Stable zirconia ceramic target material for electron beam physic vapor deposition, and its preparation method
A technology for physical vapor deposition and stabilization of zirconia, which is applied in the field of ceramic material preparation, can solve the problems of inability to meet high-performance EB-PVD coatings, the deviation of coating composition and phase structure from the design value, and the difficulty in controlling density and impurities. Achieve the effect of shortening the sintering time, avoiding secondary recrystallization, and improving the utilization rate of powder
- Summary
- Abstract
- Description
- Claims
- Application Information
AI Technical Summary
Problems solved by technology
Method used
Image
Examples
Embodiment 1
[0026] ZrO 2 (purity 99.9%) and Y 2 o 3 (Purity 99.99%) Proportion according to mass ratio 92:8, and weigh. The raw materials used to prepare 10kg ceramic powder are: ZrO 2 9.2kg, Y 2 o 3 0.8kg. Put the weighed raw materials into a stirring ball mill, add an appropriate amount of deionized water with a material-to-ball ratio of 1:2, and a material-to-water ratio of 5:3, and use zirconia balls as grinding bodies for ball milling for 10 hours. The slurry was dehydrated by a filter press, put into an oven, and dried at a temperature of 80° C. for 20 hours to obtain a raw meal powder. The raw meal powder was added to the starch powder with a mass fraction of 4%, and calcined at 1550°C for 15 hours, and the sintering atmosphere was an oxidizing atmosphere to obtain clinker blocks. The clinker block is crushed to less than 1 mm, put into a polyurethane ball mill tank, and wet-milled with deionized water for 18 hours, the ratio of material to ball is 1:2, and the ratio of mate...
Embodiment 2
[0028] ZrO 2 (purity 99.9%), Ta 2 o 5 (purity 99.99%) and Y 2 o 3 (purity 99.99%) according to 16.6mol YO 1.5 : 17.6mol TaO 2.5 : 65.8molZrO 2 Proportion and weigh. The raw materials used to prepare 10kg ceramic powder are: ZrO 2 5.85kg, Y 2 o 3 1.35kg, Ta 2 o 5 2.80 kg. Put the weighed oxide raw materials into a stirring ball mill, add an appropriate amount of deionized water, the material-to-ball ratio is 1:2, and the material-to-water ratio is 5:3, and use zirconia balls as grinding bodies for ball milling for 12 hours. The slurry was dehydrated by a filter press, put into an oven, and dried at a temperature of 95° C. for 18 hours to obtain a raw meal powder. The raw meal powder was added to the starch powder with a mass fraction of 6%, and calcined at 1600°C for 12.5 hours, and the sintering atmosphere was an oxidizing atmosphere to obtain clinker blocks. The clinker block is crushed to less than 1 mm, put into a polyurethane ball mill tank, and deionized wat...
Embodiment 3
[0030] ZrO 2 (purity 99.9%), Ta 2 o 5 (purity 99.9%) Y 2 o 3 (purity 99.99%) and Sm 2 o 3 (purity 99.99%), according to 2molSmO 1.5 : 14.6mol YO 1.5 : 17.6mol TaO 2.5 : 65.8molZrO 2 Proportion and weigh. The raw materials used to prepare 10kg ceramic powder are: ZrO 2 5.79kg, Y 2 o 3 1.18kg, Ta 2 o 5 2.78 kg, Sm 2 o 3 0.25kg. Put the weighed raw materials into a stirring ball mill, add an appropriate amount of deionized water, and use zirconia balls as grinding bodies for ball milling for 11 hours. The material-to-ball ratio is 1:2, and the material-to-water ratio is 5:3. The slurry is dehydrated by a filter press, put into an oven, and dried at a temperature of 100° C. for 20 hours to obtain a raw meal powder. Add raw meal powder to starch powder with a mass fraction of 5%, calcined at 1580°C for 15 hours, and the sintering atmosphere is an oxidizing atmosphere to obtain clinker blocks. The clinker block is crushed to less than 1 mm, put into a polyurethane...
PUM
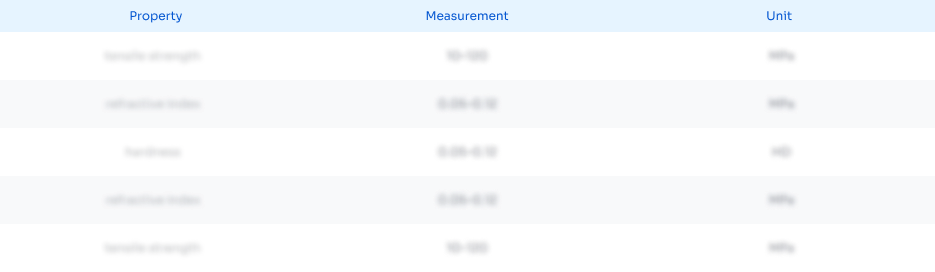
Abstract
Description
Claims
Application Information

- R&D
- Intellectual Property
- Life Sciences
- Materials
- Tech Scout
- Unparalleled Data Quality
- Higher Quality Content
- 60% Fewer Hallucinations
Browse by: Latest US Patents, China's latest patents, Technical Efficacy Thesaurus, Application Domain, Technology Topic, Popular Technical Reports.
© 2025 PatSnap. All rights reserved.Legal|Privacy policy|Modern Slavery Act Transparency Statement|Sitemap|About US| Contact US: help@patsnap.com