Vacuum melting and slab casting method of titanium-aluminum alloy
A vacuum smelting and titanium-aluminum alloy technology, which is applied in the field of titanium-aluminum alloy slab processing, can solve problems such as composition segregation, lack of uniform structure, and metallurgical defects.
- Summary
- Abstract
- Description
- Claims
- Application Information
AI Technical Summary
Problems solved by technology
Method used
Image
Examples
example
[0011] Process example: Titanium-aluminum alloy vacuum melting plus casting slab
[0012] 1. Preparation of electrodes:
[0013] 1) Raw material: Grade 0 titanium sponge (particle size 12.5~25.4mm)
[0014] Aluminum vanadium alloy (58% vanadium content)
[0015] Aluminum beans: (particle diameter less than 10mm)
[0016] The hydraulic press presses the approximate circular electrode block, with a density of more than 3.0 g / cm3. After pressing, use argon shielded plasma welding to weld the electrode block into an electrode to be melted.
[0017] 2. One-time smelting by vacuum self-consumption
[0018] Melting voltage: 25-37 volts
[0019] Current: 40-70 amps / square centimeter
[0020] Melting vacuum degree: 0.4~3 Pascal
[0021] One ingot casting:
[0022] The crucible is made of special metal composite material and is cooled by external water.
[0023] 3. Secondary smelting of vacuum shell
[0024] The primary ingot is melted twice in a 250kg vacuum shell furnace, a...
PUM
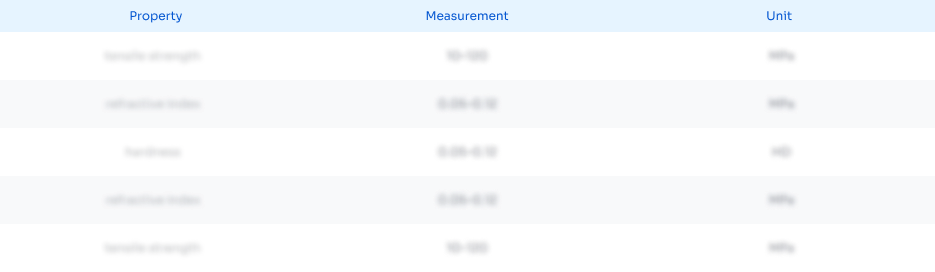
Abstract
Description
Claims
Application Information

- R&D
- Intellectual Property
- Life Sciences
- Materials
- Tech Scout
- Unparalleled Data Quality
- Higher Quality Content
- 60% Fewer Hallucinations
Browse by: Latest US Patents, China's latest patents, Technical Efficacy Thesaurus, Application Domain, Technology Topic, Popular Technical Reports.
© 2025 PatSnap. All rights reserved.Legal|Privacy policy|Modern Slavery Act Transparency Statement|Sitemap|About US| Contact US: help@patsnap.com