Low-density halogen-free flame retardant monocomponent titanate catalyzed room-temperature vulcanized silicone rubber and preparation method thereof
A technology of vulcanizing silicone rubber and catalyzing room temperature. It is applied in the direction of chemical instruments and methods, and other chemical processes. It can solve problems such as high viscosity, phase separation between filler and base rubber, and poor processing performance, so as to achieve low density and improve compatibility. , the effect of a wide range of viscosity adjustable
- Summary
- Abstract
- Description
- Claims
- Application Information
AI Technical Summary
Problems solved by technology
Method used
Examples
Embodiment 1
[0054] Preparation of modified α, ω-dihydroxy polydimethylsiloxane
[0055] in N 2 Under protection, 1000 parts of 1500 mPa·s α, ω-dihydroxy polydimethylsiloxane, 100 parts of tetramethoxysilane, 5 parts of capping catalyst calcium carbonate (or zinc carbonate, zinc oxide) were added to the reaction In the container, stir and react at 130°C for 6h (according to the difference in the capping reaction catalyst and the amount of tetramethoxysilane added, those skilled in the art can properly adjust the reaction temperature and time), and then at 100°C, Under the condition of vacuum degree>-0.09MPa, the low boilers and excess tetramethoxysilane are removed to obtain the modified α,ω-dihydroxy polydimethylsiloxane with the structural formula I.
Embodiment 2
[0057] Preparation of Modified α-Hydroxy-ω-Methyl Dimethicone
[0058] in N 2 Under protection, 500 parts of 50 mPa·s α-hydroxy-ω-methyl polydimethylsiloxane, 100 parts of tetramethoxysilane, 5 parts of calcium carbonate (or zinc carbonate, zinc oxide) of the capping catalyst Add it into the reaction container, and stir the reaction at 130°C for 6h (according to the difference of the capping reaction catalyst and the amount of tetramethoxysilane added, those skilled in the art can properly adjust the reaction temperature and time), and then at 100 °C, vacuum >-0.09MPa, low boilers and excess tetramethoxysilane are removed to obtain modified α-hydroxy-ω-methyl polydimethylsiloxane with structural formula II.
Embodiment 3
[0060] Add 200 parts of modified α-hydroxy-ω-methylpolydimethylsiloxane, 150 parts of aluminum hydroxide, 10 parts of acetylene carbon black, and 20 parts of gas-phase titanium dioxide into the high-speed dispersion mixer, at a vacuum degree >-0.09 Mix under the condition of MPa, and then break the vacuum with nitrogen, under the protection of nitrogen, stir and react at 120°C for 2h, then remove the low boilers at this temperature and vacuum >-0.09MPa and cool to room temperature, nitrogen Break the vacuum, add 1000 parts of the above-mentioned modified α, ω-dihydroxy polydimethylsiloxane, and stir for 10 minutes under the condition of vacuum degree >-0.09MPa; then add 40 parts of fumed white carbon black, Stir for 15min under the condition of -0.09MPa; finally add 30 parts of methyltrimethoxysilane, 20 parts of ethyl acetoacetate chelate of isopropyl titanate, silane coupling agent (aminopropyltriethoxysilane and ring 10 parts of oxypropoxypropyl trimethoxysilane according t...
PUM
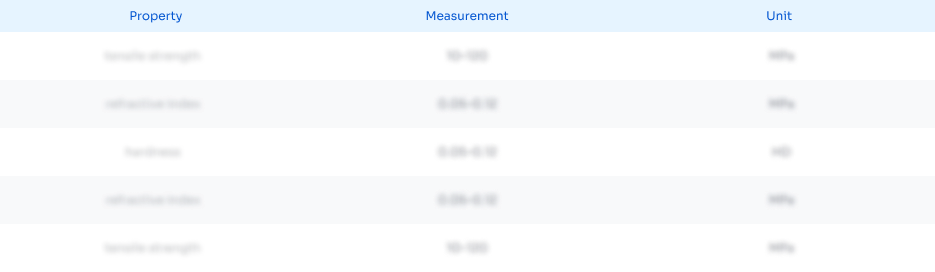
Abstract
Description
Claims
Application Information

- R&D Engineer
- R&D Manager
- IP Professional
- Industry Leading Data Capabilities
- Powerful AI technology
- Patent DNA Extraction
Browse by: Latest US Patents, China's latest patents, Technical Efficacy Thesaurus, Application Domain, Technology Topic, Popular Technical Reports.
© 2024 PatSnap. All rights reserved.Legal|Privacy policy|Modern Slavery Act Transparency Statement|Sitemap|About US| Contact US: help@patsnap.com