Chromium-molybdenum low-alloy prestress aluminum-cladding steel wire manufacturing method
A chromium-molybdenum low-alloy, aluminum-clad steel wire technology, applied in the direction of manufacturing tools, furnace types, furnaces, etc., can solve problems such as delayed cracks, corrosion service life, steel strand cracks, etc., to reduce deformation and cracking, improve durability Corrosion performance, effect of prolonging service life
- Summary
- Abstract
- Description
- Claims
- Application Information
AI Technical Summary
Problems solved by technology
Method used
Examples
Embodiment 1
[0028] A method for manufacturing chromium-molybdenum low-alloy prestressed aluminum-clad steel wire provided in this embodiment includes the following specific steps:
[0029] Step (1): Using chromium-nickel-molybdenum alloy structural steel as a blank, the chromium-nickel-molybdenum alloy structural steel includes the following components in mass percentages: carbon: 0.28%, silicon: 0%, manganese: 0%, chromium: 0.80%, Nickel: 3.00%, Molybdenum: 0.40%, Phosphorus: 0%, Sulfur: 0%, Hydrogen: 1.0ppm, Vanadium: 0.10%, Titanium: 0%, Copper: 0%, Aluminum: 0%, 0% residual elements, The rest is Fe;
[0030] Smelt and finish-roll the above-mentioned billet to a steel wire billet of the required size, the smelting temperature is 800°C;
[0031] Step (2): Perform hydrogen expansion heat treatment on the steel wire blank obtained in step (1), which specifically includes: heating the steel wire blank obtained in step (1) to 870°C and keeping it for 360 minutes, air cooling to 290°C and k...
Embodiment 2
[0039] This embodiment provides a method for manufacturing chromium-molybdenum low-alloy prestressed aluminum-clad steel wire, including the following specific steps:
[0040] Step (1): Using chromium-nickel-molybdenum alloy structural steel as a blank, the chromium-nickel-molybdenum alloy structural steel includes the following components in mass percentages: carbon: 0.38%, silicon: 0.35%, manganese: 0.90%, chromium: 1.50%, Nickel: 4.00%, Molybdenum: 0.60%, Phosphorus: 0.015%, Sulfur: 0.015%, Hydrogen: 2.0ppm, Vanadium: 0.20%, Titanium: 0.025%, Copper: 0.20%, Aluminum: 0.05%, 0-0.50% residual element, the rest is Fe;
[0041]Smelt and finish-roll the above-mentioned billet to a steel wire billet of the required size, the smelting temperature is 850°C;
[0042] Step (2): Perform hydrogen expansion heat treatment on the steel wire blank obtained in step (1), which specifically includes: heating the steel wire blank obtained in step (1) to 890°C for 360 minutes, air cooling to ...
Embodiment 3
[0049] This embodiment provides a method for manufacturing chromium-molybdenum low-alloy prestressed aluminum-clad steel wire, including the following specific steps:
[0050] Step (1): Using chromium-nickel-molybdenum alloy structural steel as a blank, the chromium-nickel-molybdenum alloy structural steel includes the following components in mass percentages: 0.3% carbon, 0.3% silicon, 0.80% manganese, 1.20% chromium, 3.50% nickel, 0.50% molybdenum, 0.01% phosphorus, 0.01% sulfur, 1.0ppm hydrogen, 0.15% vanadium, 0.02% titanium, 0.15% copper, 0.03% aluminum, 0-0.50% residual elements, the rest is Fe;
[0051] Smelt and finish roll the above-mentioned billet to the steel wire billet of the required size, the smelting temperature is 825°C;
[0052] Step (2): Perform hydrogen expansion heat treatment on the steel wire blank obtained in step (1), which specifically includes: heating the steel wire blank obtained in step (1) to 880°C for 360 minutes, air cooling to 300°C for 180 m...
PUM
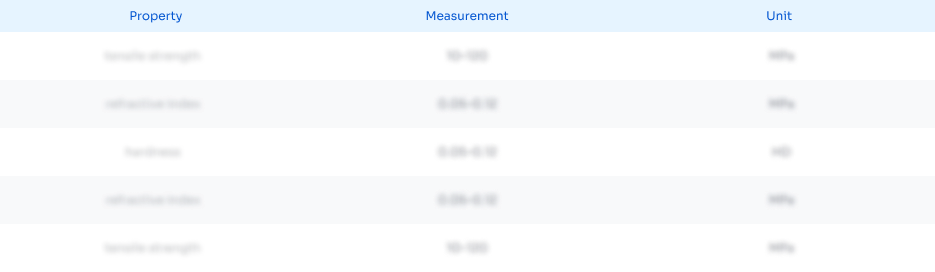
Abstract
Description
Claims
Application Information

- R&D
- Intellectual Property
- Life Sciences
- Materials
- Tech Scout
- Unparalleled Data Quality
- Higher Quality Content
- 60% Fewer Hallucinations
Browse by: Latest US Patents, China's latest patents, Technical Efficacy Thesaurus, Application Domain, Technology Topic, Popular Technical Reports.
© 2025 PatSnap. All rights reserved.Legal|Privacy policy|Modern Slavery Act Transparency Statement|Sitemap|About US| Contact US: help@patsnap.com