled under normal pressure and cut into gasoline (150°C, 220°C) according to the distillation temperature.
[0022] The yields and properties of liquid paraffin and gasoline and diesel obtained in this embodiment are shown in Table 1, Table 2 and Ta...
Embodiment 2
[0030] Shale oil is cut into distillate oil and residual oil below 420°C by vacuum distillation. The residual oil is injected into the catalytic distillation tower, and the temperature of the kettle is controlled at 480°C. The distilled oil and gas are contacted with molecular sieve / alumina catalyst for reaction and rectification. Catalytic distillation slip-off oil is mixed with distillate oil lower than 420°C, enters through the raw material pump, mixes with hydrogen, and then enters the hydrodewaxing reactor after being heated by a heat exchanger. The feed temperature is controlled at 380°C; the hydrogen partial pressure is 10MPa, and the volume Speed 0.5h -1 The volume ratio to hydrogen oil is 1000:1. The distillate after hydrofining is distilled under normal pressure and cut into gasoline (150°C, 220°C) according to the distillation temperature.
[0031] The yields and properties of liquid paraffin and gasoline and diesel obtained in this embodiment are shown in Tabl...
Embodiment 3
[0039]Shale oil is cut into distillate oil and residual oil below 420°C by vacuum distillation. The residual oil is injected into the catalytic distillation tower, and the temperature of the kettle is controlled at 450°C. The distilled oil and gas are contacted with molecular sieve / alumina catalyst for reaction and rectification. Catalytic distillation slip-off oil is mixed with distillate oil lower than 420°C, enters through the raw material pump, mixes with hydrogen, and then enters the hydrodewaxing reactor after being heated by a heat exchanger. The feed temperature is controlled at 360°C; the hydrogen partial pressure is 12MPa, and the volume Speed 0.5h -1 The volume ratio of hydrogen to oil is 600:1. The distillate after hydrofining is distilled under normal pressure and cut into gasoline (150°C, 220°C) according to the distillation temperature.
[0040] The yields and properties of liquid paraffin and gasoline and diesel obtained in this embodiment are shown in Tab...
PUM
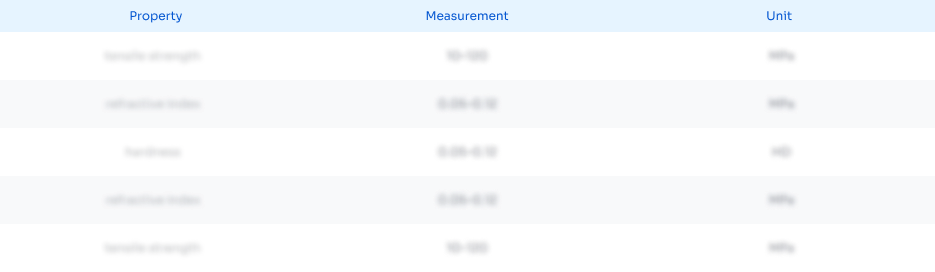
Abstract
Description
Claims
Application Information

- Generate Ideas
- Intellectual Property
- Life Sciences
- Materials
- Tech Scout
- Unparalleled Data Quality
- Higher Quality Content
- 60% Fewer Hallucinations
Browse by: Latest US Patents, China's latest patents, Technical Efficacy Thesaurus, Application Domain, Technology Topic, Popular Technical Reports.
© 2025 PatSnap. All rights reserved.Legal|Privacy policy|Modern Slavery Act Transparency Statement|Sitemap|About US| Contact US: help@patsnap.com