Method for producing terephthalic acid through oxidation of p-xylene by using air based on gas-liquid-solid heterogeneous reaction separation synchronizing reactor
A terephthalic acid, multiphase reaction technology, applied in the production of bulk chemicals, chemical instruments and methods, separation/purification of carboxylic acid compounds, etc., can solve the problems of high energy consumption, difficult operation technology, and by-products, etc. problem, to achieve the effect of solving complex equipment structure, high yield continuous production, and ensuring material balance
- Summary
- Abstract
- Description
- Claims
- Application Information
AI Technical Summary
Problems solved by technology
Method used
Image
Examples
Embodiment 1
[0037] use figure 1 The shown gas-liquid-solid multiphase reaction separation synchronous reactor carries out the air oxidation of p-xylene to prepare terephthalic acid products; wherein, the diameter-to-height ratio of the bubbling gravity reaction tower is 1:20; the ratio of the length of the gravity settling plate to the diameter of the tower is 1:0.8; The included angle of gravity settling plate tilted along the tower axis is 75°; there are two constant temperature settling towers Ⅰ and Ⅱ; the outlet of the reaction liquid is 2 / 5 of the height of the tower body from the top of the reaction tower place.
[0038] Add cobalt acetate (concentration of 200ppm) and manganese acetate (concentration of 200ppm) into the p-xylene raw material with water content of 3wt% as a composite catalyst, and the mixed solution enters the constant temperature settling tower I from the upper reaction material inlet of the constant temperature settling tower I and bubbles The gravity reaction to...
Embodiment 2
[0042] Attached figure 1 The shown gas-liquid-solid multiphase reaction separation synchronous reactor carries out the air oxidation of p-xylene to prepare terephthalic acid products; wherein, the diameter-to-height ratio of the bubbling gravity reaction tower is 1:40; the ratio of the length of the gravity settling plate to the diameter of the tower is 1:1.2; The included angle of gravity settling plate tilted along the tower axis is 45°; there are two constant temperature settling towers Ⅰ and Ⅱ; the outlet of the reaction liquid is 3 / 7 of the height of the tower body from the top of the reaction tower place.
[0043] Add cobalt acetate (concentration of 400ppm) and copper tetraphenylporphyrin (concentration of 10ppm) into the p-xylene raw material with water content of 5wt% as composite catalyst, and the mixed solution enters the constant temperature settling tower from the upper reaction material inlet of constant temperature settling tower I Ⅰ and the bubbling gravity re...
Embodiment 3
[0047] Attached figure 1 The shown gas-liquid-solid multiphase reaction separation synchronous reactor carries out the air oxidation of p-xylene to prepare terephthalic acid products; wherein, the diameter-to-height ratio of the bubbling gravity reaction tower is 1:35; the ratio of the length of the gravity settling plate to the diameter of the tower 1:1.2; The included angle of gravity settling plate tilted along the tower axis is 55°; there are two constant temperature settling towers I and II; the outlet of the reaction liquid is 3 / 7 of the height of the tower body from the top of the reaction tower place.
[0048] Add tetraphenylporphyrin cobalt (concentration: 8ppm) and tetra-p-chlorophenylporphyrin iron (concentration: 8ppm) into p-xylene raw material as composite catalyst, and the mixed solution enters from the reaction material inlet on the upper part of constant temperature settling tower I The constant temperature settling tower Ⅰ and the bubbling gravity reaction t...
PUM
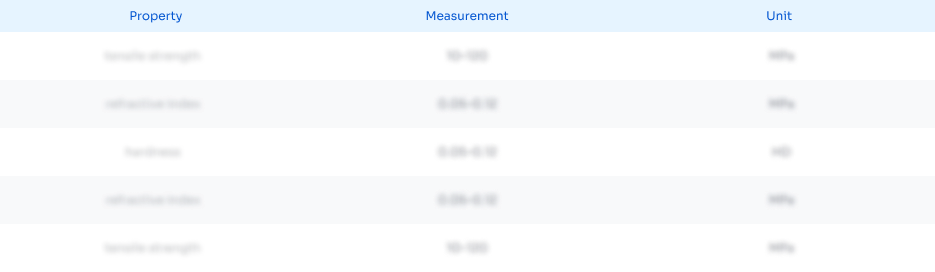
Abstract
Description
Claims
Application Information

- R&D
- Intellectual Property
- Life Sciences
- Materials
- Tech Scout
- Unparalleled Data Quality
- Higher Quality Content
- 60% Fewer Hallucinations
Browse by: Latest US Patents, China's latest patents, Technical Efficacy Thesaurus, Application Domain, Technology Topic, Popular Technical Reports.
© 2025 PatSnap. All rights reserved.Legal|Privacy policy|Modern Slavery Act Transparency Statement|Sitemap|About US| Contact US: help@patsnap.com