Batch hot-dip galvanizing chromium-free passivator and application method thereof
A chromium-free passivation agent, hot-dip galvanizing technology, applied in the direction of metal material coating process, etc., can solve the problems of high cost, inability to practically apply industrial production, and complex chromium-free passivation process.
- Summary
- Abstract
- Description
- Claims
- Application Information
AI Technical Summary
Problems solved by technology
Method used
Examples
Embodiment 1
[0049] Prepare 1L of chromium-free passivation agent for batch hot-dip galvanizing passivation treatment.
[0050] Take benzotriazole 50g, tannic acid 120g, hydroxyethylene diphosphonic acid 100g, EDTA-2 sodium salt 5g, sodium nitrate 5g, hydrogen peroxide 5g, sodium bisulfate 30g, nitric acid 15g, Phosphoric acid 50g, sodium dodecylbenzene sulfonate 5g, and the rest are water, and the above-mentioned components are prepared into a chromium-free passivator. Add 1L of prepared chromium-free passivator to 20L of water at a ratio of 1:20 to make a passivation solution. The passivation solution is at room temperature and has a pH value of 1.6. After the sample is hot-dip galvanized, it is directly immersed in the passivation solution or immersed in the passivation solution after water cooling, and the passivation time is 20s. The passivated samples were air-dried and aged at room temperature for 24 hours. The above-mentioned flow process does not change in any way to the existi...
Embodiment 2
[0053] Prepare 1L of chromium-free passivation agent for batch hot-dip galvanizing passivation treatment.
[0054]Take 10g of diaminotriazole, 10g of tartaric acid, 100g of hydroxyethylidene diphosphonic acid, 140g of phytic acid, 5g of aminotrimethylene phosphonic acid, 15g of sodium nitrate, 15g of sodium chlorate, 15g of nitric acid, 60g of phosphoric acid, nonylphenol Polyoxyethylene ether 5g, all the other are water, and above-mentioned each component is assigned to make chromium-free passivating agent. Add 1L of prepared chromium-free passivator to 20L of water at a ratio of 1:20 to make a passivation solution. The passivation solution is at room temperature and has a pH of 1.8. After the sample is hot-dip galvanized, it is directly immersed in the passivation solution or immersed in the passivation solution after water cooling, and the passivation time is 20s. The passivated samples were air-dried and aged at room temperature for 24 hours. The above-mentioned flow pr...
Embodiment 3
[0057] Prepare 1L of chromium-free passivation agent for batch hot-dip galvanizing passivation treatment.
[0058] Take 50g of dodecyldimethylbenzyl ammonium bromide, 15g of tetraethylammonium bromide, 110g of phytic acid, 80g of hydroxyethylidene diphosphonic acid, 40g of tannic acid, ethylenediaminetetraacetic acid-2 sodium salt 8g, thiourea 6g, sodium chlorate 5g / L, potassium permanganate 5g, nitric acid 20g, sodium bisulfate 40g, phosphoric acid 40g, nonylphenol polyoxyethylene ether 7g, N.N-bishydroxyethyl alkylamide 6g, The rest is water; the above-mentioned components are prepared into a chromium-free passivation agent. Add 1L of prepared chromium-free passivator to 20L of water at a ratio of 1:20 to make a passivation solution. The passivation solution is at room temperature and has a pH value of 1.6. After the sample is hot-dip galvanized, it is directly immersed in the passivation solution or immersed in the passivation solution after water cooling, and the passiva...
PUM
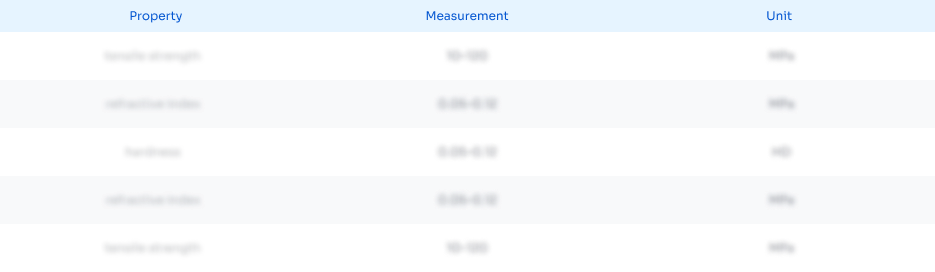
Abstract
Description
Claims
Application Information

- R&D
- Intellectual Property
- Life Sciences
- Materials
- Tech Scout
- Unparalleled Data Quality
- Higher Quality Content
- 60% Fewer Hallucinations
Browse by: Latest US Patents, China's latest patents, Technical Efficacy Thesaurus, Application Domain, Technology Topic, Popular Technical Reports.
© 2025 PatSnap. All rights reserved.Legal|Privacy policy|Modern Slavery Act Transparency Statement|Sitemap|About US| Contact US: help@patsnap.com